All Resources
Read and get updated on how we progress
- All Resources
- Blog
- Customer Story
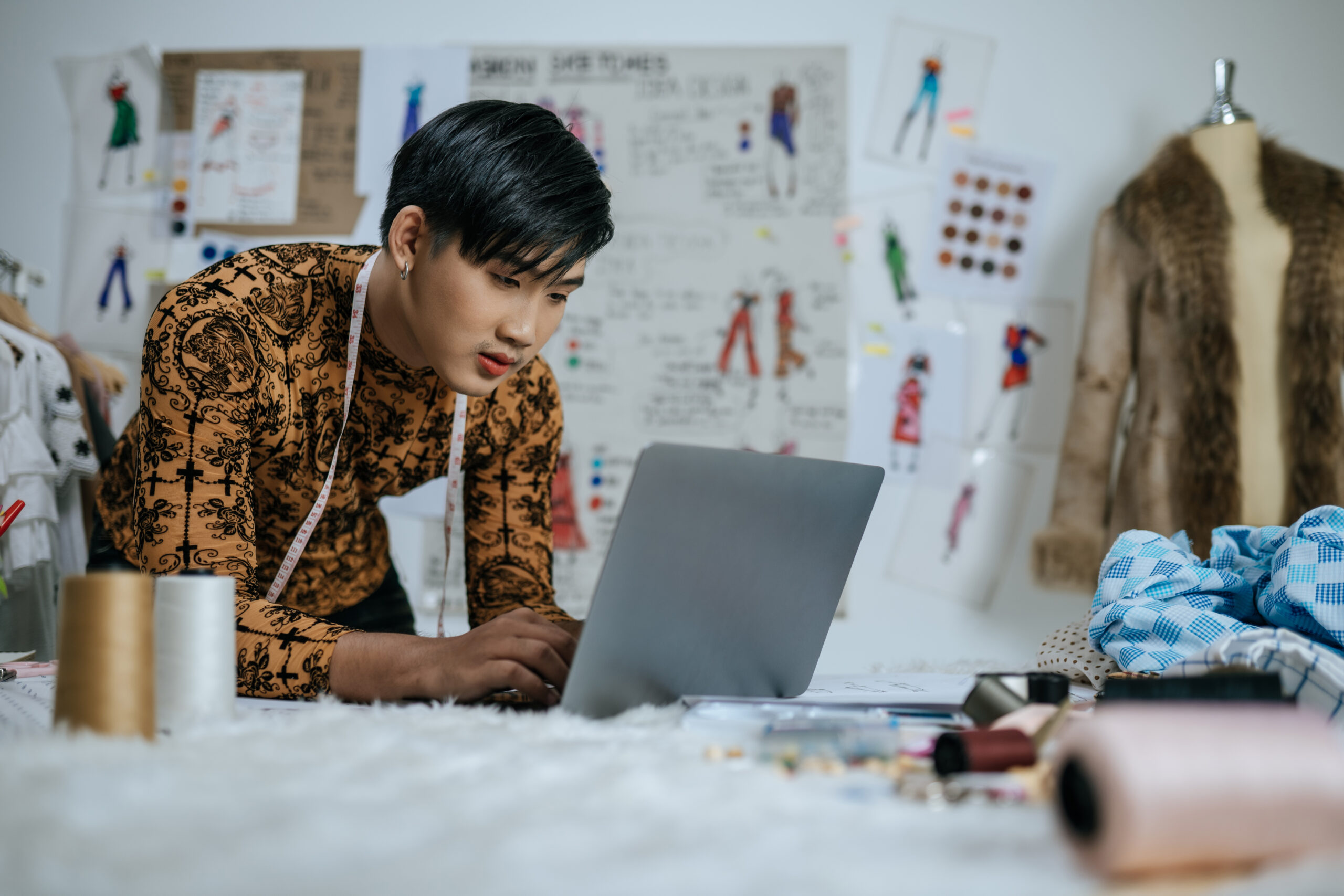
A 2024 study done by the International Textile Manufacturers Federation (ITMF) found a global skills shortage, driven by an aging workforce and a lack of younger talent entering the textile industry. This poses a difficult challenge as the apparel industry thrives on efficiency and innovation to meet the fast-paced demands of fashion trends and global supply chains.
To overcome this challenge many textile businesses have shifted their attention towards apparel software systems. Apparel management software systems have become indispensable for manufacturers, offering features to streamline operations and increase productivity.
This blog explores 6 keyways these systems revolutionize the way apparel businesses operate, ensuring sustainable growth and competitive advantage. Let’s begin!
6 Ways Apparel Software Systems Boost Productivity
As the apparel industry faces increasing challenges, from global skills shortages to dynamic market demands, adopting innovative solutions is no longer optional—it’s a necessity.
ERP for apparel are designed to address these challenges head-on by introducing smarter workflows and more efficient practices. By combining automation, real-time analytics, and streamlined operations, these systems help businesses adapt to modern manufacturing needs while staying ahead in a competitive market.
