All Resources
Read and get updated on how we progress
- All Resources
- Blog
- Customer Story
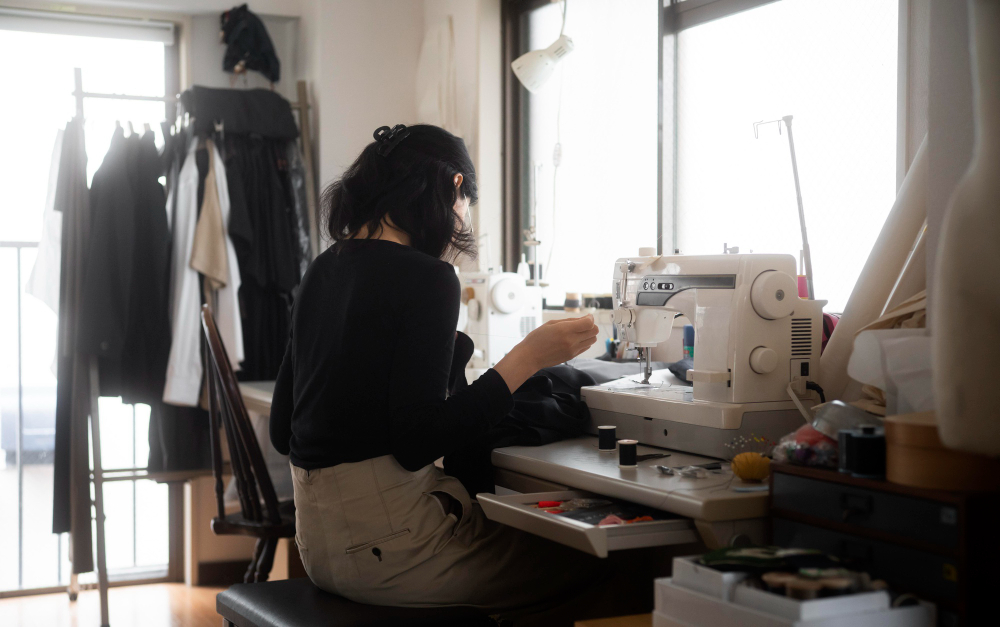
In the textile industry, staying competitive depends on operating with high efficiency, adaptability, and precision. One of the most effective ways to achieve this is through ERP implementation. By integrating ERP software, textile manufacturers can streamline operations, enhance productivity, and manage resources with better accuracy.
In this blog, we’ll explore the top 10 benefits of ERP implementation in your textile business and discuss how it can transform your operations, helping you achieve higher efficiency and profitability.
Top 10 Textile ERP Benefits
Implementing an ERP system tailored specifically for textile operations brings a wide array of advantages, from better production and inventory management to streamlined financial processes.
Below, we dive into the top 10 benefits of ERP implementation for textile businesses and explain how it can reshape your company’s operational landscape to keep up with industry demands.
- Improved Production Control
- Improved Inventory Management
- Better Financial Management
- Streamlined Supply Chain Management
- Stay Compliant with ESG Standards
- Scalability
- Data-Driven Decision Making
- Regulatory Compliance
- Improved Collaboration
- Optimized Warehouse Management
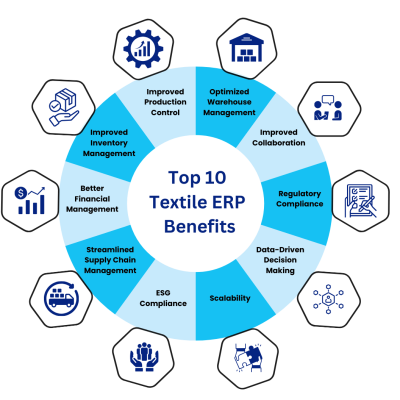
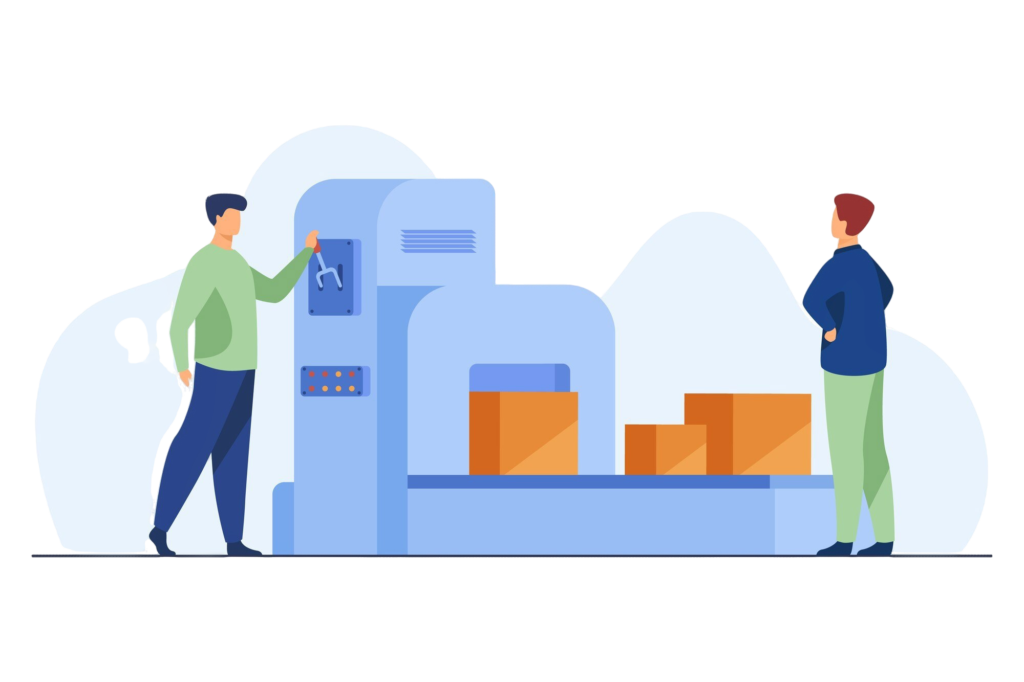
1] Improved Production Control: ERP implementation allows textile manufacturers to optimize the entire production process by providing real-time tracking of production activities. With an ERP system in place, manufacturers can monitor each stage of the manufacturing process, identify bottlenecks, and ensure that each phase operates seamlessly.
This heightened level of control reduces delays, minimizes errors, and ensures that delivery deadlines are consistently met. By enhancing production control, textile businesses can better manage various orders, prevent disruptions, and improve overall operational flow.
2] Improved Inventory Management: ERP textile advantages are especially valuable in inventory management, which is crucial in an industry dealing with a wide variety of raw materials, colors, and product types. An ERP system provides an accurate, real-time view of stock levels, helping businesses avoid overstocking and understocking.
Automated tracking of raw materials, in-process inventory, and finished goods allows companies to reduce waste, cut down on storage costs, and improve overall supply chain management. This enhanced inventory control not only reduces costs but also enables better resource allocation, ensuring that production runs smoothly without interruptions due to stock shortages.
3] Better Financial Management: ERP implementation in a textile business greatly improves financial management by automating accounting, budgeting, and reporting processes. This reduces manual errors, speeds up financial reporting, and provides a clearer picture of the company’s financial health.
With real-time visibility into cash flow and expenses, ERP software empowers decision-makers to manage cash flow more effectively and generate accurate financial statements. These insights are crucial for strategic planning and help companies make informed decisions that drive growth and profitability.
4] Streamlined Supply Chain Management: One of the core ERP textile advantages is its ability to streamline supply chain management. ERP software connects each element of the supply chain, from raw material procurement to product delivery.
This integration facilitates better coordination between suppliers, manufacturers, and distributors, enabling textile businesses to reduce lead times, control costs, and expedite product deliveries to market. By improving supply chain transparency and efficiency, ERP implementation allows textile businesses to respond quickly to demand fluctuations and maintain strong relationships with suppliers and customers.
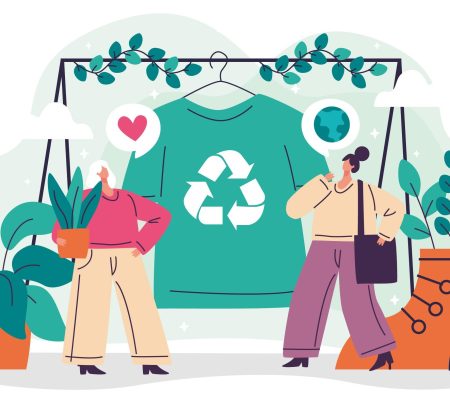
5] Stay Compliant with ESG Standards: Environmental, Social, and Governance (ESG) standards are becoming more important in the textile industry. With growing consumer demand for ethical and sustainable products, companies must demonstrate that they meet these standards.
An ERP software helps textile businesses stay compliant by tracking materials, ensuring sustainable sourcing, and generating reports that show compliance with various ESG regulations. This boosts the company's reputation and opens doors to new markets focused on sustainability.
6] Scalability: As textile businesses expand, their operational needs become more complex. One of the standout ERP textile advantages is scalability, which allows for seamless adjustments and additions as your business grows.
Whether increasing production capacity, entering new markets, or diversifying product lines, ERP implementation provides a flexible framework that can accommodate your evolving needs. New modules and features can be added without disrupting existing processes, ensuring smooth operations regardless of growth or market changes.
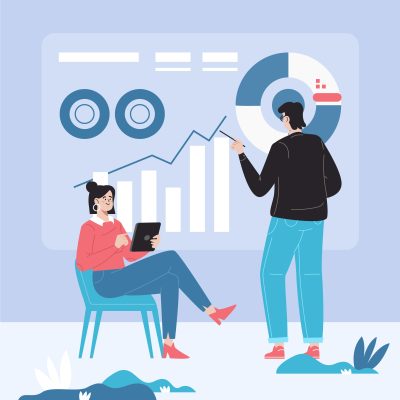
7] Data-Driven Decision Making: An ERP system provides real-time data across departments, enabling data-driven decision making that’s faster and more accurate. By accessing comprehensive reports and dashboards highlighting key performance metrics, decision-makers can identify trends, optimize production schedules, and make adjustments to boost profitability.
Instead of relying on guesswork, textile companies can make strategic choices based on accurate data, empowering them to respond to challenges proactively and stay competitive.
8] Regulatory Compliance: In the textile industry, adhering to regulatory standards is essential, covering areas like health and safety, labor laws, and environmental requirements. ERP implementation helps businesses stay compliant by automating compliance tracking and generating detailed reports for regulatory bodies. This functionality reduces the risk of penalties, audits, and reputational damage, ensuring that your business remains within the legal framework while focusing on its growth and development.
9] Improved Collaboration: One of the challenges in textile businesses is ensuring collaboration across different departments, such as production, sales, and customer service. ERP software fosters better communication and teamwork by providing a centralized platform where all departments can access the same information in real-time. This connectivity improves collaboration, accelerates problem-solving, and ensures that everyone is aligned on goals and objectives, ultimately creating a cohesive and responsive business environment.
10] Optimized Warehouse Management: Managing a textile warehouse involves handling a diverse range of products and materials. ERP implementation optimizes warehouse management by automating tasks like inventory tracking, picking, and shipping, significantly reducing human error and boosting efficiency. This optimization leads to faster order fulfillment, reduced storage costs, and higher customer satisfaction. By streamlining warehouse operations, ERP software ensures that your warehouse is well-organized and capable of supporting timely deliveries and seamless operations.
In textile industry, efficiency and adaptability are key to staying competitive. ERP implementation provides numerous benefits to textile businesses, from enhanced production control and improved financial management to compliance with ESG standards. By centralizing operations, enabling data-driven decision making, and fostering collaboration, ERP systems help textile companies reduce costs, boost customer satisfaction, and achieve sustainable growth. Whether you’re a small textile manufacturer or a large enterprise, ERP implementation is a valuable investment that will pay dividends in improved processes, scalability, and resilience in a dynamic industry.
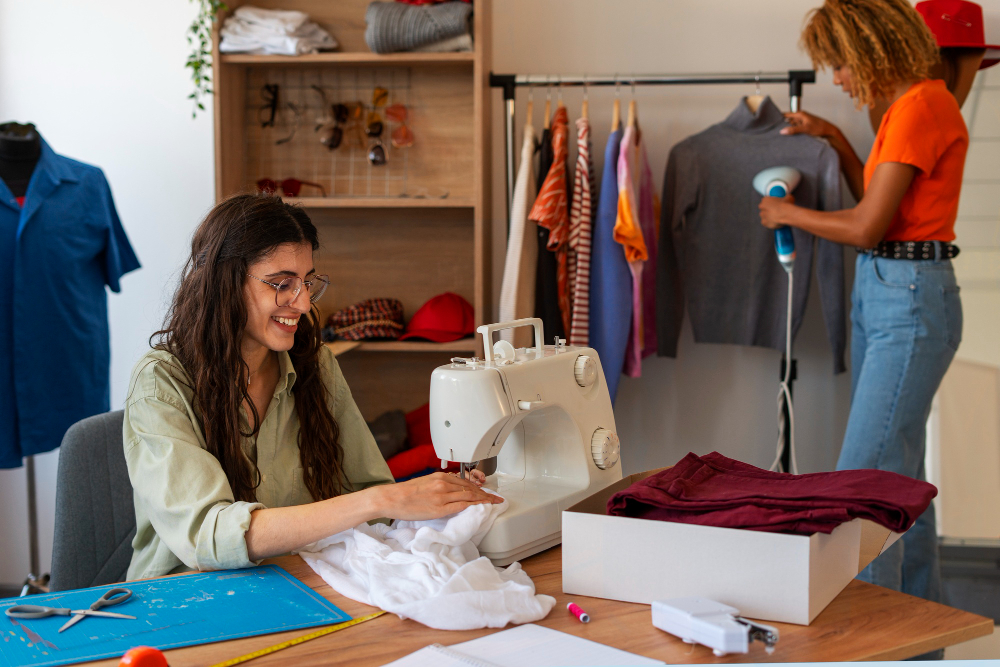
Inventory management in the apparel industry is a critical process that directly impacts profitability, customer satisfaction, and business efficiency. Managing inventory effectively means balancing supply and demand to ensure the right items are in stock, avoiding both stockouts and excess inventory. This is particularly challenging in the apparel sector, where changing consumer preferences and seasonal variations demand a responsive and precise approach.
