All Resources
Read and get updated on how we progress
- All Resources
- Blog
- Customer Story
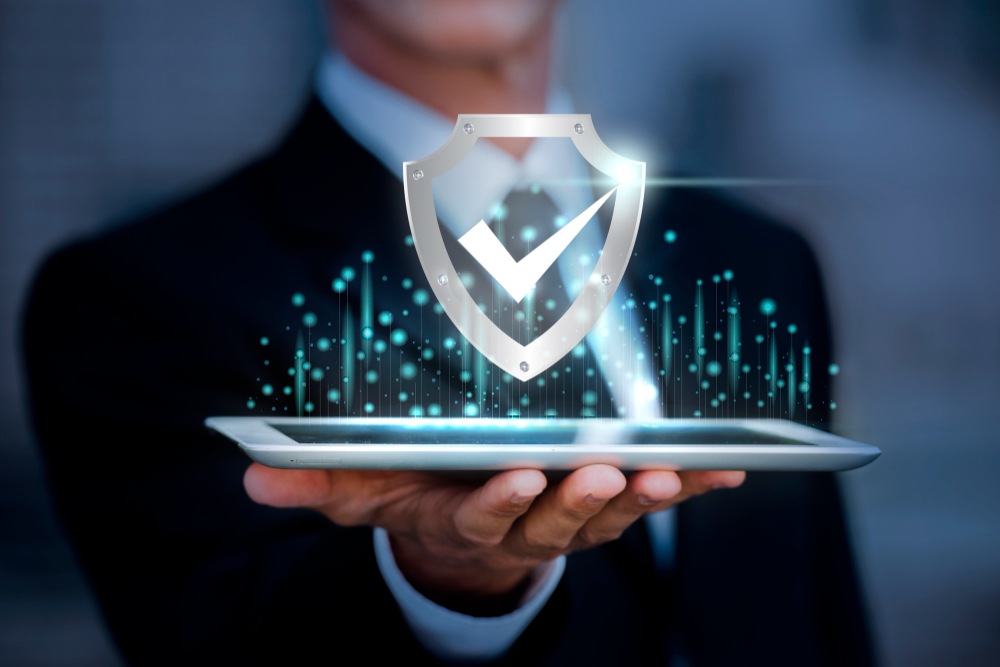
Every year 110 million tons of textile waste is produced across the world by the textile industry. In efforts to take a step towards sustainability and reduce excess waste, businesses are implementing various textile industry standards such as labor practices, ESG standards, quality control, etc.
To implements these standards efficiently, an ERP software becomes a requirement. In this blog we are going to understand the role of ERP compliance in a textile business and what main features does the compliance management ERP software offer. Let’s get started.
Understanding Role of ERP Compliance in the Textile Industry
In the textile business, ensuring ERP compliance is essential for upholding regulatory standards, enhancing operational effectiveness, and attaining sustainable growth via streamlined procedures and strong quality control. Let us see in detail the different ERP compliance standards and how they help in promoting sustainability and efficiency in textile production and waste management.
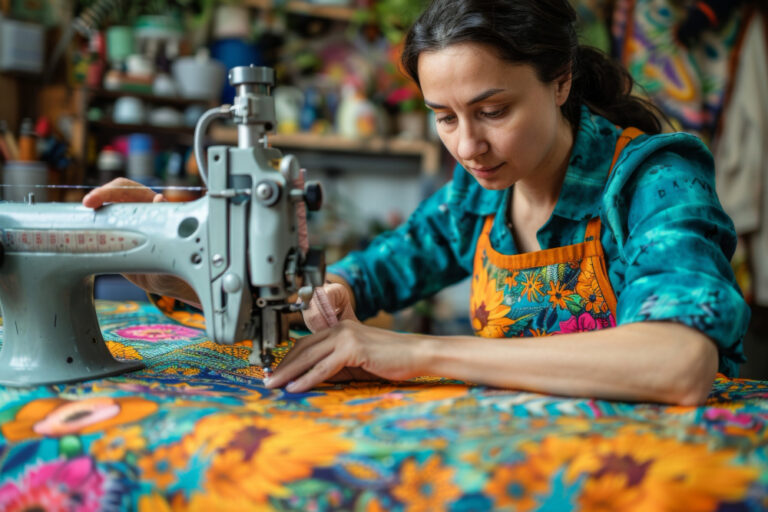
1] Labor Practices: Ensuring compliance in labor practices is essential for maintaining ethical standards and avoiding legal repercussions. Labor practices in the textile industry are regulated to ensure fair treatment, safety, and rights for workers. ERP compliance involves adhering to:
- Wage Laws
- Providing safe working conditions
- Prohibiting child and forced labor
By implementing fair labor practices, textile companies can easily prevent exploitation, improve worker satisfaction, and foster a transparent and respectful workplace culture.
2] Environmental Standards: Compliance with environmental standards not only protects the planet but also builds a company’s reputation as a responsible and eco-friendly business. ERP compliance for meeting environmental standards in the textile industry focus on reducing pollution, conserving resources, and promoting sustainable practices. This results in:
- Proper waste management
- Emission control
- Efficient use of water, energy, and raw materials
By following these regulations through ERP software, textile businesses can minimize their environmental footprint, enhance sustainability, and meet regulatory requirements.
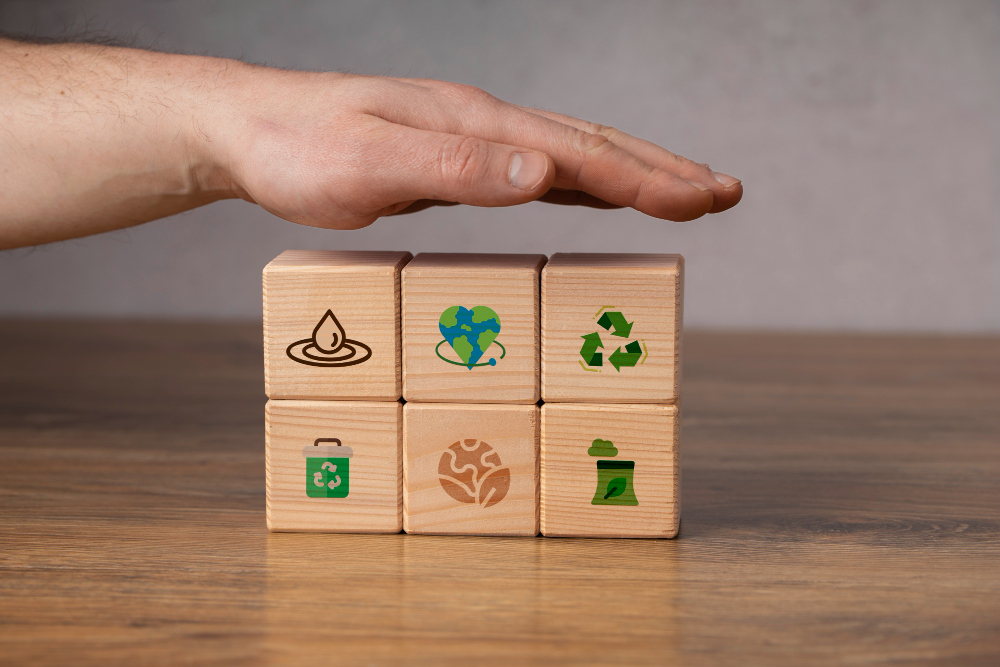
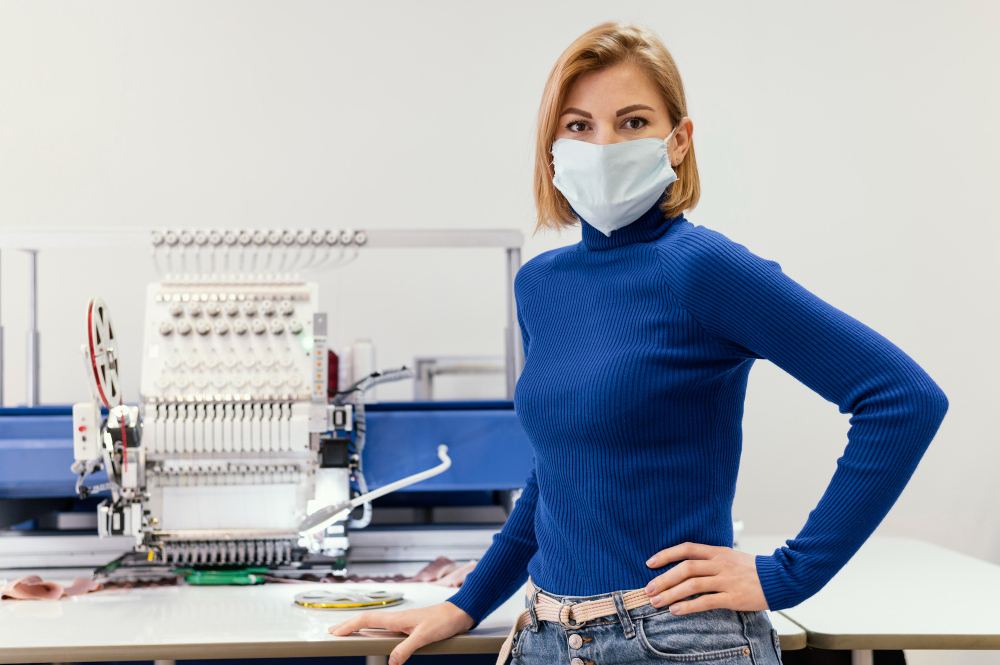
3] Quality Control Regulations: Compliance in quality control is critical for maintaining consumer safety, satisfaction, and brand integrity, ultimately leading to long-term business success. ERP Quality control regulations ensure that textile products meet safety, durability, and performance standards. The textile industry standards for this involves:
- Strict testing for harmful substances
- Adherence to durability metrics
- Accurate product labelling
By meeting quality control regulations, companies can prevent product recalls, enhance customer trust, and ensure that products consistently meet or exceed industry standards.
Key Features of ERP Software for Meeting Textile Industry Standards
In this section, we are going to learn about key ERP capabilities that support textile businesses in adhering to quality, labor, regulatory, and environmental standards while maintaining effective and compliant operations.
Here are 5 main features of compliance management ERP software:
1] Regulatory Compliance Modules: The regulatory compliance module in the ERP software is specifically designed to help textile businesses meet industry-specific regulations and standards. Implementing these modules allow textile manufacturers to stay updated with evolving regulations and ensure all processes are compliant. This helps to avoid legal penalties and enhance operational transparency.
Tools for tracking regulatory changes, maintaining documentation, and guaranteeing timely reporting are provided by this module. They assist in automating processes such as keeping records, renewing licenses, and filing required papers. This lowers the possibility of human error.
2] Quality Management: Quality management module of ERP software help to establish and maintain high standards in textile production. By integrating quality management into ERP compliance, textile companies can ensure consistent product quality, reduce defects, and meet both regulatory requirements and customer expectations.
This module gives textile manufacturers the ability to quickly manage non-conformance reports, conduct inspections, and create quality goals. Features for carrying out precise quality checks at various phases of the textile production process are available in the software. This guarantees that goods fulfil durability and safety standards, which eventually raises customer satisfaction and lowers return rates.
3] ESG Compliance: Environmental, Social, and Governance (ESG) compliance is increasingly important for textile businesses aiming for sustainable and ethical operations. Implementing ESG compliance through an ERP software helps textile companies to manage environmental impact, social responsibility, and governance practices.
The ESG module helps track carbon footprint, resource consumption, waste management, and social initiatives. This allows textile companies to showcase their sustainability efforts, enhance their brand recognition, and draw in eco-aware investors and customers by utilizing ESG compliance modules.
4] Labor Management: ERP software's labor management feature is intended to guarantee compliance to labor laws and regulations. The labor management feature facilitates training programs and monitor employee performance and welfare. It also helps businesses manage employee information, track working hours, process payroll accurately, and ensure safe working conditions.
ERP labor management helps textile manufacturers to ensure fair wages, adhere to working hour regulations, and maintain a safe and supportive work environment. This compliance not only mitigates legal risks but also boosts employee morale and productivity.
