Integrating ERP Production Planning with Design Software for Customized Quilts
Customer Profile:
Customer is a home textile manufacturer known for catering to a diverse clientele with their specialized high-quality customized home textile products like quilts. They are renowned for their innovative designs and superior craftsmanship resulting in globally widespread presence.
Problem Statement:
With an increasing consumer base, the customer had to expand their production cycles. However, they faced significant challenges due to the lack of integration between their production planning and design software. Some of these challenges included:
- Miscommunications between design and production teams.
- Data gaps leading to delays in the manufacturing process.
- Increased errors in the final products.
- Difficulty in maintaining high standards of quality.
- Rising wastes due to inability to meet consumer demands.
These issues underscored the need for a textile industry software to enhance operational efficiency and ensure consistent product quality.
Solution:
To address these challenges, the customer decided to implement iTexClouds – a textile industry focused ERP software.
A significant part of the implementation mainly focused on integrating ERP production planning module with the customer’s design software. This integration offered comprehensive capabilities to streamline processes and improve coordination between design and production. The solution included:
- Real-time synchronization between design software and ERP production planning module.
- Automated updates of design changes directly into the production schedule.
- Enhanced communication channels between design and production teams.
- Detailed production planning and scheduling to accommodate customized orders.
- Comprehensive reporting and analytics to monitor and optimize the production process.
Results:
Integrating ERP production planning with design software enabled our customer to enhance their operational efficiency, reduce errors, and deliver high-quality customized quilts to their customers. Some of the results of the implementation include:
- Production errors reduced by 30%, resulting in higher product quality.
- Manufacturing lead times decreased by 20%, ensuring timely delivery.
- Improved coordination between design and production teams, enhancing overall efficiency.
- Customer satisfaction increased by 50-70% due to the consistent quality of customized quilts.
- Operational costs were reduced by 15% due to more efficient production planning.
Contact Us
So, what are you waiting for? Don’t let your competition get ahead of you. Contact us today to discuss your textile ERP needs and let us help you achieve your business goals!
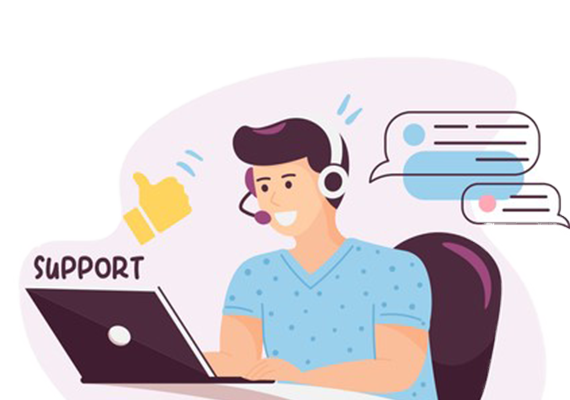