Leveraging ERP (Enterprise Resource Planning) systems, textile companies can gain visibility across the supply chain, automate key tasks, and make data-driven decisions that enhance inventory control. From real-time tracking to demand forecasting, ERP solutions offer the apparel industry a comprehensive toolkit for optimizing inventory management practices.
Key Features of ERP Inventory Management in Apparel Industry
Effective inventory management in the apparel industry is essential for balancing supply and demand while keeping operational costs in check. ERP systems provide a suite of advanced features that streamline inventory control, enhance accuracy, and support strategic decision-making.
Below are the key features of ERP inventory management in apparel industry, which enable textile businesses to stay agile and responsive in a competitive landscape.
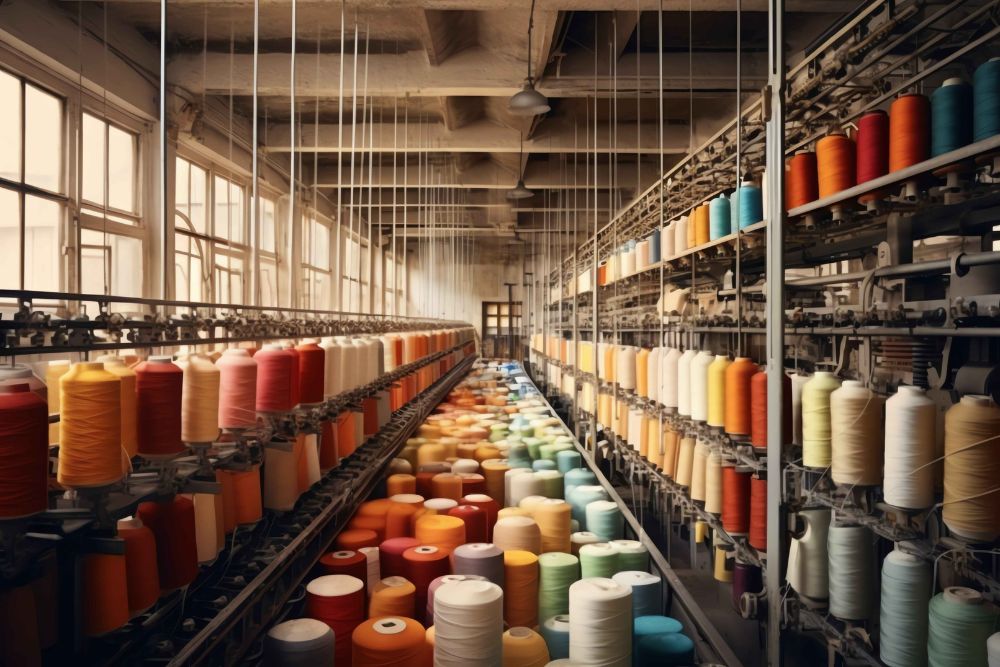
1] AI Integration: AI is transforming inventory management in the textile and apparel industry by introducing predictive analytics and process automation. Within ERP inventory modules, AI integration allows businesses to forecast demand with greater accuracy by analyzing historical sales data, market trends, and external factors, such as weather conditions and economic shifts. This predictive capability helps textile manufacturers maintain optimal stock levels, reducing the likelihood of stockouts and overproduction.
AI-driven automation also manages routine inventory tasks, such as reordering supplies automatically when stock falls below a set threshold, ensuring timely replenishment without manual intervention.
2] Versatile Product Management: The textile and apparel industry deals with a wide variety of products, including different sizes, colors, and styles. ERP software provides versatile product management capabilities, allowing businesses to categorize and manage their inventory based on various attributes.
This functionality is particularly valuable in fashion retail, where products often have multiple variations. By organizing inventory in a structured way, businesses can easily track stock levels for each variation, manage reorders efficiently, and ensure customers have access to the full product range, enhancing overall customer satisfaction.
3] Flexible Inventory Control: Flexible inventory control is a critical feature of ERP systems that allows textile and apparel companies to adapt to changing business needs. With flexible inventory control, businesses can implement various inventory management strategies, such as Just-In-Time (JIT) inventory, bulk purchasing, or consignment stock, depending on their specific requirements.
This flexibility ensures that textile manufacturers can respond to fluctuations in demand, optimize their inventory levels, and minimize carrying costs. Additionally, ERP systems offer real-time inventory tracking, enabling businesses to monitor stock levels across multiple locations and make informed decisions about production and distribution.
4] Accounting and Valuation: Accurate accounting and valuation of inventory are essential for financial reporting and decision-making. ERP systems provide robust accounting and valuation features that help textile and apparel companies maintain precise records of their inventory assets.
These systems automatically calculate the cost of goods sold (COGS), inventory turnover ratios, and other key financial metrics, ensuring compliance with accounting standards. Moreover, ERP systems offer various methods of inventory valuation, such as LIFO (Last-In, First-Out), and weighted average, allowing businesses to choose the most suitable method for their operations.
5] User-Defined Stock Management: User-defined stock management is a feature that allows businesses to customize their inventory management processes according to their unique requirements. ERP systems offer the flexibility to define stock categories, set reorder points, and establish inventory rules based on business priorities.
For example, a company might prioritize certain high-demand products by setting higher reorder levels, while keeping lower levels for slow-moving items. This level of customization ensures that inventory management is aligned with the company’s overall business strategy, reducing the risk of stockouts and excess inventory.
Effective inventory management in apparel industry is crucial for the success of textile businesses. With the rapid advancement of technology, traditional inventory management practices are being replaced by sophisticated ERP systems that offer real-time visibility, automation, and predictive analytics.
By leveraging features such as AI integration, versatile product management, flexible inventory control, accounting and valuation, and user-defined stock management, companies can optimize their inventory processes, reduce costs, and improve overall efficiency.
As the textile and apparel industry continues to evolve, the adoption of advanced inventory management solutions will be key to staying competitive in an increasingly demanding market.
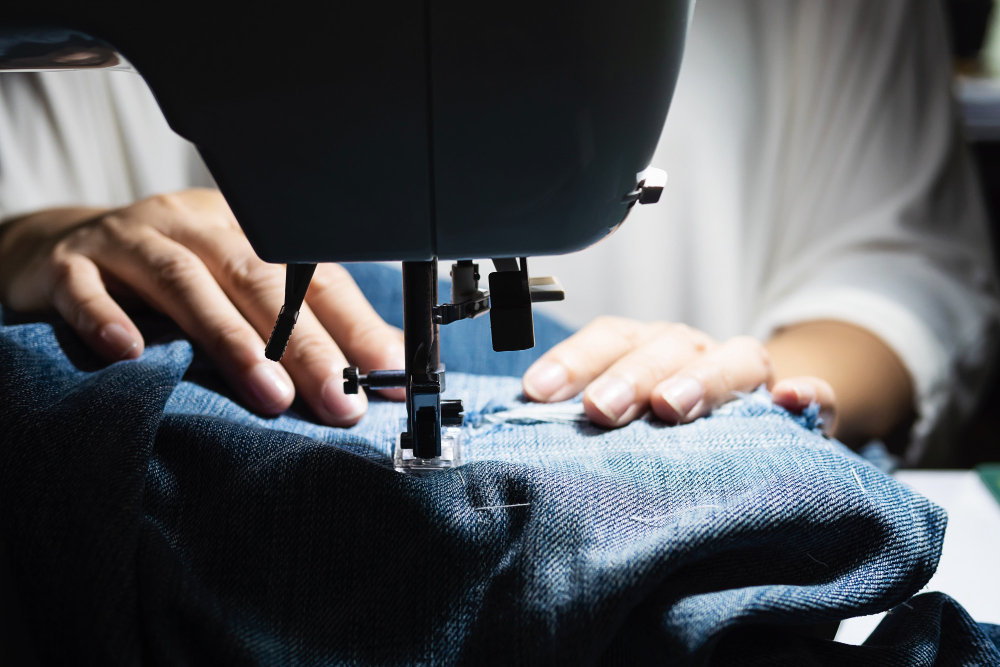
The textile industry is extremely large and consists of many businesses running their operations using outdated or traditional methods. In the current fast paced era, the competition is higher than ever and the demands of textile products are growing day by day.
In order to compete in this market, textile businesses need an edge that will boost their overall production and efficiency. This edge can come in the form of textile manufacturing ERP software, which streamlines operations, reduces errors, and enhances productivity.
Let’s first explore the types of manufacturing software available and establish why ERP software is the optimal choice for the textile industry.
Types of Textile Manufacturing Software
Every textile business operates uniquely, with specific challenges and requirements that set it apart. The different types of manufacturing software available today come with distinct features and functionalities tailored to address these diverse business needs.
For instance, some businesses may prioritize real-time production tracking, while others may need more robust inventory management or detailed supply chain oversight.
By understanding the different types of textile manufacturing software, manufacturers can choose the one most suitable for their operations. This knowledge allows them to leverage the right tools to enhance efficiency, streamline workflows, and ultimately, stay competitive in a fast-evolving industry.
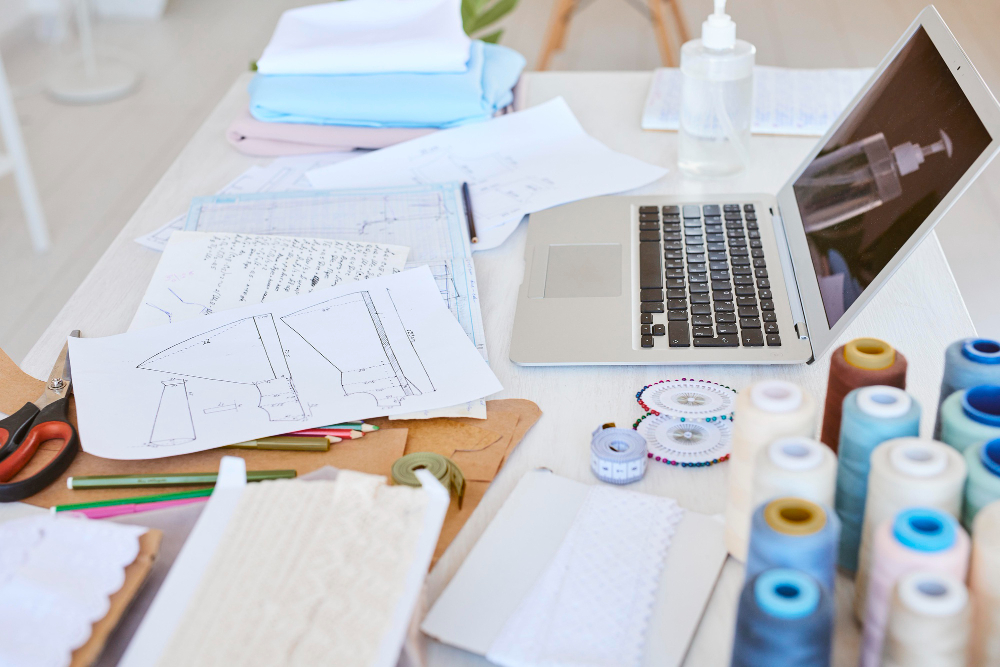
1] Enterprise Resource Planning (ERP) Software
ERP software is one of the most comprehensive solutions available, as it integrates all business processes into a single system. This comprehensive nature makes it especially valuable for textile companies that need to streamline complex workflows and manage multiple departments seamlessly.
- Definition: ERP software integrates various business processes into a single system, improving coordination and operational efficiency across departments.
- Main Feature: Provides real-time insights and data accuracy, allowing for better decision-making and operational efficiency.
- Industry Suitability: For textile businesses, ERP software is invaluable because it consolidates data across production, inventory, supply chain, and finance. This integration is crucial for managing the high volume of orders, varied product lines, and detailed tracking that are common in the textile industry.
2] Manufacturing Execution Systems (MES)
MES software is popular for its focus on production floor operations. It’s a great solution for textile manufacturers needing precise control over production processes, as it provides visibility into each stage of manufacturing.
- Definition: MES software monitors and controls manufacturing processes in real time, providing visibility and management of production operations.
- Main Feature: Improves operational efficiency and quality control by monitoring production performance and addressing problems on the shop floor.
- Industry Suitability: In the textile industry, MES software helps manufacturers monitor quality, track production stages, and respond quickly to process issues. This is particularly important for maintaining fabric quality and ensuring that production targets are met efficiently.