5] Audit Trails: Audit trails are a critical feature of ERP systems for maintaining transparency and accountability. These trails provide a detailed log of all transactions, changes, and activities within the system, allowing businesses to track and review actions for compliance purposes. Audit trails help in identifying discrepancies, ensuring data integrity, and supporting internal and external audits.
By maintaining comprehensive audit trails, textile companies can enhance their ability to demonstrate compliance, quickly address issues, and ensure continuous improvement in their operations. This feature is essential for building trust with stakeholders and regulatory bodies.
Textile businesses need to use ERP software in order to keep up with industry norms. It guarantees ethical labor standards, sustainable environmental practices, and superior products. Operational efficiency and transparency are improved by the main features, which include labor management, regulatory compliance modules, quality management, ESG compliance, and audit trails. Textile businesses can increase productivity, lower risks, and establish a reliable brand by implementing ERP systems. Long-term success in the textile sector depends on this dedication to sustainability and compliance.
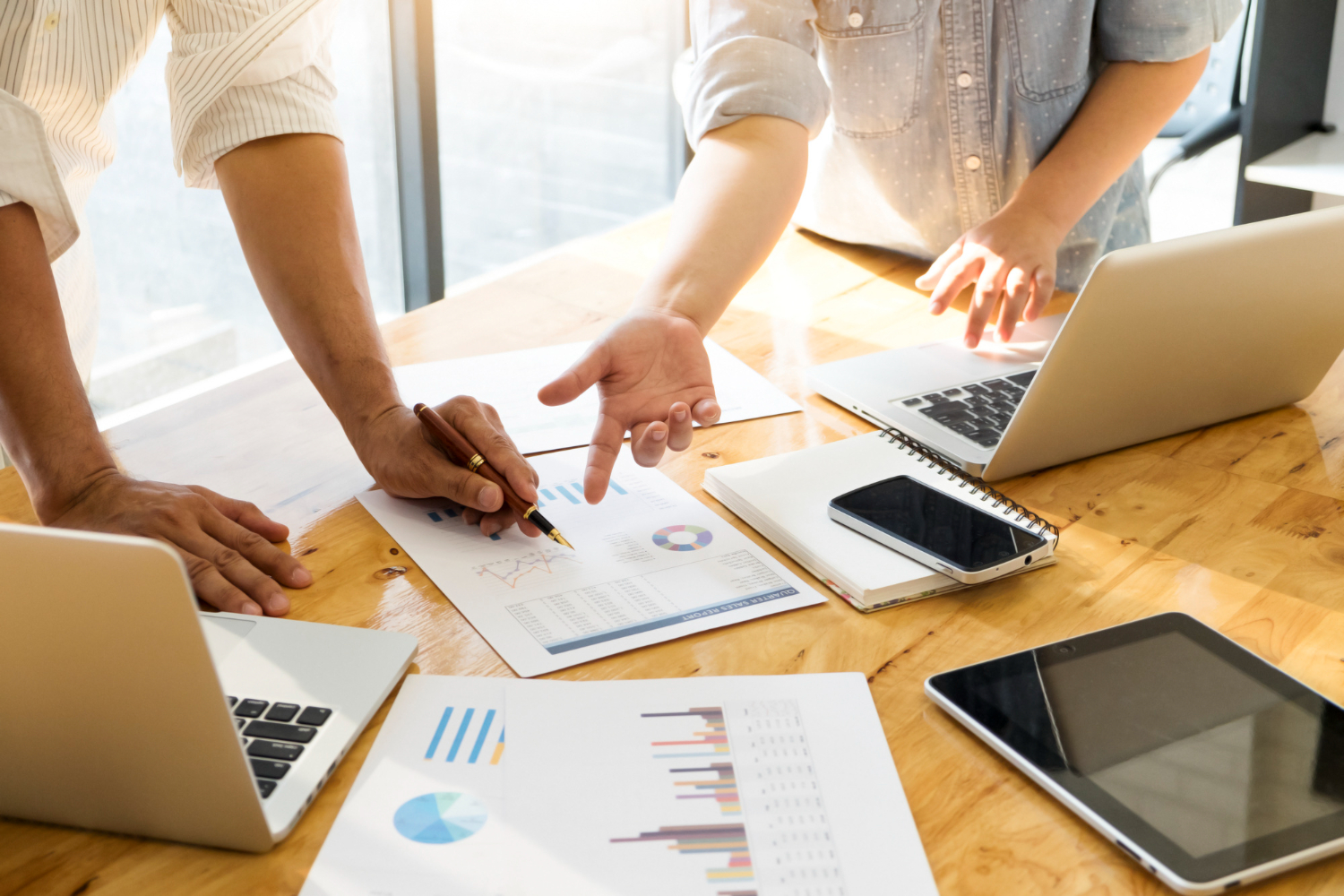
An efficient supply chain management is at the core of a competitive and successful textile business. However, given the vastness of the textile industry, co-ordinating every step from sourcing raw materials to delivering finished products can be challenging. This is where ERP systems that support textile supply chain management come into play.
ERP supply chain management helps textile manufacturers streamline their processes, reduce costs, and improve overall efficiency. In this blog, we will explore ERP supply chain benefits and why it is essential for textile manufacturers and delve into its key features.
Textile Supply Chain Management: Role of ERP
Textile manufacturers face unique challenges in managing their supply chains. The complexity of handling multiple suppliers, managing inventory, coordinating production schedules, and ensuring timely deliveries requires a robust system.
Traditional methods of managing these tasks are often inefficient and prone to errors. ERP textile supply chain management offers a solution by providing a centralized platform that integrates all aspects of the supply chain. This integration improves:
- Task Coordination
- Supply Chain Visibility
- Response time to demand changes
- Automation of Key Processes
With a well-implemented ERP system, textile manufacturers can better manage their logistics, resources, optimize production, and deliver products on time, ultimately improving their bottom line.
5 Key Features of ERP Supply Chain Management
An ERP software specializes in optimizing the entire textile supply chain with features that are designed to enhance efficiency, visibility, and coordination.
Let us discuss the 5 main features that make ERP software stand out when it comes to textile supply chain management:
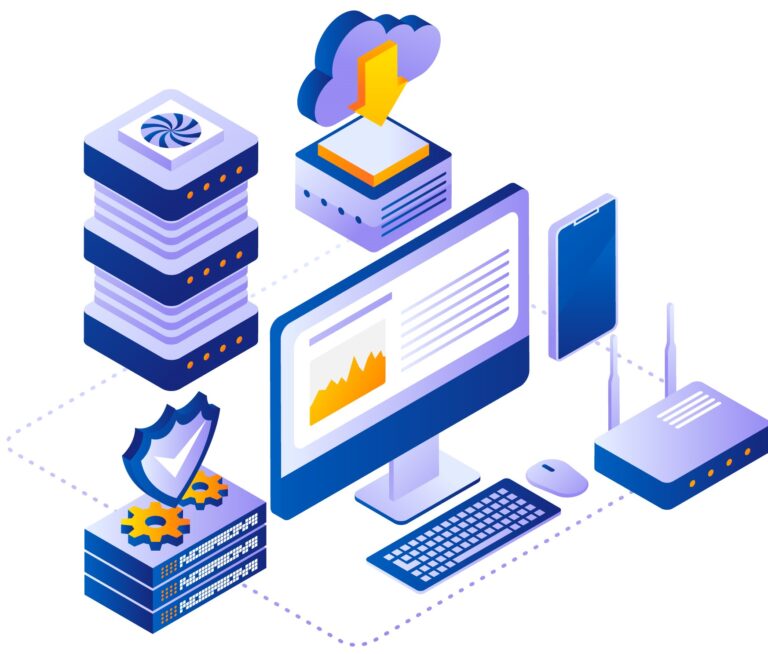
1] Centralized Supplier Database: One of the standout features of ERP supply chain management is the centralized supplier database. In the textile industry, managing relationships with multiple suppliers is a complicated task. With an ERP system, all supplier information is stored in a single, easily accessible database.
This centralization enables textile manufacturers to track supplier performance, manage contracts, and streamline procurement processes. The ability to quickly access accurate supplier data ensures that manufacturers can make timely decisions, avoid delays, and maintain strong relationships with their suppliers.
2] Increased Visibility: In the textile industry, having a clear view of the entire supply chain is essential for making sure that products are delivered on time and in the right quantities. Textile supply chain management software provide real-time visibility into every stage of the supply chain, from raw material procurement to final delivery.
This visibility allows manufacturers to identify potential bottlenecks, track shipments, and monitor inventory levels. By having a comprehensive view of the supply chain, manufacturers can quickly address issues before they escalate, ensuring smooth operations and timely deliveries.
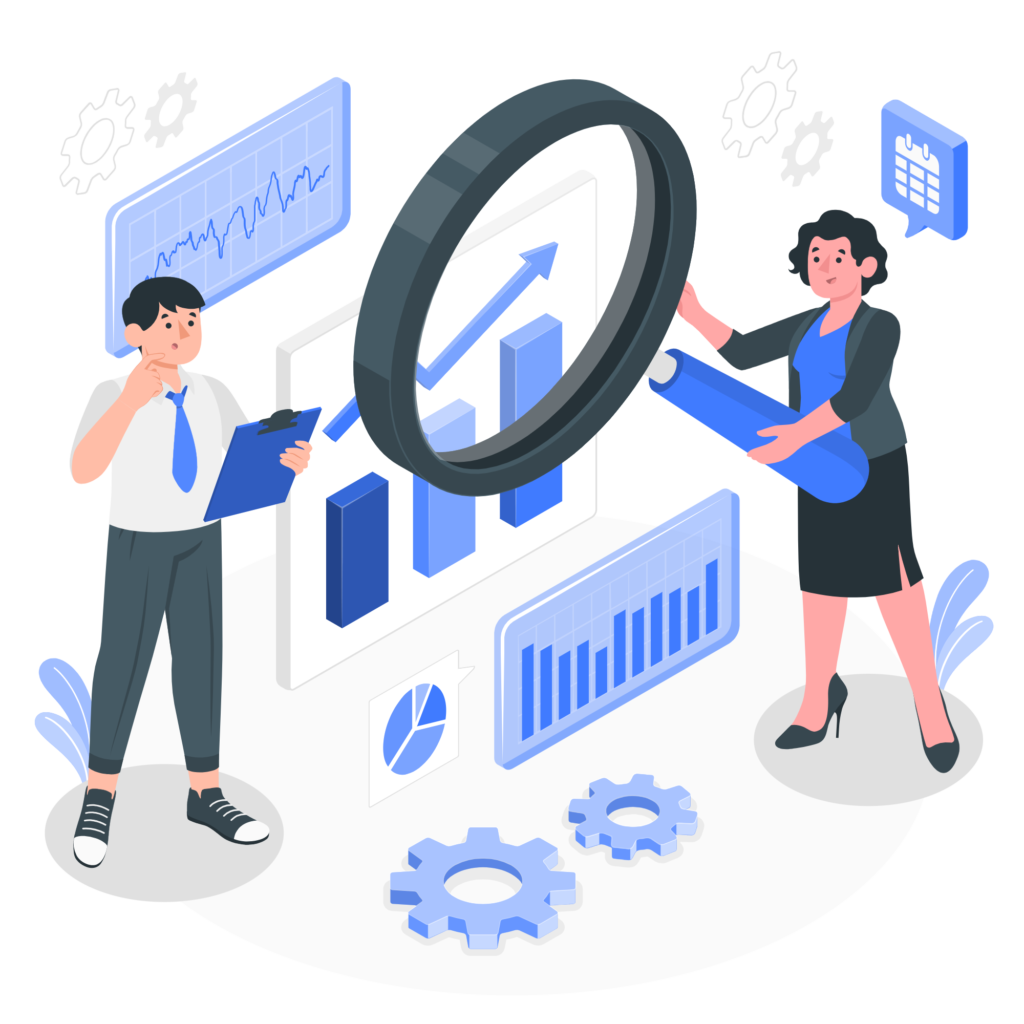
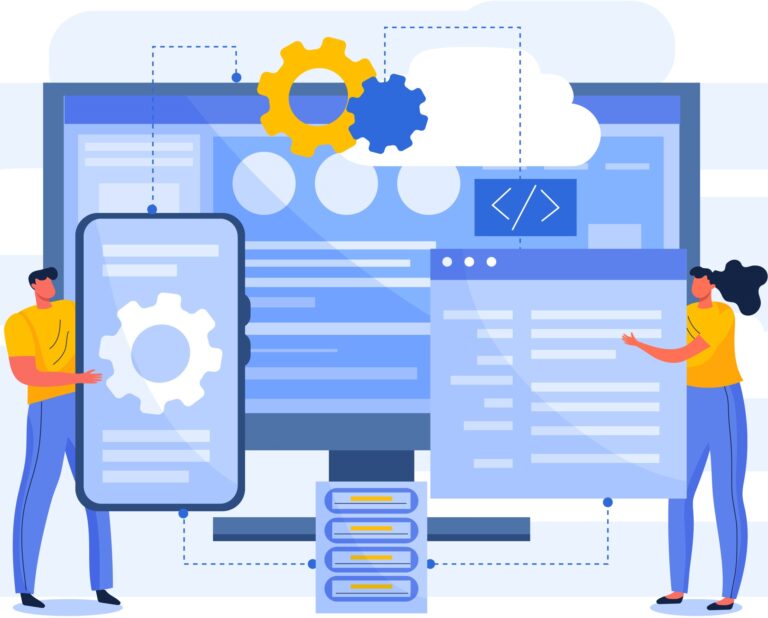
3] Automated Processes: One of the best supply chain ERP benefits is that it automates routine tasks that can save time and significantly improve overall efficiency. ERP systems automate key processes such as order processing, inventory management, and procurement.
Automation reduces the need for manual intervention, minimizing errors and speeding up operations. For example, when inventory levels fall below a certain threshold, the ERP system can automatically trigger a reorder, ensuring that stock levels are always optimal.
4] Integration of Supply Chain Functions: A textile business, as we know, comprises of different functions such as procurement, production, inventory management, and distribution. While these are often managed separately, they are highly interdependent. This usually leads to inefficiencies and communication gaps within the departments. Textile supply chain management software, like an ERP integrates these functions into a cohesive whole, enabling smooth communication and coordination.
For instance, when a production order is created, the ERP software automatically checks inventory levels and triggers procurement if necessary. This integration ensures that all departments such as inventory management, warehouse management, exports management, etc., are aligned.
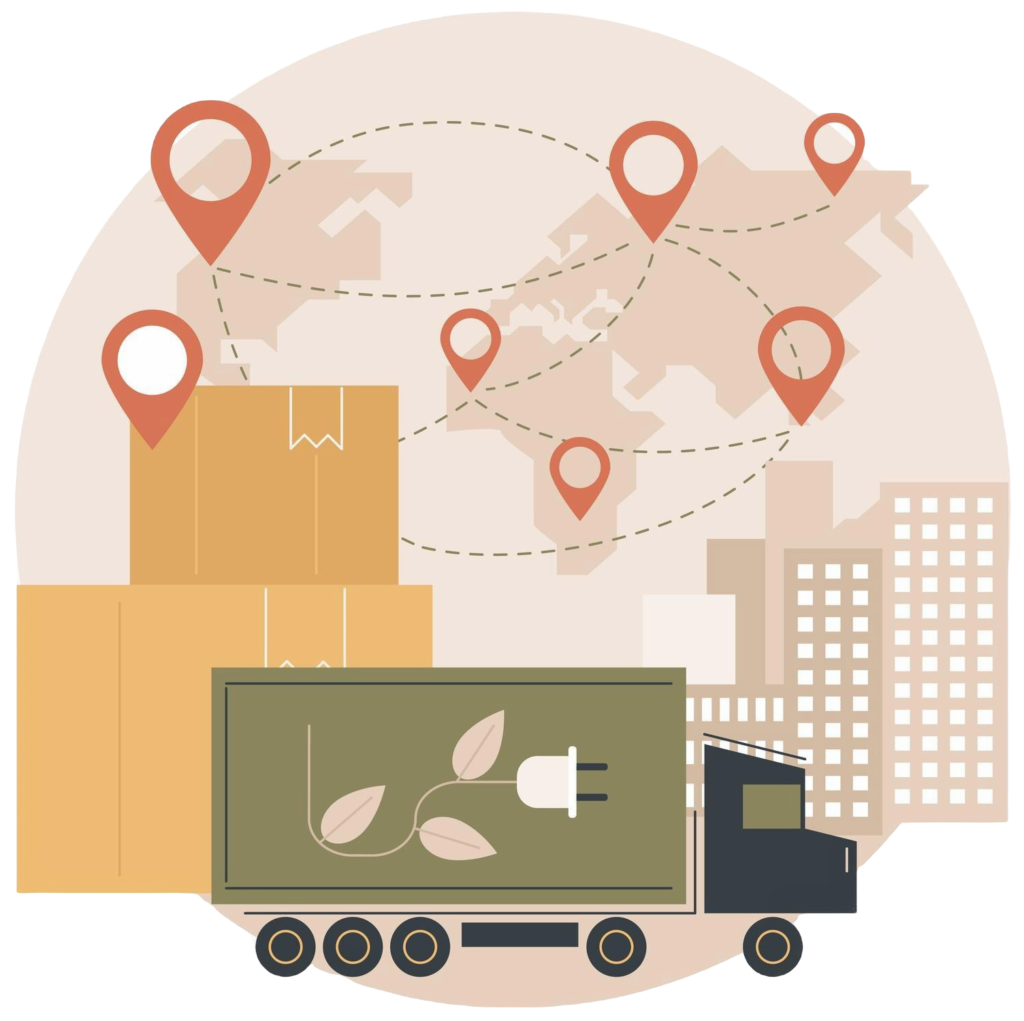
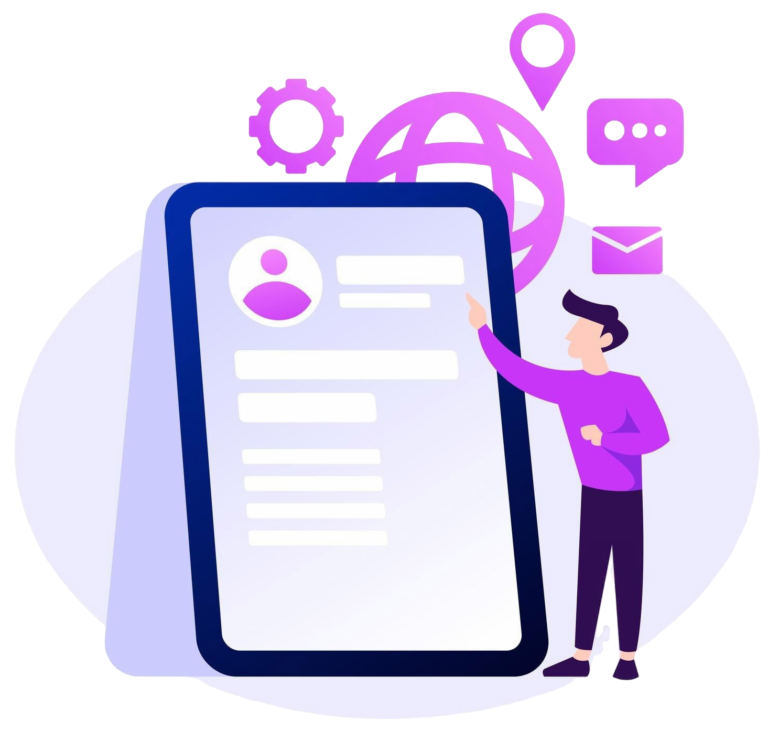
5] End-to-End Order Tracking: End-to-end order tracking is a feature that provides complete visibility into the order fulfilment process. In the textile industry, where customer satisfaction is a high priority, knowing the status of an order at any given time is essential. ERP supply chain management allows manufacturers to track orders from the moment they are placed until they are delivered to the customer.
This tracking includes every step, from raw material procurement to production, shipping, and final delivery. With this level of visibility, manufacturers can provide accurate updates to customers, resolve issues quickly, and ensure that orders are fulfilled on time.
Textile supply chain management ERP software is a powerful tool for manufacturers, offering a range of features that improve efficiency, reduce costs, and enhance visibility across the supply chain. By centralizing supplier data, providing real-time visibility, automating processes, integrating supply chain functions, and enabling end-to-end order tracking, ERP systems help manufacturers navigate the complexities of the textile industry. As competition intensifies and customer expectations continue to rise, adopting ERP supply chain management is no longer a luxury but a necessity for staying ahead in the market.

The textile industry is resource-intensive, often involving complex supply chains, high energy consumption, and significant waste generation. As per records, the industry produces 110 million tons of waste annually. And only 25% of it is recycled or reused.
Now with the growing need for sustainable textile manufacturing, businesses are becoming increasingly dependent on tools that not only help them optimize their processes but also help achieve sustainability goals.
ERP software with their advanced capabilities integrate various aspects of a textile manufacturing unit, from procurement to production, inventory management, and compliance. This allows business owners to get complete visibility and access real-time data, including insights on their environmental impact. Using these data, textile companies can ensure adherence to regulations, and make more sustainable choices at every stage of the production lifecycle.
5 Ways ERP Software Establishes Sustainable Textile Manufacturing
Implementing ERP software in textile manufacturing is a strategic move toward sustainability. This not helps them reduce textile waste with ERP but also enables them to streamline operations and ensure ethical practices.
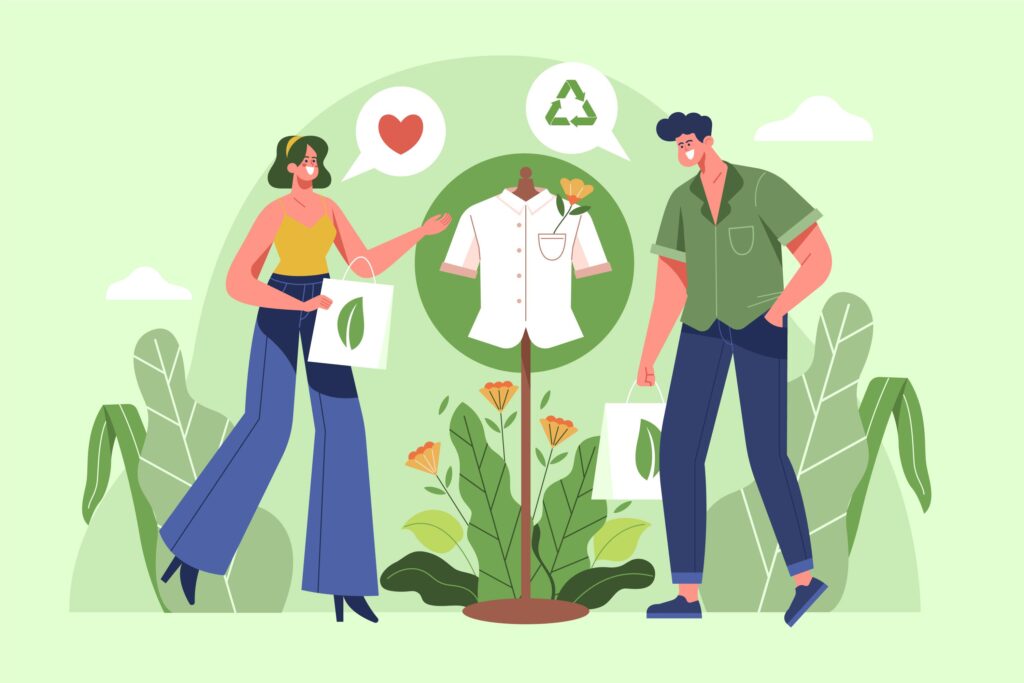
Here are five key ways ERP software helps with sustainable textile manufacturing:
1] Compliance and Reporting: Keeping up with environmental regulations is complex but ERP software simplifies the process by automating the tracking and reporting of compliance related data. With real-time access to key metrics, textile businesses can ensure they meet local and international environmental standards, reducing the risk of fines and reputational damage.
Furthermore, an ERP software can generate reports that highlight areas of improvement, enabling companies to take proactive steps toward reducing their environmental footprint.