3] Supply Chain Management (SCM) Software
SCM software is designed to optimize logistics and the flow of goods, which is critical for textile companies dealing with vast, international supply chains and multiple raw material sources.
- Definition: SCM software coordinates inventories and logistics while managing the movement of goods and materials along the supply chain.
- Main Feature: Reduces lead times and expenses while increasing overall efficiency and responsiveness through supply chain process optimization.
- Industry Suitability: Textile manufacturers benefit greatly from SCM software as it enables better raw material sourcing, inventory management, and logistics coordination—key factors in meeting customer demands quickly and efficiently.
4] Production Planning Software
Production planning software, also known as a production tracking software is highly effective for scheduling and managing production activities. Textile businesses with complex production timelines rely on this software to streamline their workflows.
- Definition: Production planning software helps in scheduling and organizing production tasks, keeping operations efficient and structured.
- Main Feature: Optimizes schedules, resources, and workflows, minimizing bottlenecks and ensuring timely completion of production tasks.
- Industry Suitability: In the textile industry, where demand can fluctuate and custom orders are common, production planning software helps manage timelines and resources efficiently, ensuring that products are completed on time and to specification.
5] Inventory Management Software
Inventory management software is crucial for textile businesses that handle large volumes of raw materials and finished goods. It helps track stock levels, reduces waste, and prevents overstock and stockouts.
- Definition: Inventory management software tracks and manages inventory levels, orders, and stock movements to optimize inventory control.
- Main Feature: Provides real-time stock data, reducing overstock and stockouts, improving order fulfillment, and lowering costs.
- Industry Suitability: Textile companies, which often carry extensive inventories of fabrics, dyes, and materials, benefit from inventory management software’s ability to monitor stock precisely, minimize wastage, and ensure efficient stock handling.
Why the ERP software is the Best Option for the Textile Industry?
A textile manufacturing ERP software is uniquely suited to meet the demands of the textile industry by offering a comprehensive set of tools to manage and integrate all aspects of production, inventory, and supply chain management.
Let’s take a look at the prominent features of an ERP software that makes it the best software for textile manufacturers.
1] Production Planning and Control
A textile manufacturing ERP software solution includes a production planning module that enables advanced scheduling and monitoring of textile production activities, ensuring that everything runs according to plan.
The module helps textile manufacturers to optimize resource allocation, minimize downtime, and improve overall production efficiency. By integrating quality control measures, the manufacturers can ensure that products meet industry standards and customer expectations.
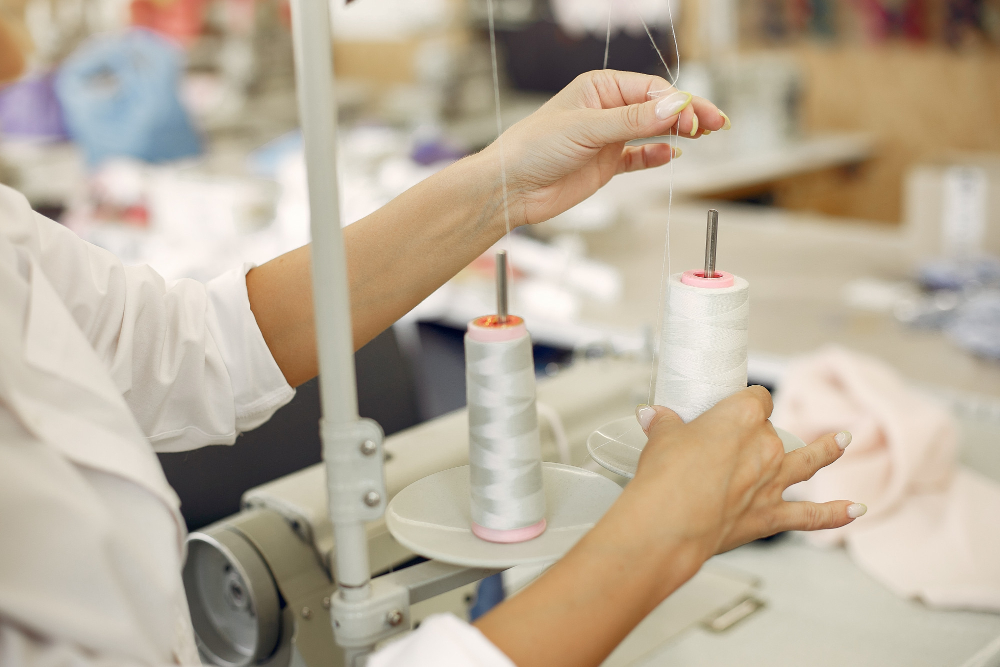
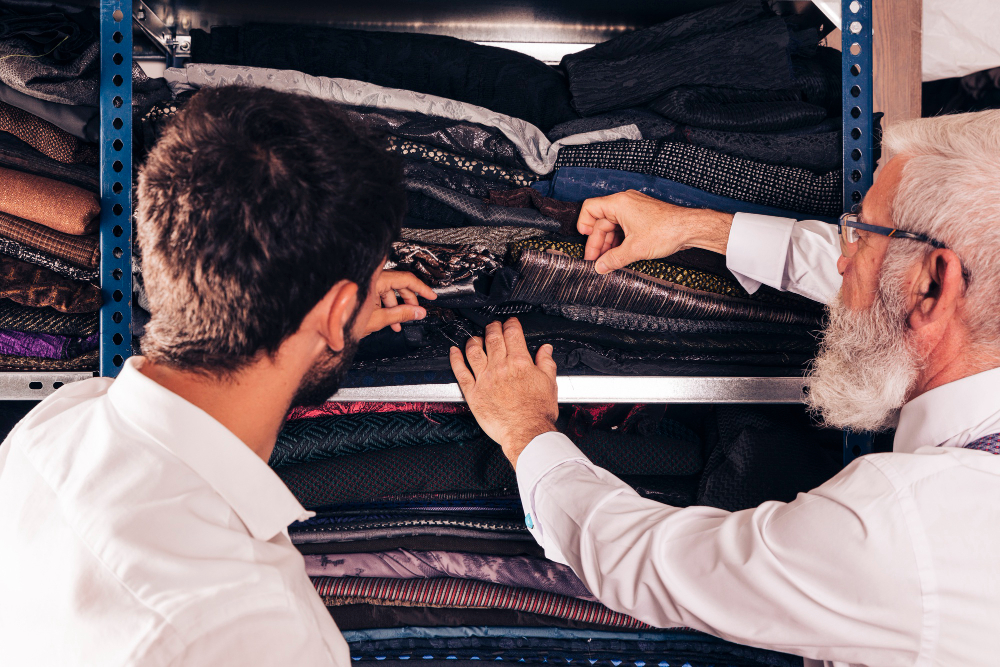
2] Inventory and Warehouse Management
ERP software for textile industry comes equipped with an inventory and a warehouse management module which allows real-time tracking of inventory levels and optimize warehouse space allocation. This helps to manage stock more efficiently and reduce waste.
By preventing both overstocking and stockouts, textile manufacturing ERP software enhances cash flow and reduces inventory holding costs, supporting better warehouse organization and space utilization.
3] Order Management
ERP software streamlines the entire order-to-delivery process, ensuring accurate and timely order fulfillment. It consolidates order information across departments, allowing teams to access up-to-date details on each order, from processing to shipment. This centralized view reduces communication gaps, prevents bottlenecks, and helps resolve issues quickly.
By automating many steps in the order management workflow, textile manufacturing ERP software also reduces the likelihood of manual errors, helping textile manufacturers provide consistent, on-time delivery.
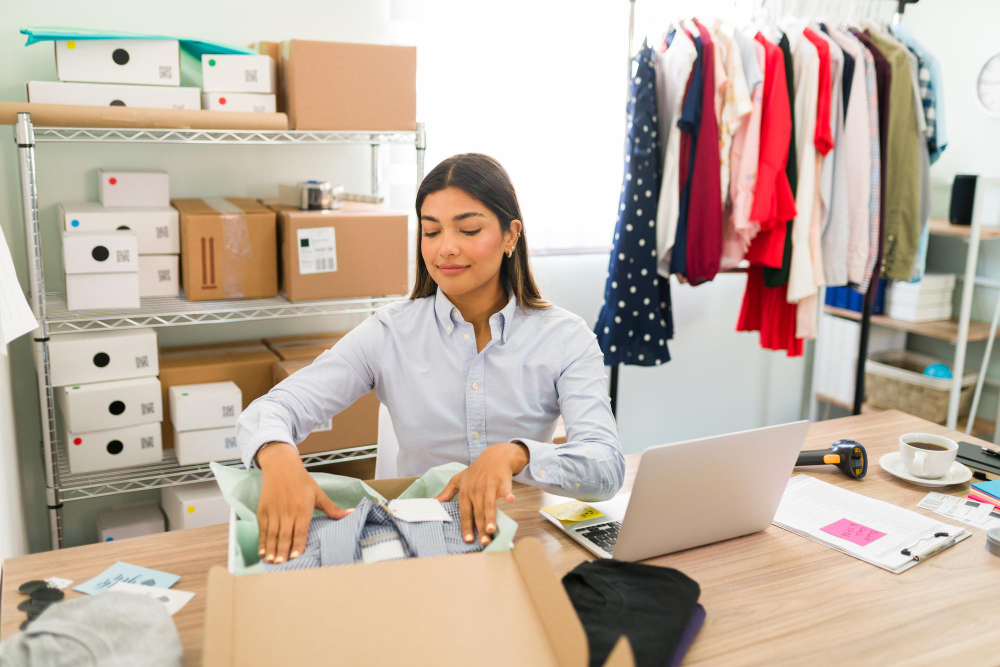
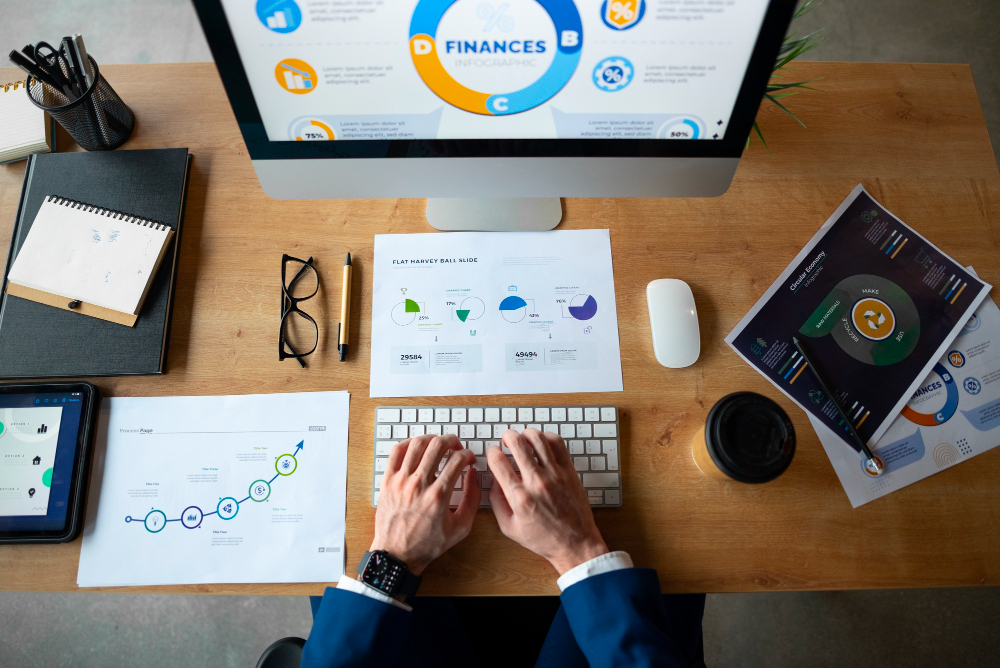
4] Financial Management
ERP software integrates financial data across departments, providing a holistic view of the company’s financial health. With real-time data consolidation, textile companies gain insights into spending patterns, revenue, and profitability, which supports better financial planning and control.
The system also simplifies financial reporting, enabling accurate and timely analysis that helps decision-makers assess performance. Additionally, ERP software aids in maintaining compliance with industry regulations and standards, reducing the risk of financial penalties and ensuring that financial practices align with both industry and regulatory expectations.
5] Supply Chain Management
ERP software facilitates better coordination between suppliers, manufacturers, and distributors, improving the overall supply chain efficiency. By consolidating historical data, textile manufacturing ERP software help manufacturers forecast demand more accurately, allowing them to plan inventory and production schedules based on real market trends.
For textile manufacturers, an optimized supply chain means smoother production cycles, improved response times to changing demands, and ultimately, greater customer satisfaction through timely deliveries.