2] Automating Workflows: Manual processes in textile manufacturing are time-consuming and prone to errors that can lead to waste. ERP software automates these workflows, reducing the likelihood of mistakes and optimizing resource utilization.
By automating tasks such as order processing, inventory management, and production scheduling, textile businesses lower expenditures and contribute to a more sustainable textile manufacturing.
3] Real-Time Monitoring: One of the key benefits of ERP software is its ability to provide real-time insights into daily operations. For textile manufacturers, this means having instant access to data on energy consumption, waste generation, and resource usage.
By tracking these metrics, businesses can identify inefficiencies and take immediate action to address them. Real-time monitoring also allows companies to measure the effectiveness of their sustainability initiatives, ensuring continuous improvement in their environmental performance.
4] Enhanced Supply Chain Transparency: Sustainability in the textile industry goes beyond just production processes. A truly sustainable textile business ensures compliance and accountability across the entire supply chain. ERP software plays a crucial role in enhancing supply chain transparency by offering comprehensive insights into the sourcing of raw materials, supplier sustainability practices, and transportation methods.
With this information, textile businesses can make informed decisions that prioritize ethical sourcing and reduce their environmental impact. By choosing suppliers that adhere to sustainable practices, companies can ensure that their products are not only high-quality but also environmentally friendly
5] Eco-Friendly Product Lifecycle Management: ERP software supports eco-friendly product lifecycle management by integrating sustainability into every stage of the product’s journey, from design to disposal. During the design phase, the software can help identify materials and processes that minimize environmental impact. Throughout production, ERP systems track the use of resources and energy, ensuring that sustainability goals are met.
Finally, the software can manage the disposal or recycling of products, ensuring that they are handled in an environmentally responsible manner. By considering the entire lifecycle, textile businesses can create products that are not only profitable but also sustainable.
In an industry where sustainability is increasingly becoming a necessity, ERP software offers textile businesses the tools they need to stay competitive while reducing their environmental impact. By streamlining operations, ensuring compliance, enhancing supply chain transparency, and supporting eco-friendly practices, ERP systems play a vital role in promoting sustainable textile manufacturing practices. As the industry continues to evolve, adopting ERP software will be key to achieving long-term environmental and economic success.
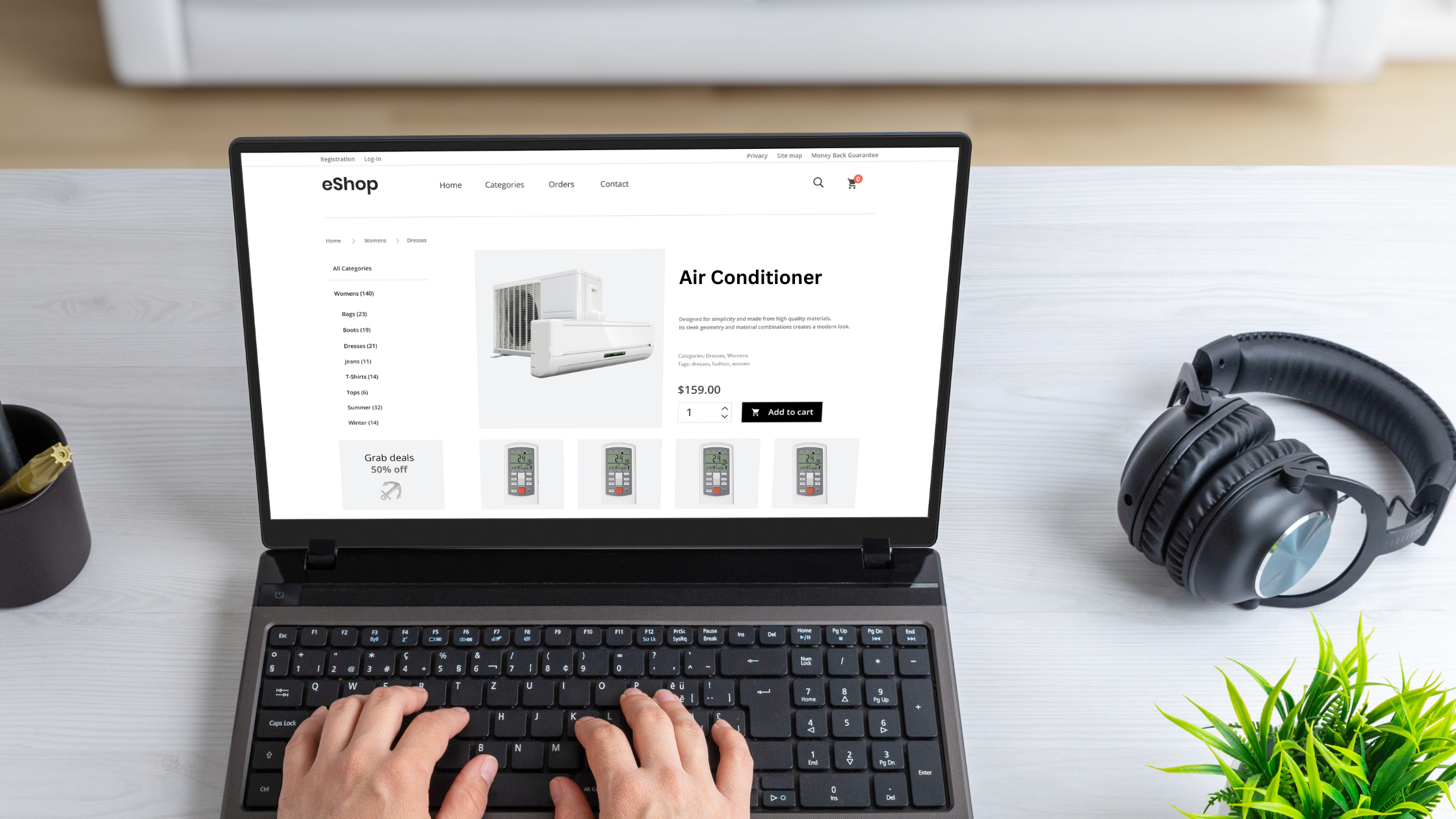
In today's digital age, having an eCommerce site is essential not just for selling products but for establishing your brand in the consumer marketplace. However, merely setting up an eCommerce site is just the beginning.
Many businesses launch their eCommerce platform only to check it off their to-do list. This approach often leads to a stagnant site and poor returns on investment (ROI). That’s where the pivotal role of an eCommerce Manager becomes clear.
Managing an eCommerce site requires constant attention and expertise—qualities that many companies, busy with day-to-day operations, might lack.
Are you maximizing your eCommerce solution? If you're not engaging in these critical tasks daily and weekly, you might be missing out:
Daily Tasks:
- Website Performance Monitoring: Check for and resolve technical glitches like broken links or slow loading times.
- Customer Experience Oversight: Keep a close eye on customer interactions and swiftly address any concerns impacting user satisfaction.
- Order Management Coordination: Ensure the order processing system is efficient and troubleshoot any issues in real-time.
- Analytics Review: Utilize analytics tools to delve into website traffic and user behavior, gaining insights that drive strategic decisions.
- Content Accuracy: Regularly update and verify the accuracy of product descriptions, prices, and images.
Weekly Tasks:
- Sales and Marketing Analysis: Analyze sales data and marketing efforts to spot trends and adjust strategies accordingly.
- SEO and Content Strategy: Collaborate with SEO specialists to enhance product pages and content visibility online.
- Performance Reporting: Compile key metrics to gauge the site’s performance and pinpoint improvement opportunities.
- Promotional Planning: Plan promotions with the marketing and sales teams, ensuring they align with broader business goals.
- Customer Feedback Integration: Use customer feedback to highlight products and services, enhancing overall customer satisfaction.
By diligently performing these tasks, your business can boost customer engagement, streamline operations, and significantly increase the ROI of your eCommerce efforts. Each activity is designed to keep you ahead in the competitive online marketplace.
Don’t let your eCommerce efforts become an afterthought. Partner with Infopine, where our experts are dedicated to elevating your site through comprehensive eCommerce managed services. Focus on your core business, and let us handle the complexities of eCommerce management.
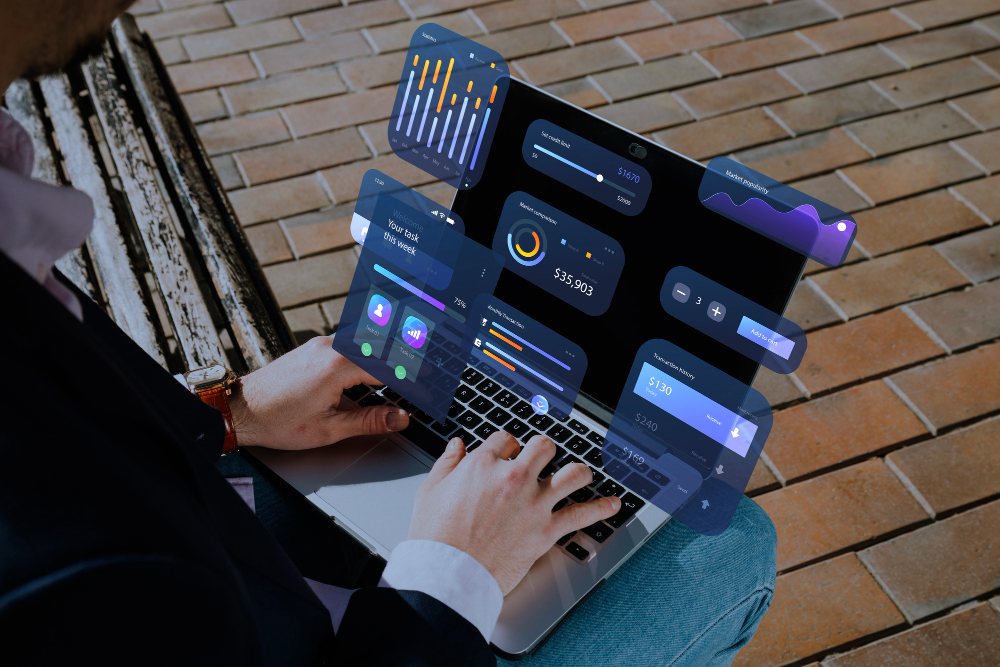
Customer Profile:
Customer is a well-known technical textile manufacturer with a global presence, specializing in producing advanced materials used in automotive, medical, and protective applications.
Problem Statement:
Our customer was using Infor ERP to manage its complex manufacturing operations. However, as the company expanded, several critical issues arose:
- The Infor system required endless customizations to meet the specific requirements of the customer.
- The Infor system lacked the specialized tools needed for the technical textiles industry, leading to operational inefficiencies and manual workarounds.
- Integrating Infor with other software systems, such as those for quality control and production planning, proved difficult. This led to data silos and communication breakdowns.
- The Infor system’s complicated interface resulted in prolonged training periods and frequent user errors, hampering productivity.
- Despite ongoing investments in the Infor system, the company struggled to achieve a consistent return on investment (ROI).
Solution:
With the aim of eliminating their struggles with the Infor system, the customer chose to implement iTexClouds – a textile-focused ERP.
Being a textile ERP, iTexClouds includes all the features and functionalities required by textile manufacturers to manage their business operations. The ERP migration process included the following key steps:
- Assessment and Planning: The team conducted a thorough analysis of the Infor system to identify critical processes and map them to the capabilities of iTexClouds ERP.
- Data Migration: Data was carefully cleaned and prepared before being transferred to iTexClouds ERP, ensuring a seamless transition without disrupting operations.
- Customization and Integration: iTexClouds ERP was customized to meet the specific needs of technical textile manufacturing, including advanced features for quality control, material tracking, and production planning. The system was also integrated with existing tools to create a unified platform.
- Training and Support: Employees received targeted training on the new system, focusing on the unique features of iTexClouds ERP that were relevant to their roles. Continuous support was provided to ensure a smooth transition.
- Go-Live: The system was successfully launched, with careful monitoring to minimize disruptions and ensure a successful transition.
Results:
The ERP migration from Infor to iTexClouds delivered substantial improvements:
- The customer noted an improved operational efficiency of up to 35%, leading to faster turnaround times in production and reduced lead times for customer orders.
- Inventory turnover increased by 40%, enabling better control of stock levels and reducing carrying costs.
- Customer achieved a 20% decrease in operational costs due to streamlined processes and reduced manual interventions.
- Employee satisfaction with the new system rose by 50%, resulting in increased productivity and morale.
Contact Us
So, what are you waiting for? Don't let your competition get ahead of you. Contact us today to discuss your textile ERP needs and let us help you achieve your business goals!
html,body{ margin: 0px; } #crmWebToEntityForm.zcwf_lblLeft { width:100%; padding: 25px; margin: 0 auto; box-sizing: border-box; } #crmWebToEntityForm.zcwf_lblLeft * { box-sizing: border-box; } #crmWebToEntityForm{text-align: left;} #crmWebToEntityForm * { direction: ltr; } .form-row { display: flex; flex-wrap: wrap; } .form-field { flex: 0 0 50%; max-width: 50%; } .zcwf_lblLeft .zcwf_title { word-wrap: break-word; padding: 0px 6px 10px; font-weight: bold; } .zcwf_lblLeft .zcwf_col_fld input[type=text], .zcwf_lblLeft .zcwf_col_fld textarea { width: 100%; border: 1px solid #ccc !important; resize: vertical; border-radius: 2px; float: left; } .zcwf_lblLeft .zcwf_col_lab { width: 30%; word-break: break-word; padding: 0px 6px 0px; margin-right: 10px; margin-top: 5px; float: left; min-height: 1px; } .zcwf_lblLeft .zcwf_col_fld { float: left; width: 100%; padding: 0px 6px 0px; position: relative; margin-top: 5px; } .zcwf_lblLeft .zcwf_privacy{padding: 6px;} .zcwf_lblLeft .wfrm_fld_dpNn{display: none;} .dIB{display: inline-block;} .zcwf_lblLeft .zcwf_col_fld_slt { width: 60%; border: 1px solid #ccc; background: #fff; border-radius: 4px; font-size: 12px; float: left; resize: vertical; padding: 2px 5px; } .zcwf_lblLeft .zcwf_row:after, .zcwf_lblLeft .zcwf_col_fld:after { content: ''; display: table; clear: both; } .zcwf_lblLeft .zcwf_col_help { float: left; margin-left: 7px; font-size: 12px; max-width: 35%; word-break: break-word; } .zcwf_lblLeft .zcwf_help_icon { cursor: pointer; width: 16px; height: 16px; display: inline-block; background: #fff; border: 1px solid #ccc; color: #ccc; text-align: center; font-size: 11px; line-height: 16px; font-weight: bold; border-radius: 50%; } .zcwf_lblLeft .zcwf_row {/*margin: 15px 0px;*/} .zcwf_lblLeft .formsubmit { margin-right: 5px; cursor: pointer; color: #333; font-size: 12px; } .zcwf_lblLeft .zcwf_privacy_txt { width: 90%; color: rgb(0, 0, 0); font-size: 12px; font-family: Arial; display: inline-block; vertical-align: top; color: #333; padding-top: 2px; margin-left: 6px; } .zcwf_lblLeft .zcwf_button { font-size: 17px; color: #ffffff; /*border: 1px solid #ccc;*/ padding: 13px 20px; border-radius: 4px; cursor: pointer; max-width: 120px; overflow: hidden; text-overflow: ellipsis; white-space: nowrap; margin-bottom: 6px; } .zcwf_lblLeft .zcwf_tooltip_over{ position: relative; } .zcwf_lblLeft .zcwf_tooltip_ctn{ position: absolute; background: #dedede; padding: 3px 6px; top: 3px; border-radius: 4px;word-break: break-word; min-width: 100px; max-width: 150px; color: #333; z-index: 100; } .zcwf_lblLeft .zcwf_ckbox{ float: left; } .zcwf_lblLeft .zcwf_file{ width: 55%; box-sizing: border-box; float: left; } .clearB:after{ content:''; display: block; clear: both; } @media all and (max-width: 600px) { .zcwf_lblLeft .zcwf_col_lab, .zcwf_lblLeft .zcwf_col_fld { width: auto; float: none !important; } .zcwf_lblLeft .zcwf_col_help {width: 40%;} } -None- Advertisement Cold Call Employee Referral External Referral Website Partner Public Relations Sales Mail Alias Seminar Partner Seminar-Internal Trade Show Web Download Web Research Chat Tex EventCaptcha validation failed. If you are not a robot then please try again.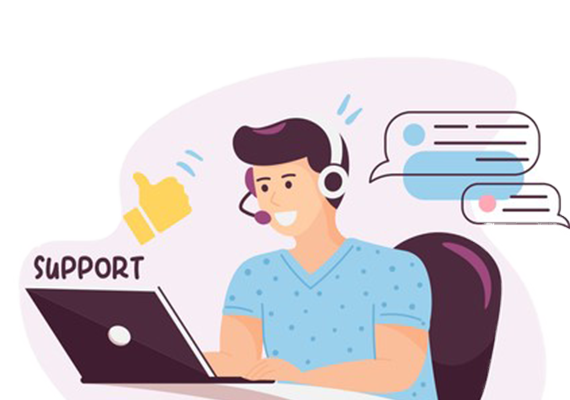
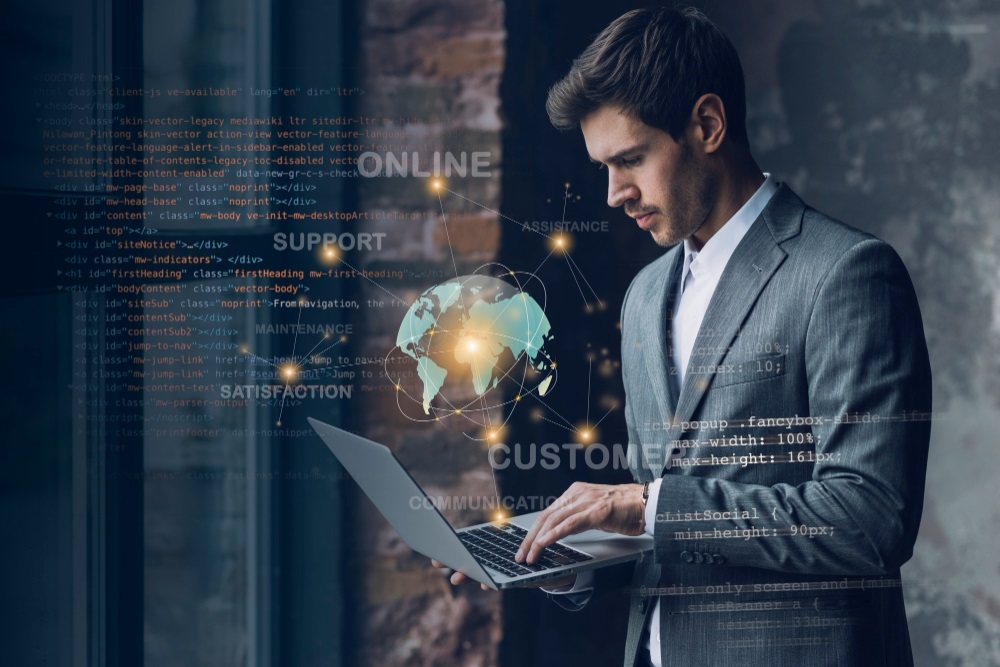
Customer Profile:
Our customer is a textile manufacturer with operations spanning the global market. They specialize in producing high-quality fabrics for various industries. The company has a strong reputation for innovation and sustainability in the textile industry.
Problem Statement:
The customer was using the IBM AS/400 system to manage their day-to-day textile operations. While the system had served them well for years, it was becoming increasingly difficult to keep up with modern business demands. As a result, they were facing several critical challenges like:
- Limited Flexibility: The AS/400 system lacked the flexibility to rapidly adapt to the changing needs of the global textile market, making it difficult to implement new processes or technologies.
- Inefficient Data Management: The system's data management capabilities were outdated, leading to slow processing times and difficulties in accessing real-time information across different departments and locations.
- High Maintenance Costs: Maintaining the AS/400 required specialized knowledge and frequent updates, resulting in high IT costs and a heavy reliance on legacy support teams.
- Scalability Issues: As the company expanded, the AS/400 system struggled to scale, leading to inefficiencies in production planning and inventory management.
- Poor ROI: Despite significant investments in maintaining the system, the company was struggling to achieve a satisfactory return on investment (ROI), hindering their ability to reinvest in growth initiatives.
Solution:
To resolve the issues faced by the textile manufacturer, the decision was made to migrate from the IBM AS/400 system to iTexClouds ERP, a modern, cloud-based software solution tailored for the textile industry.
The ERP migration process was carefully planned and executed in several key phases:
- Assessment and Planning: The first step involved analyzing the existing AS/400 system to understand its structure and determine how best to map its functionalities to iTexClouds ERP.
- Data Migration: The team ensured a seamless transition by cleaning and preparing the data before using automated tools to transfer all relevant historical data to the new cloud environment.
- Integration and Testing: iTexClouds ERP was integrated with the company’s existing tools, followed by rigorous testing to ensure all systems functioned smoothly and data integrity was maintained.
- Training and Support: Employees were trained on the new system, and ongoing support was provided to help them fully adapt to the new processes and maximize the benefits of iTexClouds ERP.
- Go-Live: The new system was successfully launched with continuous monitoring to ensure a smooth transition and minimal disruption to operations.
Results:
The ERP migration from IBM AS/400 to iTexClouds yielded significant positive outcomes for the textile manufacturer:
- Operational efficiency increased by 25%, leading to faster production cycles and streamlined processes.
- IT maintenance costs were reduced by 30%, allowing the company to reallocate resources to growth initiatives.
- Customer achieved a 100% ROI within 2 years of implementation.
- Real-time data access improved decision-making speed by 40%, enabling quicker responses to market changes.
Contact Us
So, what are you waiting for? Don't let your competition get ahead of you. Contact us today to discuss your textile ERP needs and let us help you achieve your business goals!