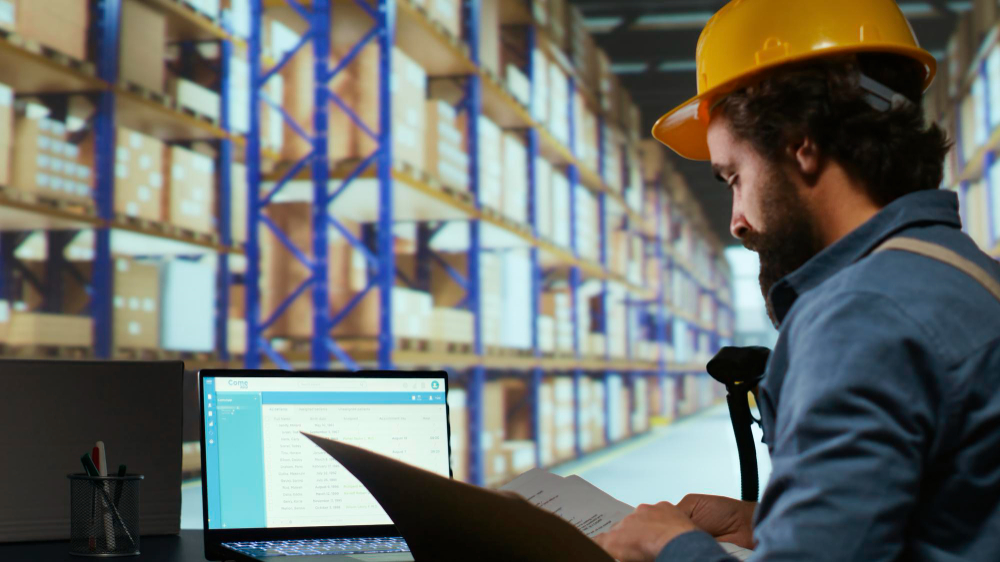
In a competitive industry like textiles, where production efficiency and quality control are paramount, investing in textile manufacturing ERP software can be a game-changer. It integrates multiple processes, enhances production planning, and provides tools for effective production tracking.
As textile businesses look to modernize and improve their production capabilities, an ERP software solution stands out as the best option to support growth, streamline operations, and deliver high-quality products on time. Embracing this technology can give textile businesses the edge they need to meet rising demand, stay competitive, and achieve sustainable success.
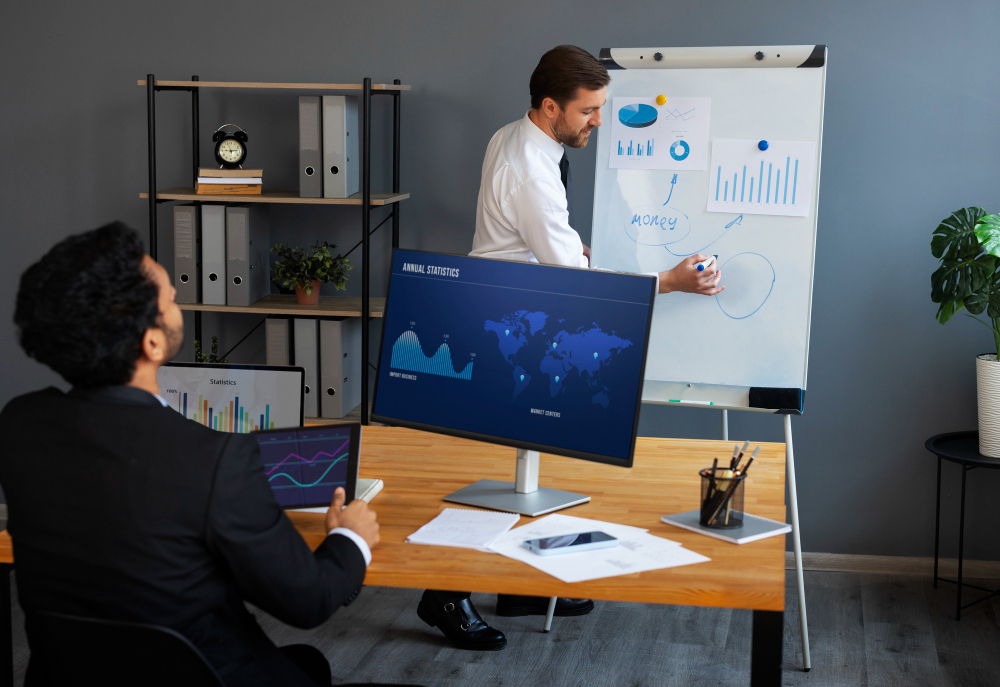
The textile industry is one of the oldest and most essential industries in the global economy. Over the years, it has evolved from manual labor to automated processes, and now, technology plays a crucial role in its operations.
One of the most significant technological advancements have been the adoption of ERP (Enterprise Resource Planning) systems. As per reports, the global ERP market is fast growing and is expected to cross USD 96 billion by 2032!
These systems help textile companies manage everything from production to supply chain management. As we look ahead, understanding the future of ERP in the textile industry becomes vital for businesses aiming to stay competitive.
Existing ERP Capabilities in the Textile Industry
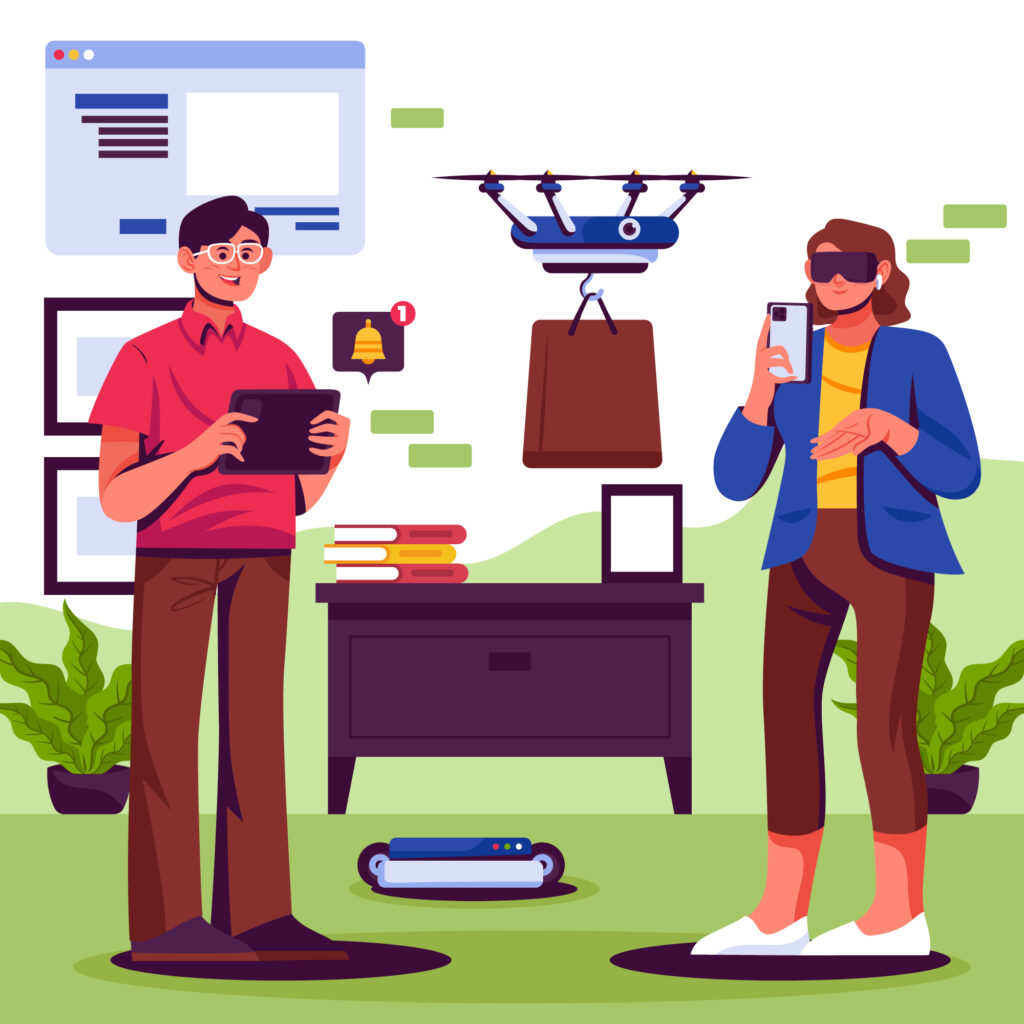
The existing ERP systems available on the market are capable of offering integrated solutions that streamline processes, reduce costs, and improve efficiency.
Interestingly, the manufacturing industry, including textiles, hold the maximum share of the ERP software market – as high as 47%! This explains why today several textile companies rely on these systems to manage their operations effectively.
But what are the ERP capabilities that are not only simplifying operational challenges for textile manufacturers but also shaping the future of ERP? Let’s take a look at them!
1] Cloud-Based Solutions
- These systems allow companies to access their data and manage operations from anywhere in the world.
- The flexibility offered by cloud-based ERP is particularly beneficial for textile companies with multiple locations or global supply chains.
- With real-time updates and seamless communication, cloud-based solutions ensure that all departments are aligned and functioning smoothly.
2] Advanced Data-Driven Analytics
- Modern ERP systems offer advanced data-driven analytics that help companies make informed decisions.
- These analytics tools can analyze large volumes of data to identify trends, predict demand, and optimize inventory management.
- By leveraging data, textile companies can reduce waste, improve product quality, and meet customer demands more effectively.
3] Mobile ERP Solutions
- Mobile ERP solutions allow employees to manage tasks, access information, and make decisions on the go.
- This is particularly useful for managers who need to oversee operations remotely or sales teams who require real-time data while meeting with clients.
- Mobile ERP ensures that all critical information is at your fingertips, no matter where you are.
4] API Integration
- The ability to integrate ERP systems with other software applications is essential for textile companies.
- API (Application Programming Interface) integration allows ERP systems to communicate with other tools such as CRM (Customer Relationship Management) software, e-commerce platforms, and more.
- This integration creates a seamless flow of information across different systems, improving efficiency and reducing the chances of errors.
ERP Future Trends for the Textile Industry
As technology continues to advance, the textile industry must keep pace with the latest textile ERP innovations. These trends will shape the future of ERP systems and offer new opportunities for textile companies to enhance their operations.
- AI Integration
As of now, almost 65% of businesses believe Artificial Intelligence (AI) is critical to ERP systems in the textile industry. That’s not all! 16% participants of a recent survey said that they consider embedded AI a ‘must-have’ in their ERP systems.
AI can automate routine tasks, provide predictive analytics, and offer personalized insights to help companies make better decisions.
For example, AI can predict equipment maintenance needs, reducing downtime and improving productivity. By embracing AI, textile companies can stay ahead of the competition and operate more efficiently.
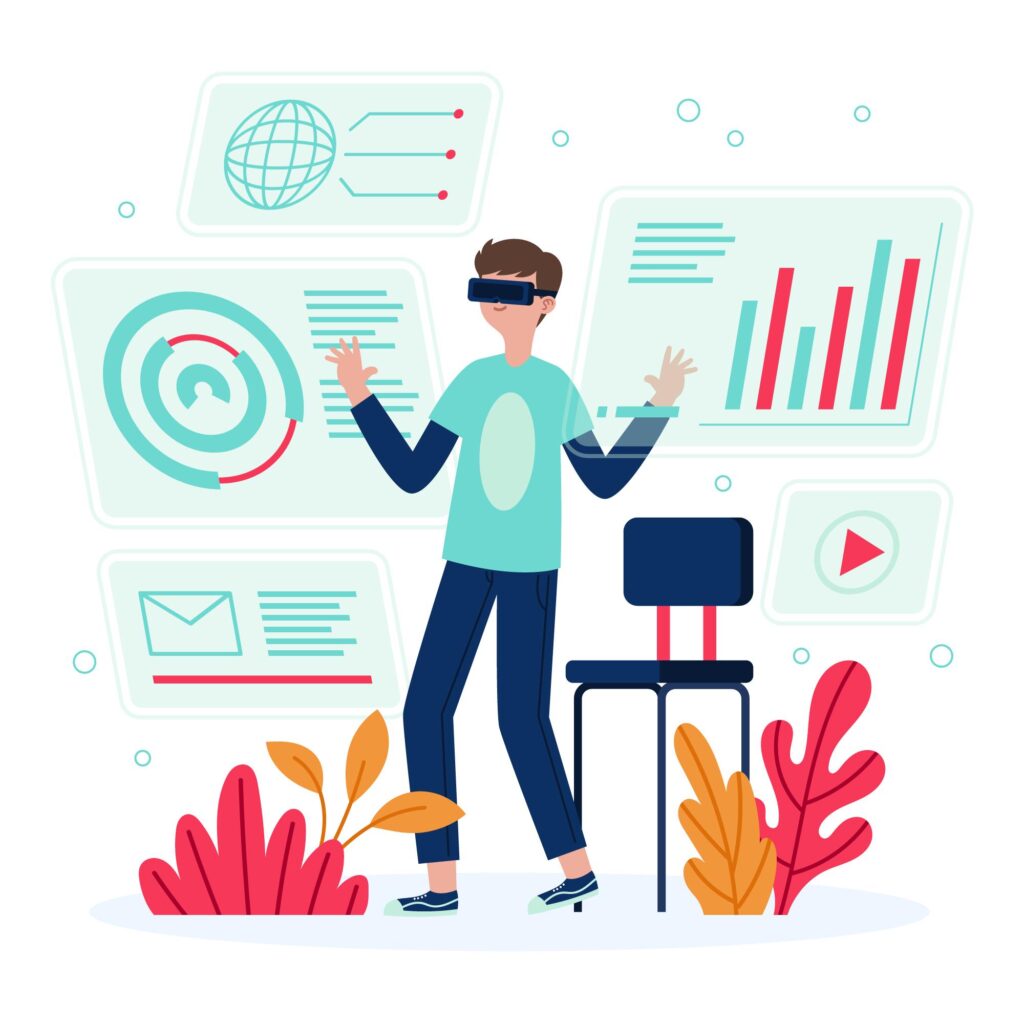
- IoT Integration
The Internet of Things (IoT) is another ERP future trend that will have a significant impact on the textile industry. IoT devices can collect real-time data from machines, vehicles, and other equipment, providing valuable insights into operations.