html,body{ margin: 0px; } #crmWebToEntityForm.zcwf_lblLeft { width:100%; padding: 25px; margin: 0 auto; box-sizing: border-box; } #crmWebToEntityForm.zcwf_lblLeft * { box-sizing: border-box; } #crmWebToEntityForm{text-align: left;} #crmWebToEntityForm * { direction: ltr; } .form-row { display: flex; flex-wrap: wrap; } .form-field { flex: 0 0 50%; max-width: 50%; } .zcwf_lblLeft .zcwf_title { word-wrap: break-word; padding: 0px 6px 10px; font-weight: bold; } .zcwf_lblLeft .zcwf_col_fld input[type=text], .zcwf_lblLeft .zcwf_col_fld textarea { width: 100%; border: 1px solid #ccc !important; resize: vertical; border-radius: 2px; float: left; } .zcwf_lblLeft .zcwf_col_lab { width: 30%; word-break: break-word; padding: 0px 6px 0px; margin-right: 10px; margin-top: 5px; float: left; min-height: 1px; } .zcwf_lblLeft .zcwf_col_fld { float: left; width: 100%; padding: 0px 6px 0px; position: relative; margin-top: 5px; } .zcwf_lblLeft .zcwf_privacy{padding: 6px;} .zcwf_lblLeft .wfrm_fld_dpNn{display: none;} .dIB{display: inline-block;} .zcwf_lblLeft .zcwf_col_fld_slt { width: 60%; border: 1px solid #ccc; background: #fff; border-radius: 4px; font-size: 12px; float: left; resize: vertical; padding: 2px 5px; } .zcwf_lblLeft .zcwf_row:after, .zcwf_lblLeft .zcwf_col_fld:after { content: ''; display: table; clear: both; } .zcwf_lblLeft .zcwf_col_help { float: left; margin-left: 7px; font-size: 12px; max-width: 35%; word-break: break-word; } .zcwf_lblLeft .zcwf_help_icon { cursor: pointer; width: 16px; height: 16px; display: inline-block; background: #fff; border: 1px solid #ccc; color: #ccc; text-align: center; font-size: 11px; line-height: 16px; font-weight: bold; border-radius: 50%; } .zcwf_lblLeft .zcwf_row {/*margin: 15px 0px;*/} .zcwf_lblLeft .formsubmit { margin-right: 5px; cursor: pointer; color: #333; font-size: 12px; } .zcwf_lblLeft .zcwf_privacy_txt { width: 90%; color: rgb(0, 0, 0); font-size: 12px; font-family: Arial; display: inline-block; vertical-align: top; color: #333; padding-top: 2px; margin-left: 6px; } .zcwf_lblLeft .zcwf_button { font-size: 17px; color: #ffffff; /*border: 1px solid #ccc;*/ padding: 13px 20px; border-radius: 4px; cursor: pointer; max-width: 120px; overflow: hidden; text-overflow: ellipsis; white-space: nowrap; margin-bottom: 6px; } .zcwf_lblLeft .zcwf_tooltip_over{ position: relative; } .zcwf_lblLeft .zcwf_tooltip_ctn{ position: absolute; background: #dedede; padding: 3px 6px; top: 3px; border-radius: 4px;word-break: break-word; min-width: 100px; max-width: 150px; color: #333; z-index: 100; } .zcwf_lblLeft .zcwf_ckbox{ float: left; } .zcwf_lblLeft .zcwf_file{ width: 55%; box-sizing: border-box; float: left; } .clearB:after{ content:''; display: block; clear: both; } @media all and (max-width: 600px) { .zcwf_lblLeft .zcwf_col_lab, .zcwf_lblLeft .zcwf_col_fld { width: auto; float: none !important; } .zcwf_lblLeft .zcwf_col_help {width: 40%;} } -None- Advertisement Cold Call Employee Referral External Referral Website Partner Public Relations Sales Mail Alias Seminar Partner Seminar-Internal Trade Show Web Download Web Research Chat Tex EventCaptcha validation failed. If you are not a robot then please try again.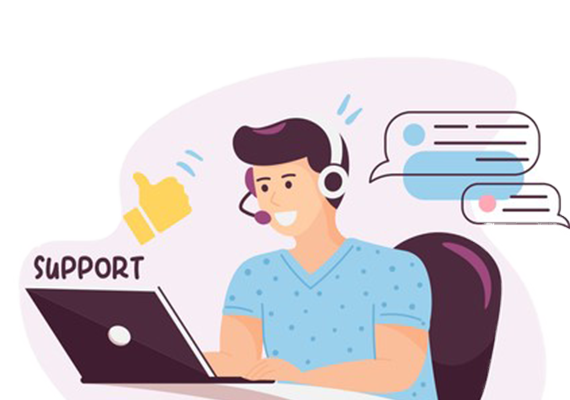
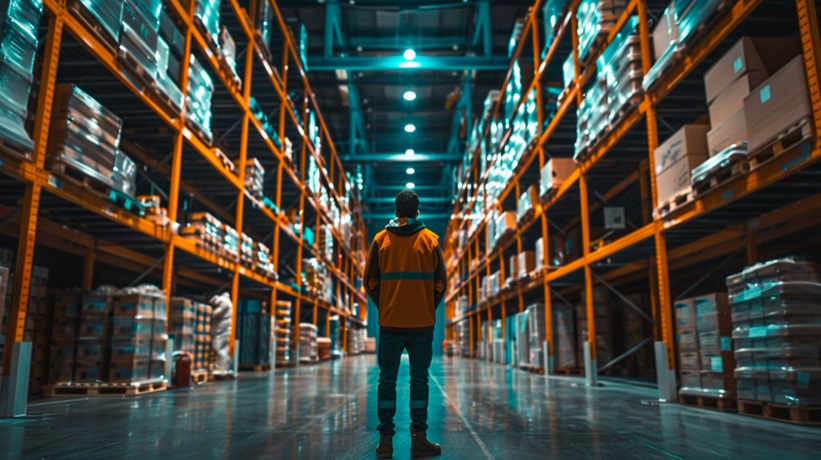
According to a survey conducted by the International Textile Manufacturers Federation (ITMF), 45% of companies reported challenges with apparel and textile warehouse management, leading to either surplus stock or underproduction.
If you ask “what is proper warehouse management” – it is a growing need for textile manufacturers as the industry deals with a lot of raw material storage, regular shipments, order deliveries, etc. Optimizing space allocations and regular tracking of all warehouse tasks is a mandatory need. To check all these boxes off, integrating an ERP software that offers robust warehouse management is the best solution for a textile manufacturer.
In this blog, we are going to look at what a proper warehouse management system is and discuss key features an ERP warehouse management system must have.
What is Proper Warehouse Management?
There are multiple ways to manage warehouse activities in the textile industry, but the question is which is the most efficient way? The answer is simple – implement an ERP software which will allow you to leverage a warehouse management system (WMS) in the textile industry.
An ERP software will help you with effective organization, control, and monitoring of all warehouse activities, such as:
- Efficient space utilization
- Inventory management
- Detailed data analysis
- On-time order fulfilment
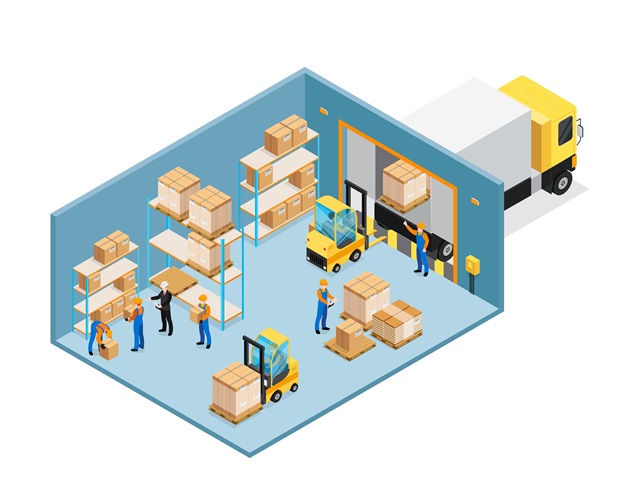
Key Features of Apparel and Textile Warehouse Management System
Now that we know what proper warehouse management is, let’s talk about the specific features an ERP with WMS must have.
An ERP software generally consists of a warehouse management module which is specifically designed to help textile manufacturers optimize space utilization, ensure accurate order fulfilment, and minimize storage costs. To discuss this in a more detailed manner, here are 5 key features of an ERP warehouse management system:
1. Inventory Tracking and Management
Accurate inventory tracking is the backbone of efficient apparel and textile warehouse management. An ERP software provides real-time visibility into inventory operations, such as raw material shipping, stock adjustments, cycle counting of fabrics and keeping track of batches, pallets, rolls, boxes, etc. Manufacturers also get information about precise inventory locations and movements between various warehouses.
Having up-to-date inventory information is crucial to meet customer demands and reduce holding costs.
2. Optimizing Space Utilization
Optimizing space utilization is an essential feature of an efficient warehouse management system (WMS) in textile industry. Apparel and textiles warehouse management system helps in organizing the warehouse layout, ensuring that products are stored in the most effective locations.
A WMS system can analyze data based on product dimensions, demand patterns, and picking frequencies and recommend the best storage strategies. This reduces travel time for picking and packing, minimizes congestion, and enhances overall productivity.
3. Barcode and RFID Integration
Barcode and RFID (Radio Frequency Identification) technologies are one of the main features of apparel and textiles warehouse management system. Integrating these technologies with an ERP warehouse management system enables accurate and efficient tracking of inventory and finished products.
Barcodes and RFID tags provide real-time information on product movements, reducing manual data entry and errors. This integration enhances inventory accuracy, speeds up the receiving and shipping processes, and improves overall warehouse efficiency.
4. Integration with Other ERP Modules
One of the main advantages of an ERP warehouse management module is its ability to easily integrate with multiple modules within the software. Apparel and textiles warehouse management is closely linked with other processes such as procurement, production, and sales. An ERP software ensures that these functions communicate effectively, providing a streamlined flow of operations.
For example, when a sales order is placed, the inventory management module checks inventory levels to ensure the required products are available. If inventory is insufficient, the system can automatically trigger the purchase management module to initiate purchasing or the PPC module to update production schedules. The warehouse management module then manages the physical handling, picking, and shipping of goods. This integration streamlines operations, reduces delays, and enhances customer satisfaction.
5. Real-Time Data and Analytics
Having access to real-time data is a necessity for textile manufacturers to make informed decisions. Apparel and textiles warehouse management system provides real-time analytics and reporting capabilities, enabling textile businesses to monitor key performance indicators (KPIs) and identify trends.
This data-driven approach allows textile companies to respond quickly to market changes, optimize inventory levels, and improve overall efficiency. Real-time insights also help in identifying bottlenecks and areas for improvement, leading to continuous process optimization.
Implementing an apparel and textiles warehouse management system is essential for success in the competitive industry. It ensures efficient space utilization, accurate inventory tracking, and seamless integration with other business processes.
Warehouse management system (WMS) in textile industry minimizes errors, reduces costs, and improves customer satisfaction, ensuring timely and accurate order deliveries. Adopting a specialized software tailored for the textile industry can empower businesses to streamline operations, reduce waste, and achieve long-term sustainability in a fast-paced market.
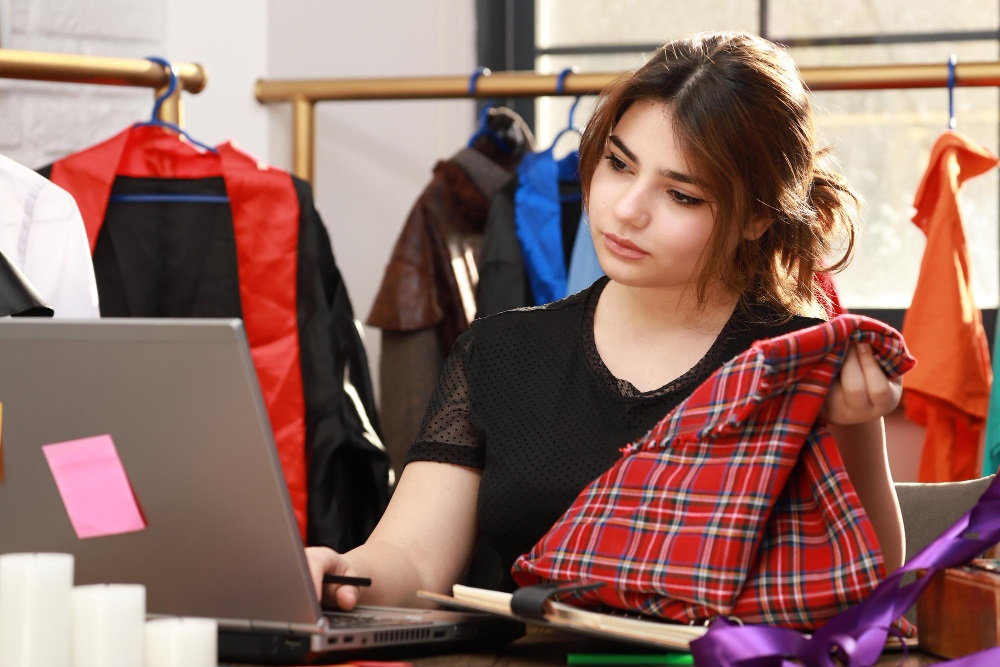
Imagine a growing textile business, bustling with new orders every day, striving to keep up with the increasing demands of its customers. Managing these orders manually becomes a challenging task, prone to errors, delays, and inefficiencies. This is where apparel order management software, integrated within an ERP system becomes essential.
A textile order management software is developed to streamline the entire sales order process. It seamlessly integrates with other departments like inventory, production, finance, etc., and offers real-time data. As a result, textile manufacturers benefit from increased business visibility, reducing errors and enhancing customer experience.
This blog post will discuss the essential role of an order management system for textile integrated within an ERP software and highlights its specific features and benefits.
Role of Apparel Order Management Software
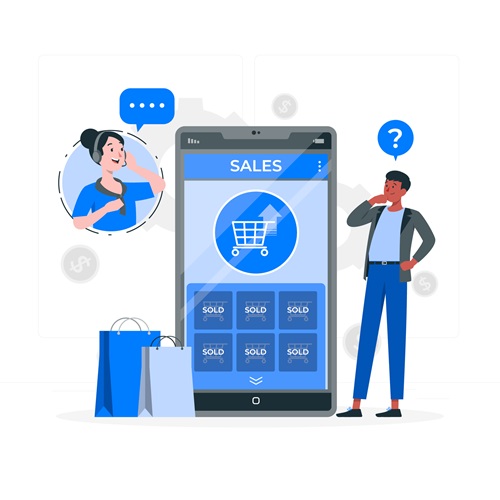
While investing in a standalone fashion order management software can do the work for textile manufacturers, an advanced ERP software with comprehensive modules is always a better choice!
A comprehensive ERP system consists of an order management module that integrates various business processes, providing a unified platform for managing various orders. Since all modules within an ERP software work in sync with each other, it helps textile manufacturers ensure that all departments ranging from sales and inventory to finance work together easily.
Here are some of the important roles an order management system for textile plays:
1. Seamlessly Integrates Departments:
ERP or an apparel order management software connects sales, inventory, finance, and shipping, ensuring information flows seamlessly and processes are synchronized. This integration improves accuracy and efficiency by automatically updating all relevant departments when a sales order is placed.
2. Offers Real-time Data and Visibility:
Textile order management software provides real-time tracking of sales orders from the moment they are placed until they are fulfilled. This real-time visibility into order status, inventory levels, and customer details enables sales teams to proactively manage customer expectations, provide accurate delivery timelines, and promptly address any issues that may arise.
3. Improves Accuracy and Reduces Errors:
ERP software automates critical aspects of sales order management, such as data entry, order processing, and billing. This automation ensures that every step, from capturing customer orders to final invoicing, is executed with precision. The result is fewer human errors in shipments, accurate billing, and a smoother overall process.
4. Enhances Customer Experience:
With apparel order management software centralizing customer information, sales representatives are empowered to offer highly personalized service. They can quickly access relevant data to address customer inquiries, tailor recommendations, and resolve issues on the spot. This personalized approach enhances the overall customer experience, fostering stronger relationships and boosting customer satisfaction and loyalty.
Key Features of Textile Order Management Software
Fashion order management software offers numerous features tailored to the unique needs of the textile industry. These features streamline sales order management, enhance efficiency, and improve overall business performance.
Here are the key features that make ERP or an apparel order management software a factor for optimizing sales orders in the textile industry:
1. Centralized Sales Channels:
The textile industry consists of various sales channels such as direct sales, online platforms, and distributors. ERP textile order management software centralizes all these channels into a single platform.
This centralization provides a holistic view of all sales activities, enabling better coordination and management. It also ensures consistency in pricing, discounts, and promotions across different channels, enhancing customer trust and satisfaction.
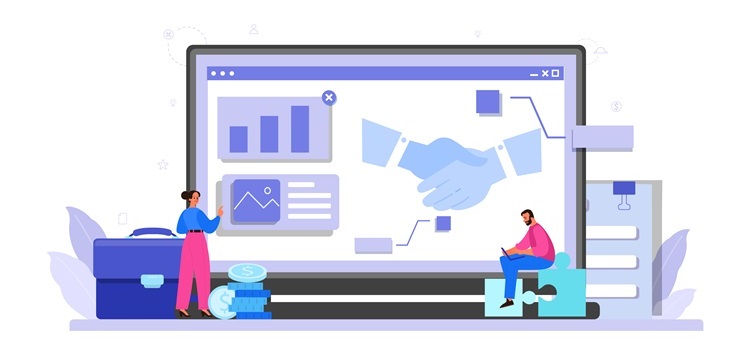
2. Automated Order Processing
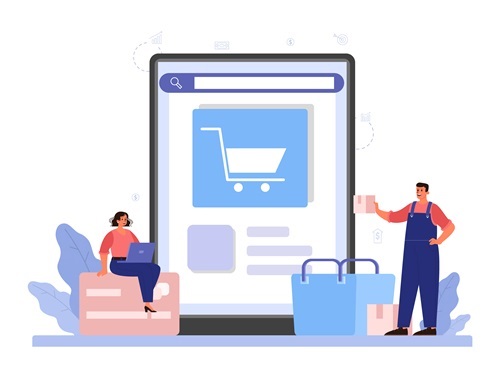
Manual order processing is time-consuming and creates opportunity for a lot of errors. ERP textile order management software automates processes ranging from order entry to invoicing.
This automation accelerates order fulfilment, ensures that all necessary steps are followed accurately, and reduces the likelihood of costly mistakes. Additionally, it allows businesses to handle a higher volume of orders without increasing overhead, enabling them to scale efficiently.
3. Standardized Order Fulfilment Processes
Apparel order management software helps standardize order fulfilment processes by establishing clear workflows and protocols. This standardization ensures that every order ranging from inventory checks to packaging and shipping is handled consistently.
This feature helps reduce variability in final products and maintain an even standard. This helps increase the product quality, reduce room for inconsistencies, increase customer satisfaction, and in turn lead to more sales.
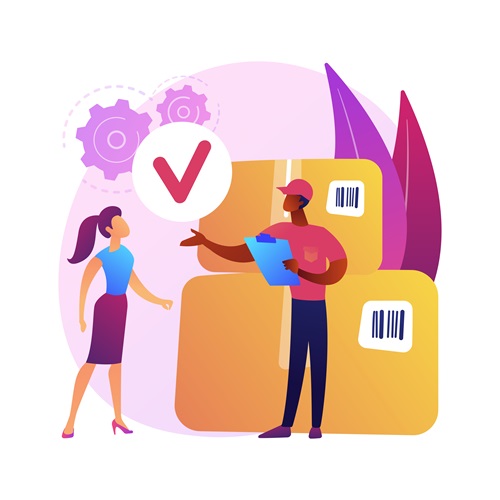
4. Manage Payment Records
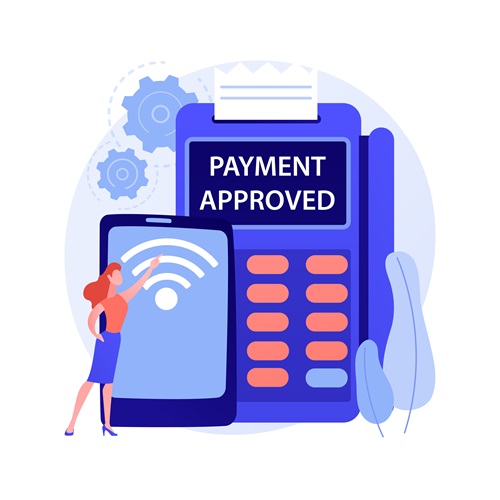
Managing payment records accurately is essential for maintaining accurate cash flow and financial stability. Fashion order management software tracks all payment transactions, ensuring that invoices are accurate, and payments are received on time.
The software maintains clear records of order payments, provides real-time visibility into outstanding payments, and automates reminders for overdue accounts. This feature helps textile businesses to manage finances more effectively and reduces the risk of payment disputes.
Optimizing inventory management through ERP software ensures that the right materials are available when needed, reducing production delays and holding costs. This leads to improved inventory turnover rates, lower waste, and enhanced overall efficiency in the textile production process.
5. Informative Reports and Decision-Making
Apparel order management software generates comprehensive reports that provide insights into sales performance, order trends, and customer behavior. These reports help promote informed decision-making among textile manufacturers with regards to inventory management, marketing strategies, and resource allocation.
In the textile industry, where market trends can change rapidly, having access to accurate and timely information allows companies to adapt quickly. ERP-generated reports help identify areas for improvement and optimize sales strategies.
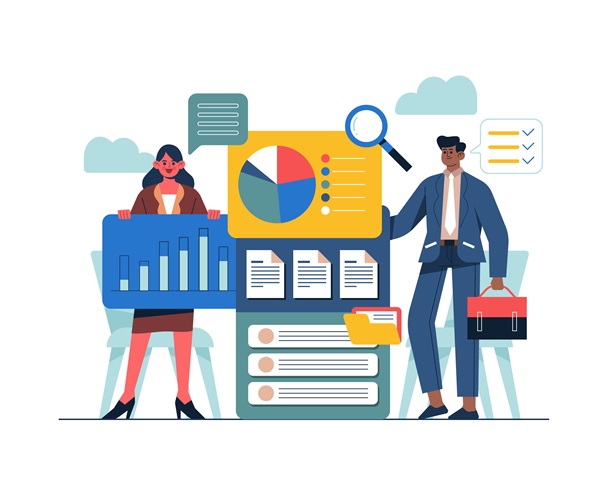
Fashion order management software plays a transformative role in sales order management for the textile industry. It streamlines processes, enhances accuracy, and improves customer satisfaction. By offering centralized sales channels, automating order processing, standardizing fulfilment processes, managing payment records, and providing informative reports, ERP software enables textile companies to stay competitive in a fast-paced market. Implementing apparel order management software is not just an investment in technology; it's an investment in the future success of your business.
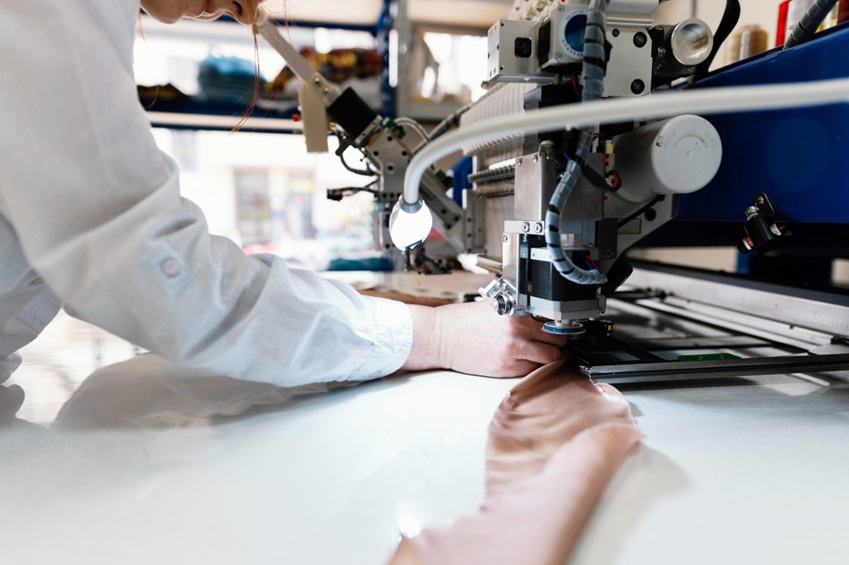
7 Step Guide to Optimize Textile Production Process Through ERP
Schedule MeetingOptimizing the textile production process through ERP can be challenging but highly rewarding. Implementing the right ERP system can streamline operations, enhance productivity, and ensure quality control. However, many businesses struggle to maximize the benefits of their ERP due to improper implementation or underutilization.
ERP software enables you to manage and improve textile production efficiency, including inventory management, production planning, supply chain management, sales and order management, financial management, human resources, and quality management.
So, how can you optimize textile production process using ERP? This guide will walk you through a 7-step process, helping you ensure textile production best practices and harnessing your ERP’s full potential.
7 Steps to Optimize Textile Production Process Through ERP
Textile production processes can be optimized to increase efficiency and lower costs. Implementing an ERP software offers an organized strategy to achieve these objectives. Here, we highlight seven essential steps to optimize textile production process with ERP software for ensuring better resource management, increased productivity, and streamlined operations.
1. Assess Current Processes and Identify Gaps
Before implementing an ERP software to a textile business, identify the areas or gaps that are causing problems in the production process. Analyze each step from raw material procurement to final product delivery. Identify inefficiencies, bottlenecks, and areas where data is not being effectively utilized.
Key Actions:
- Conduct a thorough process audit.
- Gather input from various departments (production, inventory, sales, etc.).
- Identify pain points and areas needing improvement.