By integrating IoT with ERP systems, textile companies can monitor production processes, track inventory levels, and even predict equipment failures. This level of visibility will help companies optimize their operations and reduce costs.
- Sustainability and ESG Practices
As environmental concerns become more prominent, sustainability is becoming a key focus for textile companies. This has led to growing popularity of Green ERP systems or ERPs that assist businesses track their environmental impact and reduce waste.
These specialized systems can monitor energy consumption, water usage, and emissions, allowing companies to implement more sustainable practices. By adopting green ERP, textile companies can not only reduce their environmental footprint but also appeal to eco-conscious consumers.
- Enhanced Cybersecurity
As ERP systems become more advanced, the need for robust cybersecurity measures will shape the future of ERP. Cyber threats are a growing concern for all industries, and the textile sector is no exception.
Enhanced cybersecurity will be a critical ERP future trend, ensuring that sensitive business data is protected from unauthorized access. This includes advanced encryption, multi-factor authentication, and continuous monitoring to detect and respond to potential threats.
The textile industry is on the verge of significant technological advancements, with ERP systems at the forefront of this transformation. Understanding and embracing ERP future trends will be essential for textile companies aiming to remain competitive and efficient.
From AI and IoT integration to sustainability and enhanced cybersecurity, the future of ERP in the textile industry is filled with opportunities. By staying ahead of these trends, textile companies can not only improve their operations but also contribute to a more sustainable and secure industry.
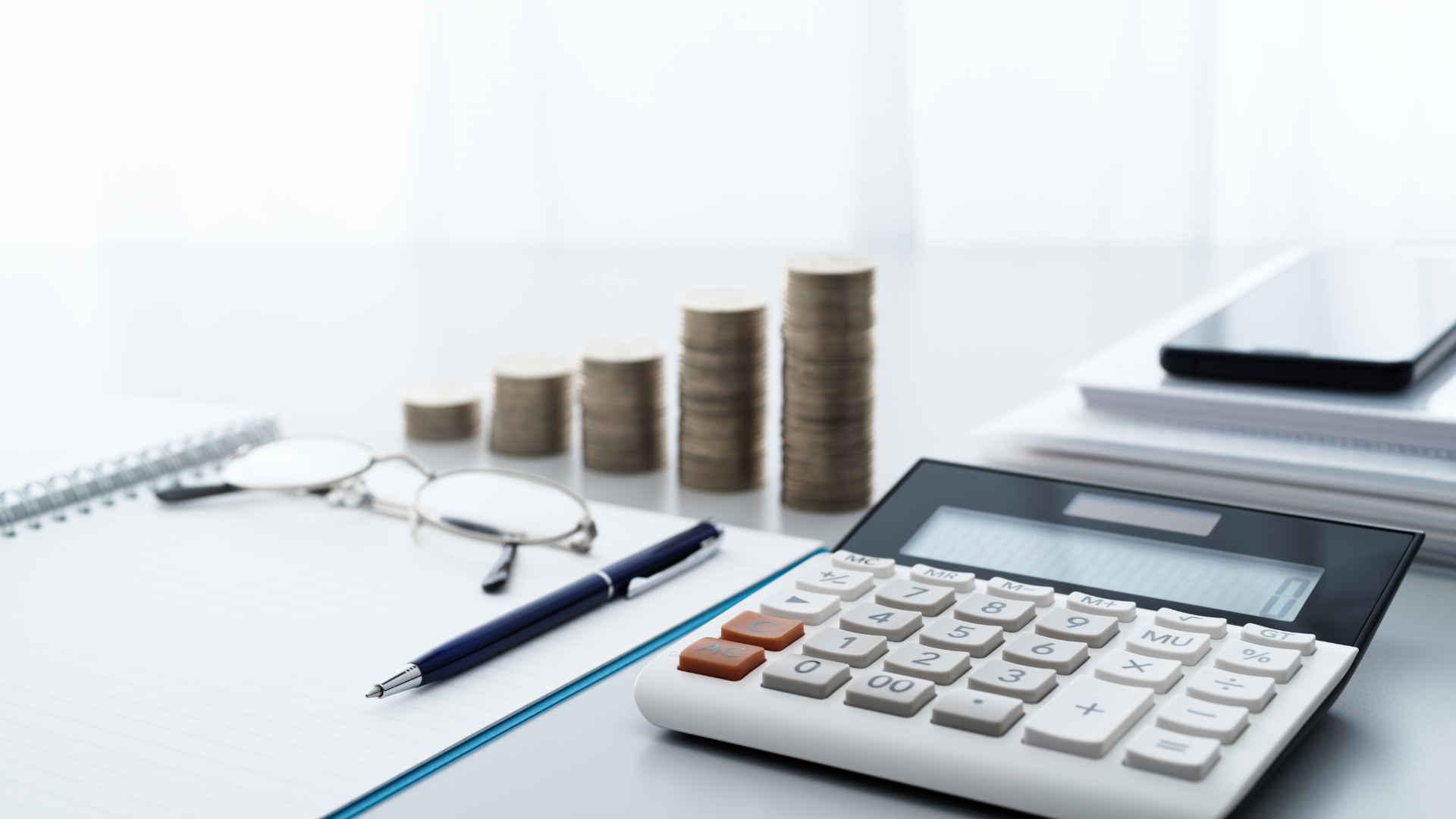
Customer Profile:
The customer, a well-established electrical distributor, manages a wide range of products for industrial and residential use, including wiring, switchgear, and electrical components.
Problem Statement:
For a long time, the customer relied on a generic software for managing their operations, including credit management. This software lacked the ability to scale along with the customer’s business leading to failure in meeting the demands of the growing business.
Some everyday problems the customer was experiencing included:
- Frequent manual oversight required for credit approvals, payment tracking, and outstanding balances.
- The need for human intervention led to delays in payment processing, increased chances of miscommunication, and occasional errors in credit allocation.
- Negative impact on cash flow and decreasing customer satisfaction.
Solution:
The customer recognized the need for a more advanced, industry-specific system to streamline credit management, minimize manual efforts, and reduce errors. They decided to implement DistFlow ELEC ERP, an industry-focused software designed to automate key business processes for electrical distributors.
Key solution highlights include:
- Automated Credit Approval and Tracking: DistFlow ELEC ERP enabled the customer to automate credit approvals, track payment terms, and monitor outstanding balances, reducing the need for manual intervention.
- Real-Time Credit and Payment Visibility: Provided a clear, real-time view of each client’s credit standing, ensuring timely actions on overdue accounts.
- Automatic Reminders and Alerts: Set up automatic reminders for overdue payments and alerts for credit limits, helping the customer stay proactive in collections.
- Integrated Reporting and Analysis: Generated detailed credit reports, facilitating better financial forecasting and cash flow management.
- Enhanced Business Process Automation: Beyond credit management, DistFlow ELEC ERP improved inventory, order processing, and customer management processes, leading to a more cohesive operational flow.
Results:
Switching to DistFlow ELEC ERP delivered impressive results for the electrical distributor, including:
- 45% reduction in manual credit management tasks, minimizing the risk of human error.
- 35% improvement in payment collection time, thanks to automated alerts and reminders.
- 20% increase in cash flow predictability, facilitated by real-time credit visibility and automated tracking.
- 25% reduction in operational costs, achieved by cutting down on manual intervention and increasing process efficiency.
Contact Us
So, what are you waiting for? Don't let your competition get ahead of you. Contact us today to discuss your Electrical Distribution ERP needs and let us help you achieve your business goals!
html,body{ margin: 0px; } #crmWebToEntityForm.zcwf_lblLeft { width:100%; padding: 25px; margin: 0 auto; box-sizing: border-box; } #crmWebToEntityForm.zcwf_lblLeft * { box-sizing: border-box; } #crmWebToEntityForm{text-align: left;} #crmWebToEntityForm * { direction: ltr; } .form-row { display: flex; flex-wrap: wrap; } .form-field { flex: 0 0 50%; max-width: 50%; } .zcwf_lblLeft .zcwf_title { word-wrap: break-word; padding: 0px 6px 10px; font-weight: bold; } .zcwf_lblLeft .zcwf_col_fld input[type=text], .zcwf_lblLeft .zcwf_col_fld textarea { width: 100%; border: 1px solid #ccc !important; resize: vertical; border-radius: 2px; float: left; } .zcwf_lblLeft .zcwf_col_lab { width: 30%; word-break: break-word; padding: 0px 6px 0px; margin-right: 10px; margin-top: 5px; float: left; min-height: 1px; } .zcwf_lblLeft .zcwf_col_fld { float: left; width: 100%; padding: 0px 6px 0px; position: relative; margin-top: 5px; } .zcwf_lblLeft .zcwf_privacy{padding: 6px;} .zcwf_lblLeft .wfrm_fld_dpNn{display: none;} .dIB{display: inline-block;} .zcwf_lblLeft .zcwf_col_fld_slt { width: 60%; border: 1px solid #ccc; background: #fff; border-radius: 4px; font-size: 12px; float: left; resize: vertical; padding: 2px 5px; } .zcwf_lblLeft .zcwf_row:after, .zcwf_lblLeft .zcwf_col_fld:after { content: ''; display: table; clear: both; } .zcwf_lblLeft .zcwf_col_help { float: left; margin-left: 7px; font-size: 12px; max-width: 35%; word-break: break-word; } .zcwf_lblLeft .zcwf_help_icon { cursor: pointer; width: 16px; height: 16px; display: inline-block; background: #fff; border: 1px solid #ccc; color: #ccc; text-align: center; font-size: 11px; line-height: 16px; font-weight: bold; border-radius: 50%; } .zcwf_lblLeft .zcwf_row {/*margin: 15px 0px;*/} .zcwf_lblLeft .formsubmit { margin-right: 5px; cursor: pointer; color: #333; font-size: 12px; } .zcwf_lblLeft .zcwf_privacy_txt { width: 90%; color: rgb(0, 0, 0); font-size: 12px; font-family: Arial; display: inline-block; vertical-align: top; color: #333; padding-top: 2px; margin-left: 6px; } .zcwf_lblLeft .zcwf_button { font-size: 17px; color: #ffffff; /*border: 1px solid #ccc;*/ padding: 13px 20px; border-radius: 4px; cursor: pointer; max-width: 120px; overflow: hidden; text-overflow: ellipsis; white-space: nowrap; margin-bottom: 6px; } .zcwf_lblLeft .zcwf_tooltip_over{ position: relative; } .zcwf_lblLeft .zcwf_tooltip_ctn{ position: absolute; background: #dedede; padding: 3px 6px; top: 3px; border-radius: 4px;word-break: break-word; min-width: 100px; max-width: 150px; color: #333; z-index: 100; } .zcwf_lblLeft .zcwf_ckbox{ float: left; } .zcwf_lblLeft .zcwf_file{ width: 55%; box-sizing: border-box; float: left; } .clearB:after{ content:''; display: block; clear: both; } @media all and (max-width: 600px) { .zcwf_lblLeft .zcwf_col_lab, .zcwf_lblLeft .zcwf_col_fld { width: auto; float: none !important; } .zcwf_lblLeft .zcwf_col_help {width: 40%;} } -None- Advertisement Cold Call Employee Referral External Referral Website Partner Public Relations Sales Mail Alias Seminar Partner Seminar-Internal Trade Show Web Download Web Research Chat Tex EventCaptcha validation failed. If you are not a robot then please try again.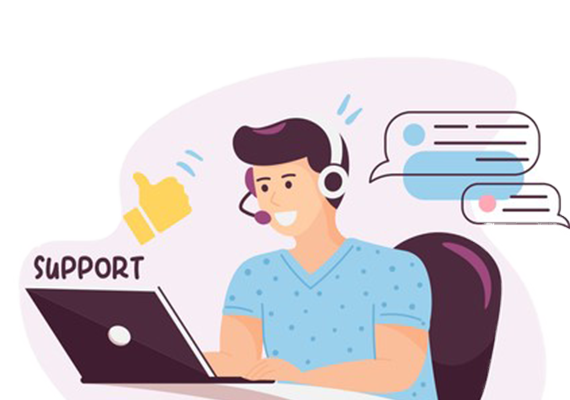
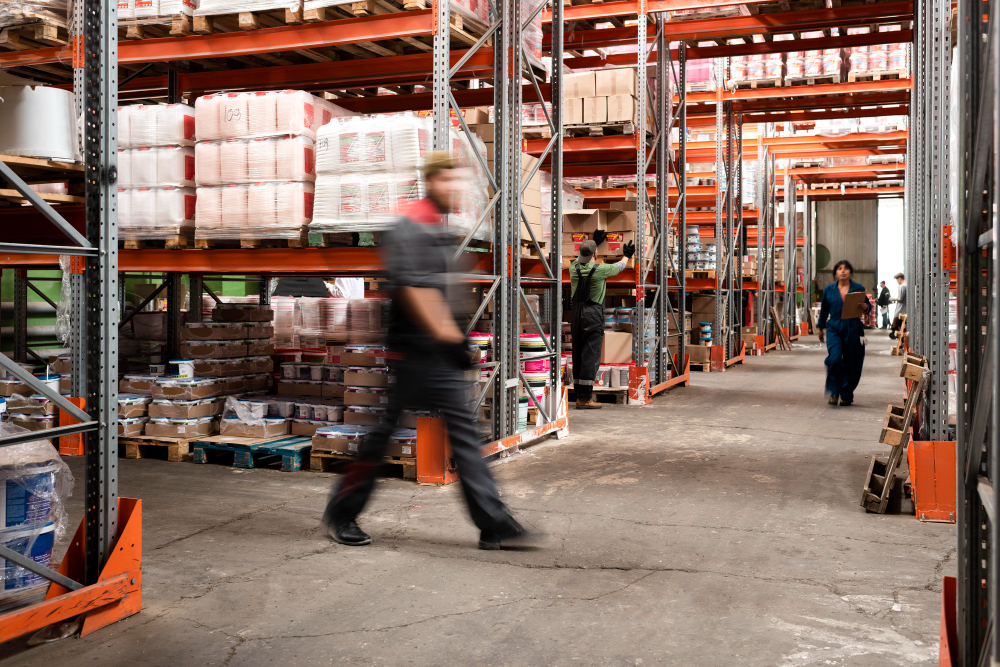
Customer Profile:
Our customer is a prominent PCB distributor with an expansive product portfolio. They manage extensive distribution operations across multiple countries distributing high-quality circuit boards to electronics manufacturers, suppliers, and other clients worldwide.