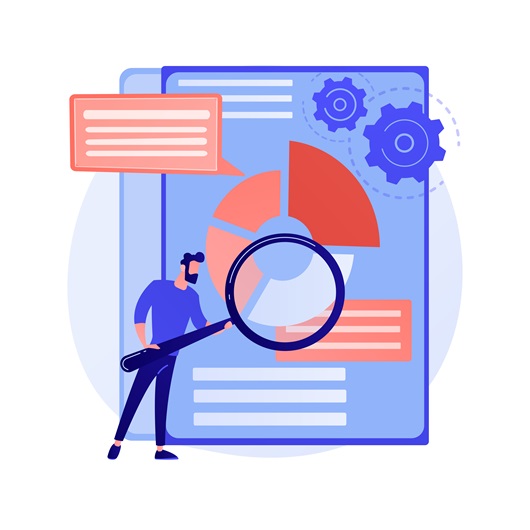
2. Define Clear Objectives
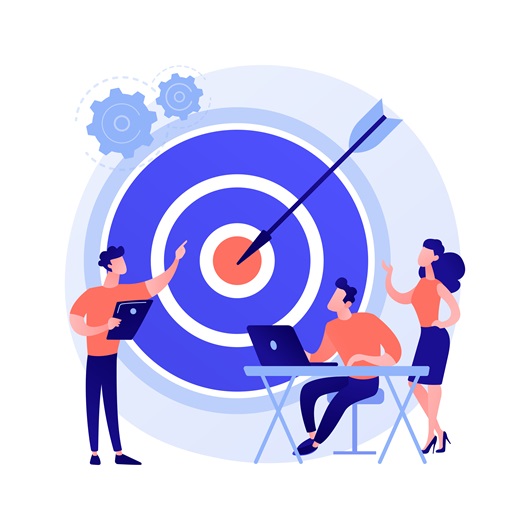
Set clear objectives for what the ERP software is expected to achieve. The goals can be like reducing lead times, minimizing textile waste, improving inventory management, or enhancing communication across departments.
Key Actions:
- Align objectives with overall business goals.
- Prioritize objectives based on impact and feasibility.
- Set measurable targets to track progress.
Having well-defined goals will guide the customization and implementation of the ERP software and clear objectives ensure that the ERP implementation stays focused and delivers tangible benefits.
3. Automate Workflow Processes
Use the ERP software to automate repetitive and time-consuming tasks to improve textile production efficiency. This can include tasks such as order processing, inventory management, production scheduling, and supply chain coordination.
Key Actions:
- Identify manual processes that are time consuming or prone to a lot of errors.
- Check if those processes can be automated.
- Configure your ERP to handle these tasks automatically.
ERP automation of workflow processes reduce manual workload, increase speed, and minimize errors. This leads to faster turnaround times and allows textile manufacturers to focus on more strategic tasks.
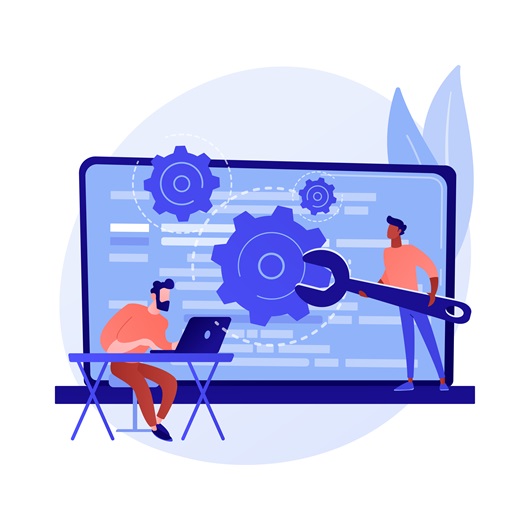
4. Optimize Inventory Management
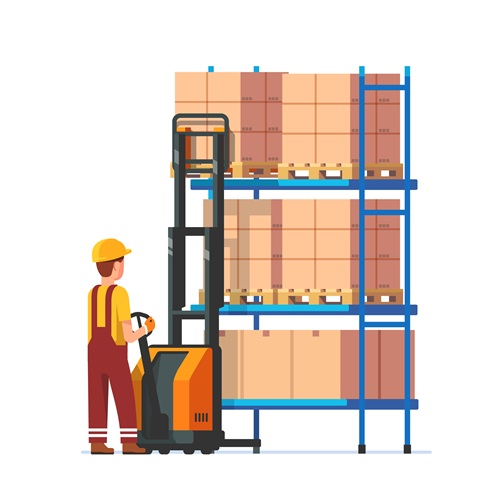
Effective inventory management is crucial to optimize textile production process. Utilizing ERP inventory management helps streamline inventory processes, ensuring materials are available when needed and reducing holding costs.
Key Actions:
- Set up automated inventory tracking through ERP software to track stock levels in real-time.
- Configure automatic alerts for low stock levels to ensure timely reordering of materials.
- Analyze inventory data to identify slow-moving items and adjust purchasing strategies accordingly.
- Forecast demand based on historical data and market trend.
Optimizing inventory management through ERP software ensures that the right materials are available when needed, reducing production delays and holding costs. This leads to improved inventory turnover rates, lower waste, and enhanced overall efficiency in the textile production process.
5. Implement Real-Time Monitoring and Reporting
An ERP allows you to implement real-time monitoring and reporting for gaining essential insights into production performance. You get access to several crucial reports that your ERP generates based on your business data. These reports help you track key performance indicators (KPIs) and make informed decisions based on real-time data.
Key Actions:
- Create personalized dashboards tailored to different roles within your organization.
- Define key performance indicators (KPIs) and track critical metrics
- Configure real-time alerts to notify staff of any anomalies or deviations from expected performance
- Implement graphs, charts, and other visualization tools to make data easily understandable and quickly identify trends.
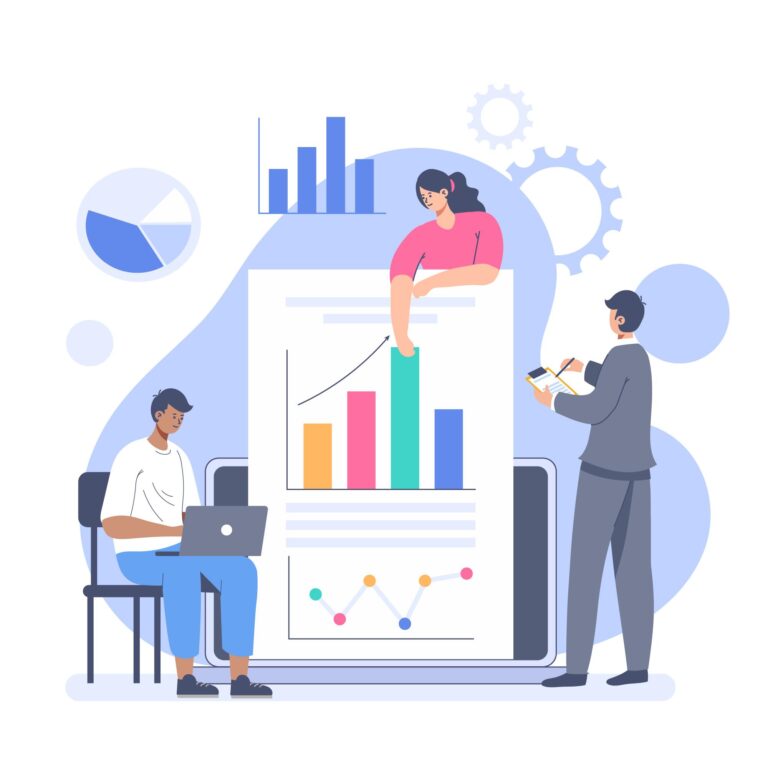
Implementing real-time monitoring and reporting provides immediate access to critical data for proactive management and timely decision-making. Real-time insights will allow your team to respond quickly to issues, reduce downtime and optimize textile production process.
6. Integrate Quality Control Mechanisms
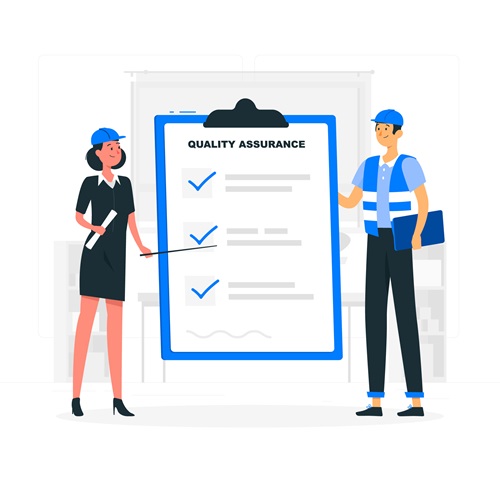
Integrating robust quality control measures within your ERP system is crucial for maintaining high product standards and optimizing the textile production process. By embedding quality control into your ERP, you can ensure that raw materials meet the required standards and maintain consistent product quality throughout every stage of production.
Key Actions:
- Incorporate quality checks at critical points in the production process to catch issues early and prevent defects from progressing.
- Automate quality control alerts to notify relevant personnel of quality issues in real time. This enables immediate corrective actions.
- Ensure that quality standards and inspection criteria are regularly reviewed and updated in the ERP software to ensure compliance with industry regulations and evolving customer expectations.
- Use ERP software to record quality control data and generate reports for continuous improvement and audit readiness.
By integrating quality control mechanisms within your ERP software, you can ensure consistent product quality, reduce defects, and enhance customer satisfaction. This also strengthens your compliance with industry standards and boosts your reputation for reliability and excellence.
7. Foster Collaboration and Communication
Fostering collaboration and communication across departments is vital to optimize the textile production process. The ERP software can significantly improve these aspects by providing a centralized platform for information sharing and workflow management.
Key Actions:
- Implement real-time communication tools within the ERP software, such as instant messaging and notifications.
- Schedule regular meetings and updates through the ERP software to ensure all team members are aligned with project goals and timelines.
- Enable document sharing and collaboration by using the ERP software as a repository for critical documents and data.
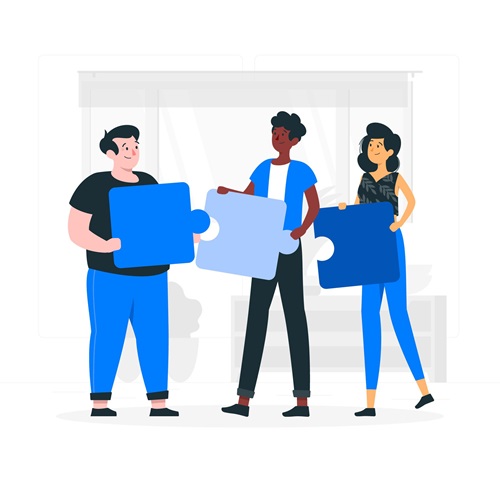
Establishing communication between departments through an ERP software leads to improved teamwork and coordination, resulting in optimized textile production processes. It ensures that all departments are on the same page, reducing misunderstandings and production delays. This ultimately enhances operational efficiency and drives continuous improvement in the textile production process.
Implementing an ERP software is one of the best ways to optimize the textile production process. By following this 7-step guide, textile manufacturers can improve textile production efficiency, streamline workflows, improve inventory management, and enhance quality control. Real-time monitoring, automation, and improved collaboration lead to increased efficiency, reduced costs, and higher product quality. An ERP software ensures textile production best practices are implemented. This helps business owners to ensure smoother operations and a stronger, more responsive business eventually leading to an optimized textile production process.
Contact Us
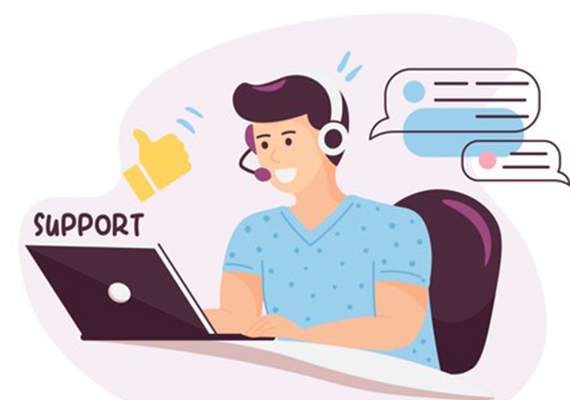