Problem Statement:
As the customer’s operations grew, they started facing complexities of managing multiple warehouses. The lack of a centralized system led to challenges in stock visibility, miscommunication between locations, and delays in order processing.
Each warehouse operated in isolation, making it difficult to synchronize inventory, track stock levels, and efficiently allocate resources. This disjointed structure resulted in frequent stockouts, overstocking, delayed shipments, and even order fulfillment errors.
Ultimately, these issues were beginning to impact customer satisfaction and operational costs. The customer needed a solution that would streamline inventory management, facilitate real-time data sharing across all warehouses and optimize order fulfillment.
Solution:
To address these challenges, the customer implemented DistFlow PCB ERP, a software designed specifically for PCB distributors.
- DistFlow PCB offered a unified platform to manage inventory, logistics, and order processing across all warehouse locations.
- Customer got real-time visibility into stock levels across each warehouse, allowing them to efficiently track inventory, manage replenishments, and avoid stock discrepancies.
- DistFlow PCB’s automated alerts and reorder functions ensured that stockouts were minimized, while overstocking was controlled through accurate demand forecasting.
- The PCB ERP system enabled seamless communication between warehouses, facilitating smoother inter-warehouse transfers and improving order processing time.
- Additionally, the customer could assign priority to orders and allocate resources as needed, streamlining their fulfillment process and reducing delays.
- DistFlow PCB further simplified reporting and analytics, allowing the customer to make data-driven decisions and continually refine their logistics operations.
Results:
The implementation of DistFlow PCB yielded impressive results for the customer’s multi-location distribution operations:
- 40% reduction in order processing time, enabling faster and more accurate fulfillment.
- 30% decrease in stockouts and overstocking issues, leading to optimal inventory levels across warehouses.
- 25% increase in order fulfillment efficiency, as real-time data and automated processes reduced manual errors.
- 20% improvement in customer satisfaction, driven by more consistent on-time deliveries and accurate order fulfillment.
Contact Us
So, what are you waiting for? Don't let your competition get ahead of you. Contact us today to discuss your PCB ERP needs and let us help you achieve your business goals!
html,body{ margin: 0px; } #crmWebToEntityForm.zcwf_lblLeft { width:100%; padding: 25px; margin: 0 auto; box-sizing: border-box; } #crmWebToEntityForm.zcwf_lblLeft * { box-sizing: border-box; } #crmWebToEntityForm{text-align: left;} #crmWebToEntityForm * { direction: ltr; } .form-row { display: flex; flex-wrap: wrap; } .form-field { flex: 0 0 50%; max-width: 50%; } .zcwf_lblLeft .zcwf_title { word-wrap: break-word; padding: 0px 6px 10px; font-weight: bold; } .zcwf_lblLeft .zcwf_col_fld input[type=text], .zcwf_lblLeft .zcwf_col_fld textarea { width: 100%; border: 1px solid #ccc !important; resize: vertical; border-radius: 2px; float: left; } .zcwf_lblLeft .zcwf_col_lab { width: 30%; word-break: break-word; padding: 0px 6px 0px; margin-right: 10px; margin-top: 5px; float: left; min-height: 1px; } .zcwf_lblLeft .zcwf_col_fld { float: left; width: 100%; padding: 0px 6px 0px; position: relative; margin-top: 5px; } .zcwf_lblLeft .zcwf_privacy{padding: 6px;} .zcwf_lblLeft .wfrm_fld_dpNn{display: none;} .dIB{display: inline-block;} .zcwf_lblLeft .zcwf_col_fld_slt { width: 60%; border: 1px solid #ccc; background: #fff; border-radius: 4px; font-size: 12px; float: left; resize: vertical; padding: 2px 5px; } .zcwf_lblLeft .zcwf_row:after, .zcwf_lblLeft .zcwf_col_fld:after { content: ''; display: table; clear: both; } .zcwf_lblLeft .zcwf_col_help { float: left; margin-left: 7px; font-size: 12px; max-width: 35%; word-break: break-word; } .zcwf_lblLeft .zcwf_help_icon { cursor: pointer; width: 16px; height: 16px; display: inline-block; background: #fff; border: 1px solid #ccc; color: #ccc; text-align: center; font-size: 11px; line-height: 16px; font-weight: bold; border-radius: 50%; } .zcwf_lblLeft .zcwf_row {/*margin: 15px 0px;*/} .zcwf_lblLeft .formsubmit { margin-right: 5px; cursor: pointer; color: #333; font-size: 12px; } .zcwf_lblLeft .zcwf_privacy_txt { width: 90%; color: rgb(0, 0, 0); font-size: 12px; font-family: Arial; display: inline-block; vertical-align: top; color: #333; padding-top: 2px; margin-left: 6px; } .zcwf_lblLeft .zcwf_button { font-size: 17px; color: #ffffff; /*border: 1px solid #ccc;*/ padding: 13px 20px; border-radius: 4px; cursor: pointer; max-width: 120px; overflow: hidden; text-overflow: ellipsis; white-space: nowrap; margin-bottom: 6px; } .zcwf_lblLeft .zcwf_tooltip_over{ position: relative; } .zcwf_lblLeft .zcwf_tooltip_ctn{ position: absolute; background: #dedede; padding: 3px 6px; top: 3px; border-radius: 4px;word-break: break-word; min-width: 100px; max-width: 150px; color: #333; z-index: 100; } .zcwf_lblLeft .zcwf_ckbox{ float: left; } .zcwf_lblLeft .zcwf_file{ width: 55%; box-sizing: border-box; float: left; } .clearB:after{ content:''; display: block; clear: both; } @media all and (max-width: 600px) { .zcwf_lblLeft .zcwf_col_lab, .zcwf_lblLeft .zcwf_col_fld { width: auto; float: none !important; } .zcwf_lblLeft .zcwf_col_help {width: 40%;} } -None- Advertisement Cold Call Employee Referral External Referral Website Partner Public Relations Sales Mail Alias Seminar Partner Seminar-Internal Trade Show Web Download Web Research Chat Tex EventCaptcha validation failed. If you are not a robot then please try again.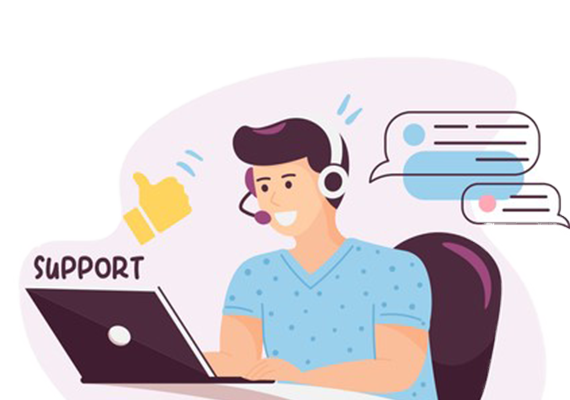
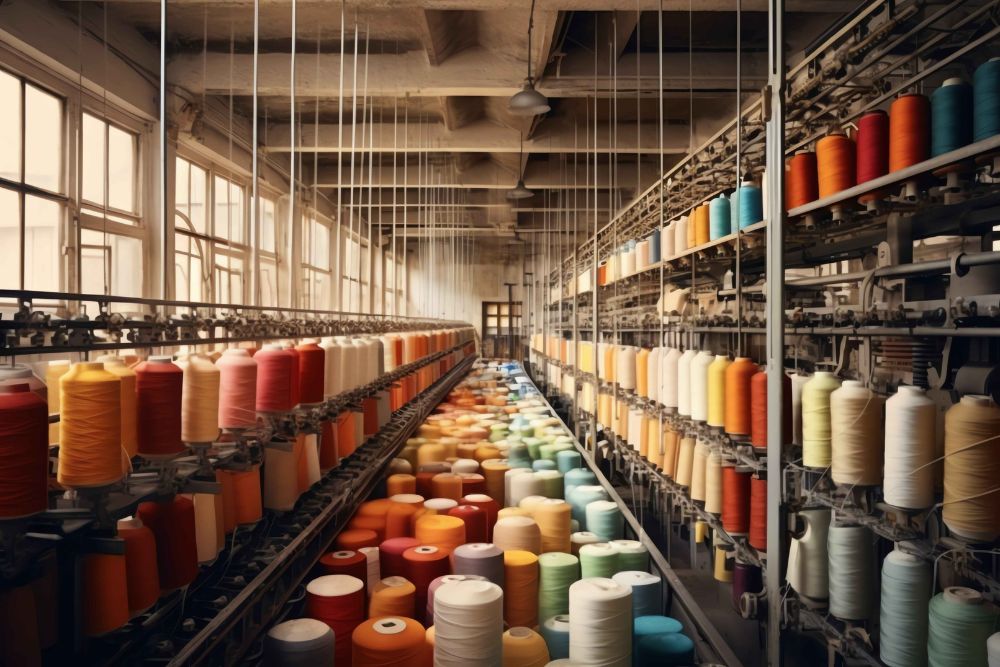
Reports on ERP statistics show that 95% of businesses improve their process after implementing an ERP software – and textile mills are no exception.
Implementing textile mill ERP streamlines operations, enhances productivity, and ensures better resource management. However, successfully implementing ERP software presents its own set of challenges. In fact, 55% to 75% of ERP projects fail to meet their objectives, often due to poor implementation strategies.
A successful implementation requires careful planning and adherence to ERP best practices. In this blog, we’ll explore the key considerations for implementing ERP in textile mills, followed by the best practices that can help you achieve optimal results. Let’s begin.
Key Considerations for Successful Implementation of Textile Mill ERP
When considering ERP implementation tips for your textile business, here are five key factors to ensure a smooth and effective transition:
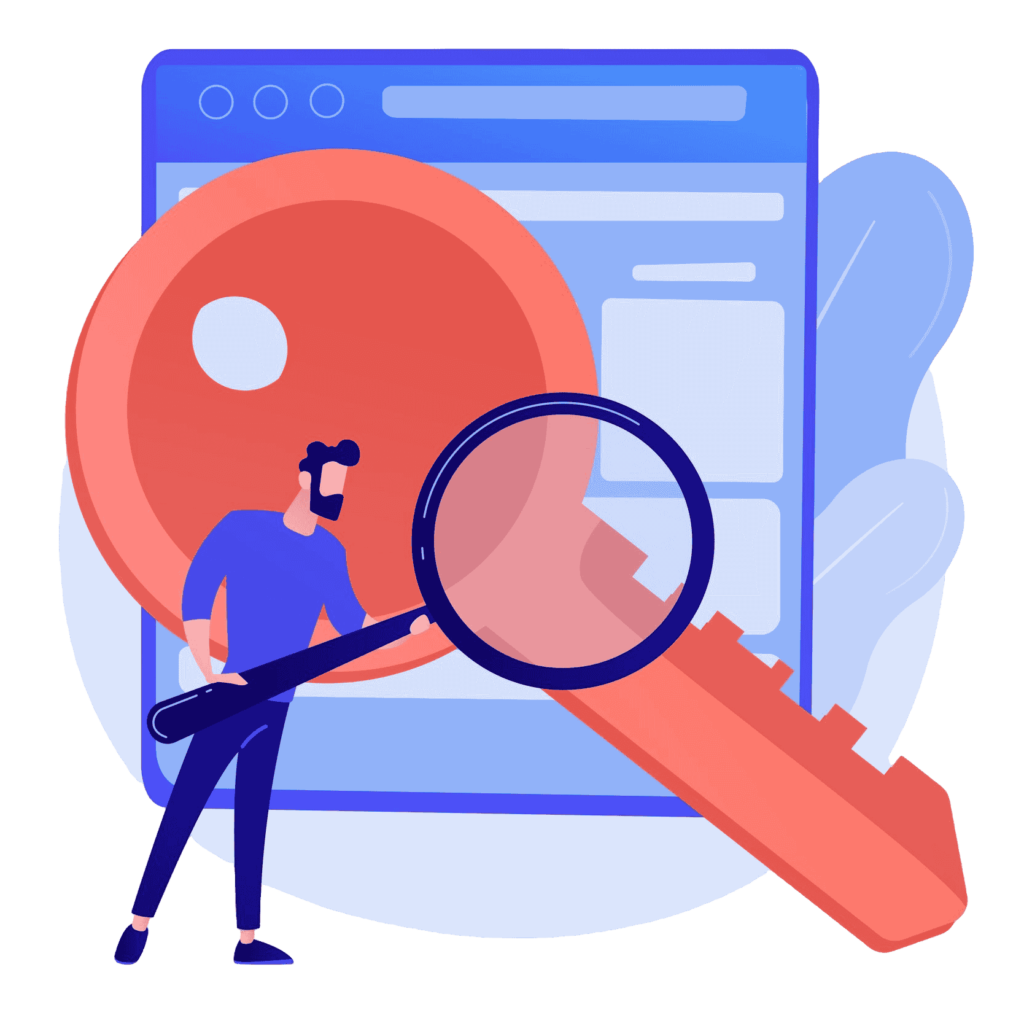
1] Industry Specific Customizations:
Textile mill operations such as spinning, weaving, dyeing, finishing, etc., are highly specialized. A generic ERP solution will not necessarily address these needs. So, it is important to choose a textile mill ERP that can be customized to meet the specific workflows of your mill. Tailoring the ERP software ensures that it accommodates your processes, making operations more streamlined and efficient.
2] Seamless Integration with Existing Systems
Textile mills often use specialized equipment and software, including CAD systems, looms and quality control tools. The ERP implementation should involve a smooth integration with these existing systems, allowing for seamless data flow across departments without disrupting current operations. A well-integrated ERP solution helps unify the mill’s systems, promoting better coordination and efficiency.
3] Scalability
As your textile business grows, production volumes will naturally increase. The ERP software must be scalable to support future expansion without compromising efficiency. A scalable solution ensures that, as your product line diversifies and operations grow, your system can adapt without loss in performance, making scalability a crucial aspect of ERP best practices.
4] Cost and ROI Analysis
Implementing an ERP system requires significant investment. Before proceeding, perform a comprehensive cost analysis that includes setup, customization, training, and ongoing maintenance. Additionally, assess the expected ROI by considering the potential gains in efficiency, productivity, and cost savings. Evaluating costs alongside projected benefits helps you make informed decisions, aligning with the best ERP implementation tips.
5] Data Security and Privacy
The current digital era consists of many cyber security threats when it comes to software applications. A robust textile mill ERP should offer strong data security features to protect against breaches and cyber threats. Compliance with data protection regulations is also essential to avoid legal issues and maintain the trust of stakeholders.
ERP Best Practices for Textile Mills
To ensure a smooth and successful ERP implementation in your textile business, following ERP best practices is essential. Here are key steps that can make all the difference:
1] Detailed Requirements Gathering
A critical step for successful ERP implementation involves thorough requirements gathering from all stakeholders. Engage representatives from various departments to understand their specific needs and challenges. This comprehensive understanding aids in selecting the appropriate ERP solution and customizing it to meet the mill's unique requirements.
2] Clear Communication Plan
Establishing a clear communication plan ensures that all stakeholders are kept informed about the project's progress, milestones, and any changes. Regular updates and feedback sessions are crucial to ensure everyone is aligned and can contribute to the project's success. This transparency fosters collaboration and mitigates the risk of misunderstandings or misaligned objectives.
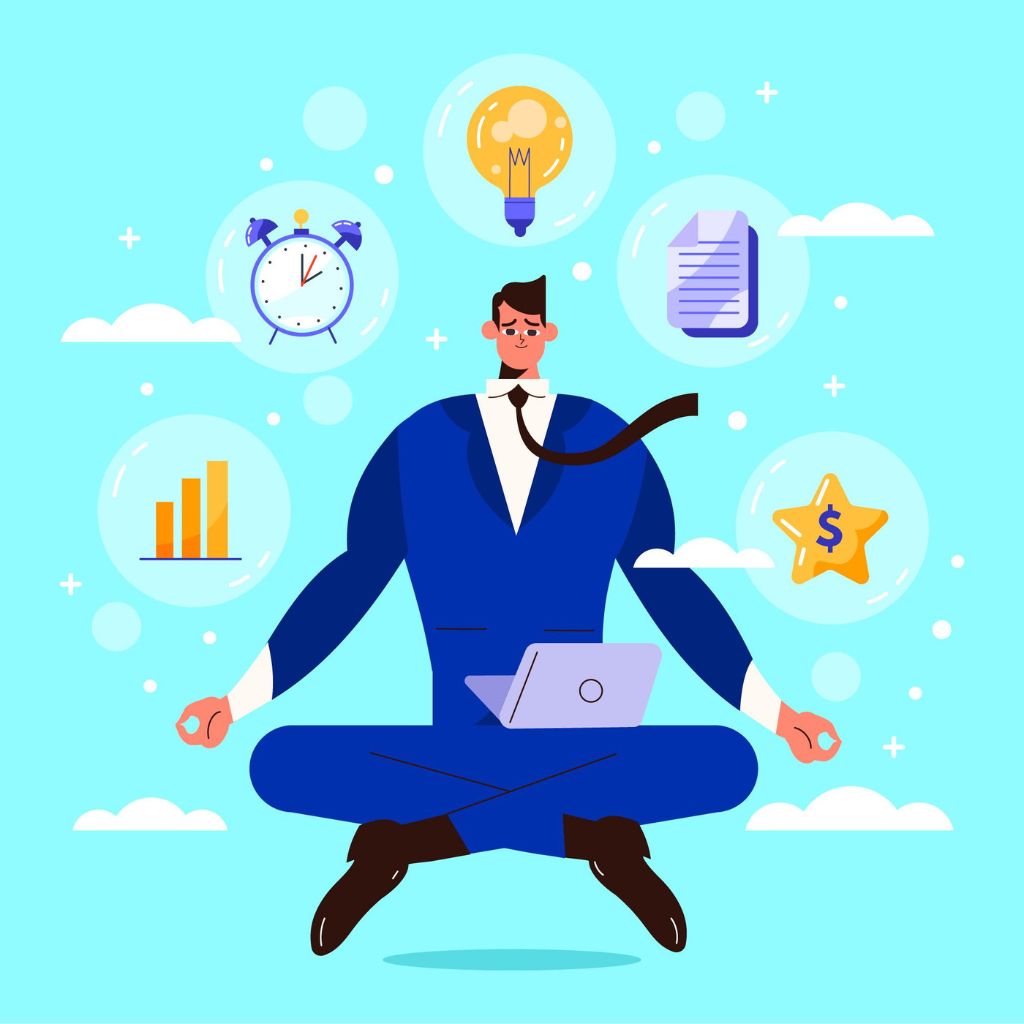
3] Continuous Monitoring and Evaluation
ERP implementation is not a one-time event but an ongoing process. It is crucial to continuously monitor the system's performance and gather user feedback. Regular evaluations help identify areas for improvement and ensure that the ERP software continues to meet the mill's evolving needs. Proactive monitoring is one of the ERO best practices as it allows for timely adjustments and prevents potential issues from escalating, ensuring long-term success and efficiency.
4] User Training and Support
Comprehensive training programs are essential to equip staff with the necessary knowledge and skills to use the system effectively. Effective user training and support enhances user adoption, ensuring that the ERP software delivers its intended benefits. By investing in thorough training and robust support structures, organizations can maximize the value and efficiency of their ERP software.
5] Strong Vendor Partnership
Forming a solid partnership with an ERP vendor is essential for a successful implementation. It is vital to select a vendor with a proven track record in the textile industry who also provides continuous support, updates, and training. A dependable vendor can promptly address issues and ensure the system stays current with industry advancements.
Implementing textile mill ERP can greatly boost operational efficiency, productivity, and competitiveness. The success of this implementation hinges on careful planning and execution. By focusing on factors such as customization, integration, scalability, cost, and data security, textile mills can choose and deploy an ERP system tailored to their unique requirements.
Moreover, adhering to ERP best practices include detailed requirement gathering, clear communication, continuous monitoring, user training, and forging a robust partnership with the vendor. These steps can significantly enhance the likelihood of a successful ERP implementation.
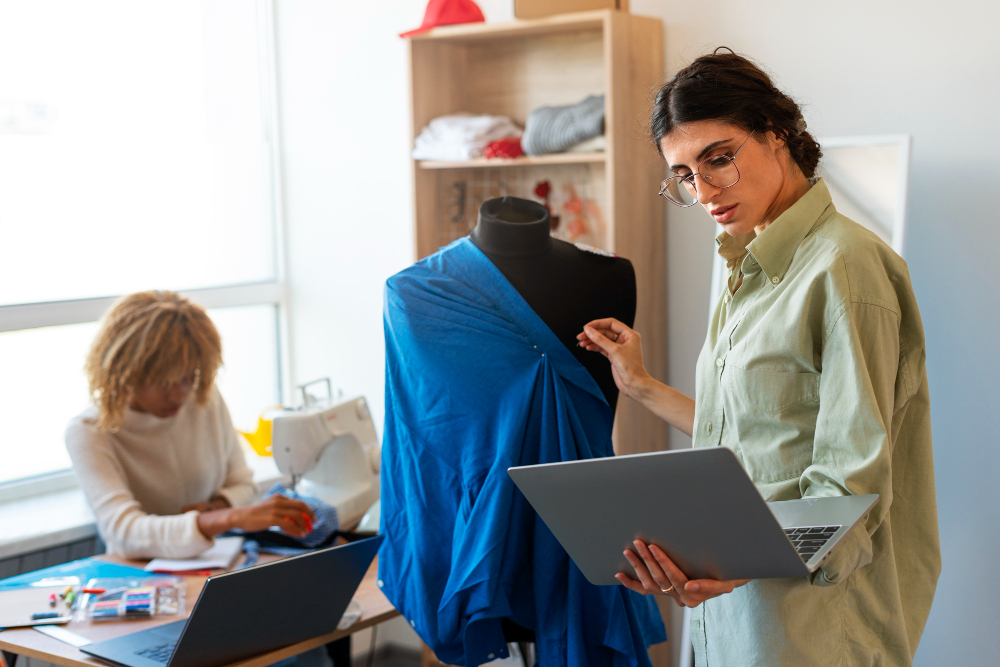
Small and Medium Enterprises (SMEs) form the backbone of the textile industry, accounting for nearly 75% of its value chain. Despite their crucial role, SMEs face challenges that are often distinct from those of larger manufacturers.
These challenges include managing processes such as spinning, weaving, printing, and stitching—each requiring specific solutions tailored to their operations. To effectively address these unique needs, ERP for small businesses in the textile sector offers a highly customizable solution.
By adapting to the specific requirements of SMEs, ERP systems can streamline processes, enhance productivity, and resolve operational bottlenecks. In this blog, we’ll explore the unique challenges SMEs face and how ERP can be customized to meet their needs in the textile industry.
Understanding the Unique Challenges and Specific Needs of Textile SMEs
Small and medium-sized enterprises frequently face resource constraints, regulatory compliance, and market competitiveness. Addressing these challenges and needs requires tailor-made methods that improve operational efficiency, innovation, and sustainability.
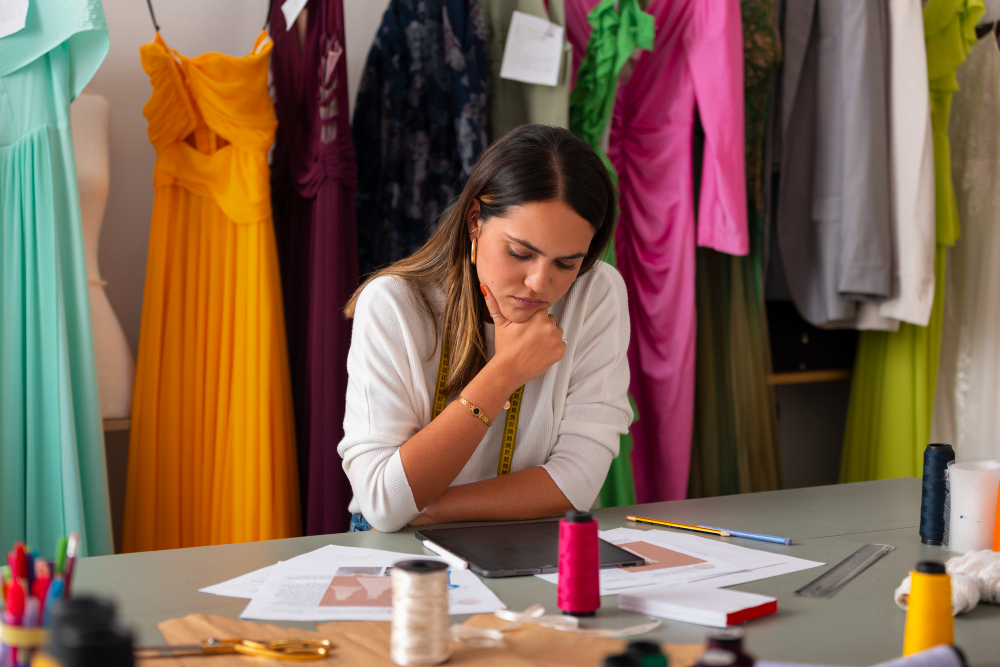
Unique Challenges
Textile SMEs typically operate with smaller teams and constrained resources, making it difficult to manage various aspects of their business efficiently. Some of their key challenges include:
- Managing Inventory: SMEs often struggle to keep accurate track of stock levels, balancing the risk of overstocking and stock shortages. Effective inventory management of raw materials and finished products is crucial for smooth operations.
- Tracking Orders: Monitoring the status of customer orders, ensuring accurate order processing, and providing customers with timely updates can be a logistical challenge, especially when dealing with multiple clients.
- Maintaining Quality Control: Ensuring that all products meet industry standards and customer expectations can be demanding, especially with limited resources.
- Ensuring Timely Deliveries: Coordinating production schedules, managing logistics, and ensuring that products are delivered on time is a constant challenge in the fast-moving textile market.
- Adapting to Market Changes: The textile market can be volatile, with changing trends and demands. SMEs need to stay agile and responsive to these shifts to remain competitive.
- Managing Costs: Balancing operational costs while maintaining profitability is critical. SMEs must carefully control expenses related to raw materials, production, and overheads to sustain growth.
Specific Needs
To address these unique challenges, textile businesses require SME ERP solutions that are not only industry-specific but also adaptable to their evolving business needs. Here are some key features that SMEs in the textile industry require from their ERP systems:
- Cost-Effectiveness: Given their limited financial resources, SMEs need cost-effective ERP for small businesses that can manage their entire operations without overwhelming their budget. An affordable SME ERP solution allows businesses to focus on key areas like production and market expansion while keeping costs under control.

- Simple-to-Use Software: Many SMEs lack considerable IT resources and experience. Simple-to-use software ensures that all team members can easily learn and apply the system. This lowers training time and expenses while increasing productivity by allowing staff to focus on their primary responsibilities.
- Software Flexibility: As SMEs grow, their business requirements change. A flexible ERP system with scalable features ensures that Textile ERP customization is possible, allowing businesses to introduce new functionalities and adapt the software to their expanding needs without needing a major overhaul.
5 Key Customization Features of ERP for Small Businesses
Textile SMEs seek specialized solutions to meet their specific challenges and operating requirements. Let us look at the 5 features of ERP for small businesses that provide a huge advantage to SMEs to effectively address their challenges and increase overall operational efficiency.
1] User-Friendly Interface: ERP for SMEs should be intuitive and easy to navigate. Textile SMEs usually have a wide range of staff who necessarily do not have specialized experience in handling an advanced software.
An ERP with a clean, user-friendly design reduces the learning curve, allowing all employees to use it effectively without extensive training. This improves productivity and ensures that teams can focus on their core responsibilities without struggling with complicated software.
2] Modular Architecture: Textile SMEs often focus on specific areas like yarn spinning, dyeing, or weaving, making modular architecture a crucial feature. This enables businesses to customize their ERP by adding or removing modules as needed.
As their business evolves, they can easily scale the system by incorporating additional functions. This flexibility ensures that the ERP for small businesses can grow alongside the company, providing continuous support for its expanding needs.
3] Integration Capabilities: Efficient Textile ERP customization requires robust integration capabilities. SMEs typically use different tools for various functions, and the ERP system should seamlessly integrate with these existing software tools.
By doing so, the ERP facilitates smooth data flow across departments, eliminating the need for manual data entry and reducing the risk of errors. This integration also enhances overall efficiency by creating a unified platform for managing all business operations.
4] Scalable Infrastructure: A scalable infrastructure is vital as textile SMEs grow. The ERP system must handle increasing data volumes, users, and tasks without losing performance.
With a scalable ERP for small businesses, SMEs can expand their operations, manage more data, and integrate larger teams without needing a complete system overhaul. This scalability ensures the ERP remains reliable and effective, supporting long-term growth.
5] Industry-Specific Modules: One of the greatest advantages of Textile ERP customization is the availability of industry-specific modules tailored to textile manufacturing processes. These modules are designed to manage inventory, track dyeing and printing, and ensure quality control, making them highly relevant for SMEs in the textile sector.
By integrating these specialized modules, the ERP system aligns perfectly with the business's unique requirements, ensuring smooth operations and enhanced productivity.
ERP for small businesses offers tailored solutions that help streamline operations, boost productivity, and support growth. By choosing a customizable ERP system, textile SMEs can meet their unique needs while remaining flexible as their business evolves. As they continue to face challenges related to efficiency, scalability, and industry-specific processes, an ERP solution designed with SMEs in mind empowers them to stay competitive, innovate, and grow in a rapidly changing market.
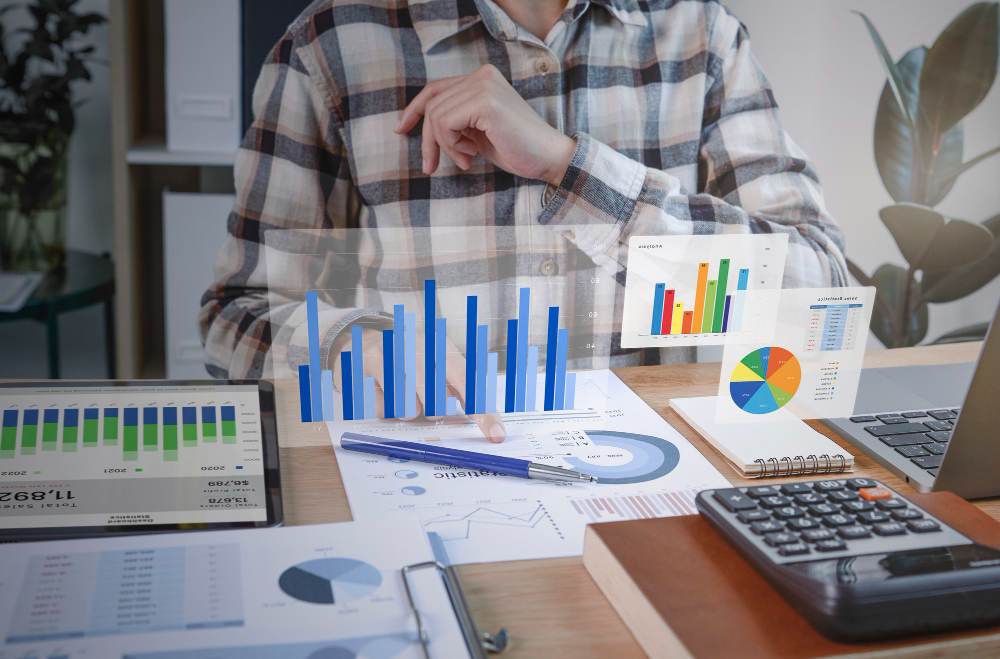
Managing the finances of a textile business is a very difficult task due to the sheer volume of transactions that take place on a daily basis. Following traditional or manual methods of financial management may act as a hinderance towards better textile financial planning.
The smartest decision a textile manufacturer can make in this regard is to implement ERP financial management. In this blog we are going to discuss some of the common issues faced by textile businesses with their finances and elaborate on the key features the financial management module of the ERP software offers.
Common Issues of Financial Management in the Textile Industry
Textile businesses operational efficiency and financial health can be severely impacted by problems such as inaccuracies in financial data, cash flow disruptions, regulatory non-compliance, and delays in payment processing.
Let us discuss in detail these 5 common issues below:

1] Delays in Payment Processing: Manual handling of invoices and payments is prone to errors and delays, which disrupt operations and cash flow. The lack of automation leads to slow payment processing, impacting the overall financial health of textile businesses.
2] Challenges in Tracking Payment Status: With numerous transactions, textile companies often struggle to track payment statuses accurately. Without proper tracking, payment discrepancies occur, leading to confusion and operational delays.
3] Cash Flow Disruptions: Cash flow is critical for textile businesses. Unpredictable sales cycles and customer payment delays can disrupt cash flow, affecting the ability to meet financial obligations like paying suppliers and managing inventory.
4] Regulatory Non-Compliance: The textile industry must adhere to various regulations, including tax laws, environmental standards, and labor laws. Lack of awareness or understanding of these regulations and inadequate internal controls can lead to compliance issues. Regulatory compliance is critical in the textile industry for upholding sustainability. Failure to comply can result in penalties and legal issues.
5] Inaccurate Financial Data: Textile companies need reliable data for budgeting, forecasting, and financial planning. Manual data entry errors, outdated systems, and lack of integration between financial software can result in inaccurate financial data. This eventually leads to poor decision-making by textile manufacturers with regards to financial management.
Key Features of ERP Financial Management
The ERP software consists of a financial management module that is specifically designed to greatly improve the financial processes of textile companies. Here, we highlight the essential features that make ERP financial management a vital solution for tackling the specific financial challenges in the textile industry, ensuring better efficiency, accuracy, and compliance.
1] Efficient Invoicing and Purchase Orders:
The ERP financial management module offers efficient invoicing and purchase order features. This helps streamline the billing process and ensures that invoices are generated promptly. It also helps manage purchase orders effectively. By automating these processes, the ERP financial management module reduces manual work and speeds up transactions.
2] Payment Tracking:
Payment tracking is another key feature of the ERP financial management module. It allows textile manufacturers to monitor all incoming and outgoing payments. This feature provides a clear view of payment statuses and helps prevent issues related to payment delays. Accurate tracking ensures that payments are processed on time and reduces the risk of financial inconsistencies.
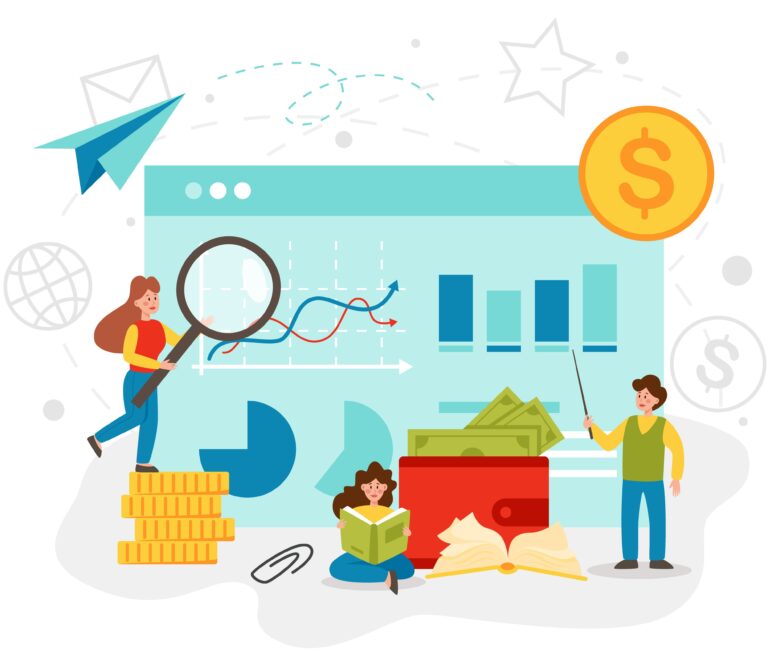
3] Account Payable and Receivables:
Managing accounts payable and receivables can be complex due to the volume of transactions that take place in a textile business. The ERP financial management module simplifies this task by automating accounts payable and receivables processes. It helps manage invoices, track payments, and handle outstanding balances. This feature improves accuracy and efficiency in managing financial transactions.
4] Compliance and Controls:
Compliance and control are crucial for avoiding legal and regulatory issues like fines and sanctions. The ERP financial management module includes tools for ensuring compliance with financial regulations. These tools include automated reporting, audit trails, real-time monitoring, and internal controls. They help monitor financial activities, maintain adherence to standards, and protect the company from potential penalties.
5] Financial Reporting and Analytics:
Financial reporting and analytics are critical for making informed decisions. The ERP financial management module provides comprehensive reporting and analytics tools. It offers detailed financial reports and insights into business performance. These tools help companies analyze their financial data and make strategic decisions based on accurate information.
Implementing ERP financial management in textile businesses is crucial for addressing common financial challenges like payment delays, tracking difficulties, cash flow issues, and compliance risks. With features like efficient invoicing, payment tracking, and real-time analytics, ERP ensures accuracy and compliance, ultimately improving financial health and decision-making. Textile manufacturers who integrate ERP into their operations can better manage their financial planning, leading to long-term success.
Contact Us
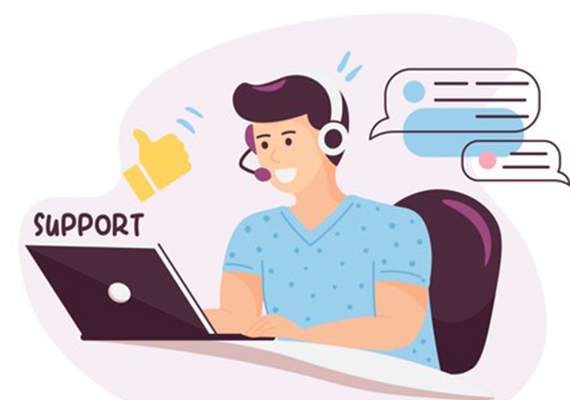