Let’s dive deeper into how apparel production management software boost productivity in six significant ways:
1] Enhancing Inventory Management:
Inventory management is a complex task in the apparel sector, requiring careful balancing to avoid overstocking or stockouts. Modern apparel software systems provide detailed insights into inventory levels, track stock movements, and set automatic reorder alerts.
Advanced apparel production management software also incorporates AI-based demand forecasting, enabling manufacturers to preemptively reorder materials and avoid costly stockouts. Furthermore, by setting automated reorder alerts and optimizing storage practices, businesses can reduce holding costs and ensure better cash flow management.
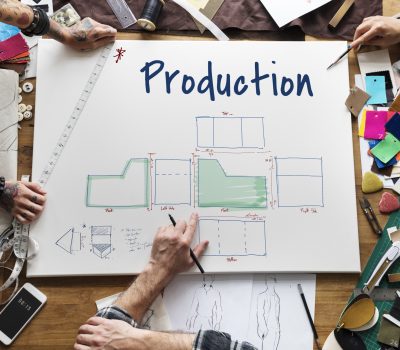
2]Streamlining Production Planning:
Apparel software systems enable textile manufacturers to optimize the entire production planning to forecast demand, schedule tasks, and allocate resources effectively. Advanced textile ERP solutions integrate real-time data, allowing for seamless adjustments to production schedules in response to market changes or supply chain disruptions.
This not only reduces delays but also optimizes resource utilization, minimizing waste and boosting productivity. Additionally, predictive analytics can help identify potential bottlenecks before they occur, ensuring continuous production and improved efficiency.
3] Improving Quality Control:
Maintaining consistent quality is essential in the apparel industry, where customer expectations are high, and product returns can damage profitability. Apparel software systems incorporate quality control features such as defect tracking, inspection checkpoints, and compliance management. For example, systems can flag defects during fabric cutting or stitching, enabling manufacturers to rectify issues immediately rather than after production is complete.
By automating quality assurance processes and providing real-time feedback, these textile ERP solutions help manufacturers identify and resolve issues early in the production cycle. This not only saves costs but also maintains the brand reputation by delivering high-quality products consistently.
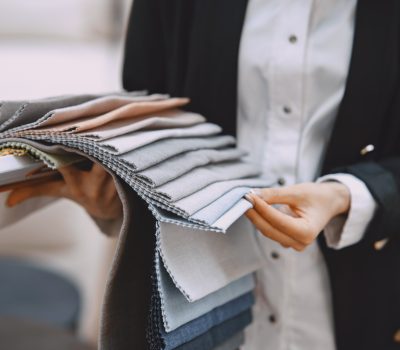
4] Optimizing Supply Chain Management:
The efficiency of an apparel manufacturer’s supply chain directly impacts production timelines and profitability. Apparel software systems provide an integrated platform to manage and monitor supply chain activities in real time. With features like vendor performance tracking, shipment tracking, and demand planning, manufacturers gain full visibility into their supply chain operations.
Advanced tools also help identify weak links, such as unreliable suppliers or delayed shipments, and suggest alternative solutions to mitigate risks. By aligning supply chain activities with production schedules, apparel management software reduces lead times, minimizes disruptions, and ensures smoother operations from start to finish.
5] Automating Routine Tasks:
Routine tasks often consume significant time and resources, leaving little room for strategic decision-making. Apparel software systems automate repetitive operations such as data entry, order processing, and financial reporting. Beyond saving time, automation ensures accuracy and consistency across workflows. For instance, a software system can automatically generate invoices based on completed orders, track payment statuses, and alert managers about pending dues.
Moreover, automated reporting tools offer actionable insights, empowering managers to make data-driven decisions faster. By reducing the burden of administrative tasks, businesses can redirect their workforce towards innovation and customer-focused initiatives.
6] Facilitating Collaboration and Communication:
In the apparel industry, seamless collaboration across teams such as design, production, and logistics is crucial for meeting tight deadlines and ensuring quality outcomes. Apparel software systems act as centralized platforms, breaking down silos and enabling real-time communication among departments. For example, design teams can upload patterns directly onto the platform for review by production teams, while managers can track progress through detailed dashboards.
Some apparel ERP systems also integrate with external communication tools to facilitate supplier collaboration. Improved information sharing and transparency not only enhances team productivity but also fosters a culture of accountability and innovation across the organization.
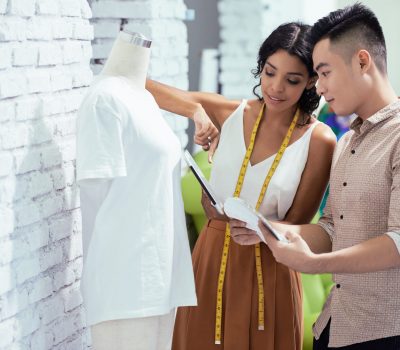
Apparel software systems are transformative tools for the industry, addressing challenges like inefficiency, quality issues, and supply chain complexities. By streamlining operations and fostering collaboration, these systems empower businesses to meet market demands while maintaining high standards of quality and sustainability. Investing in the right ERP for apparel is a step toward unlocking new levels of productivity and staying competitive in the ever-evolving apparel landscape.
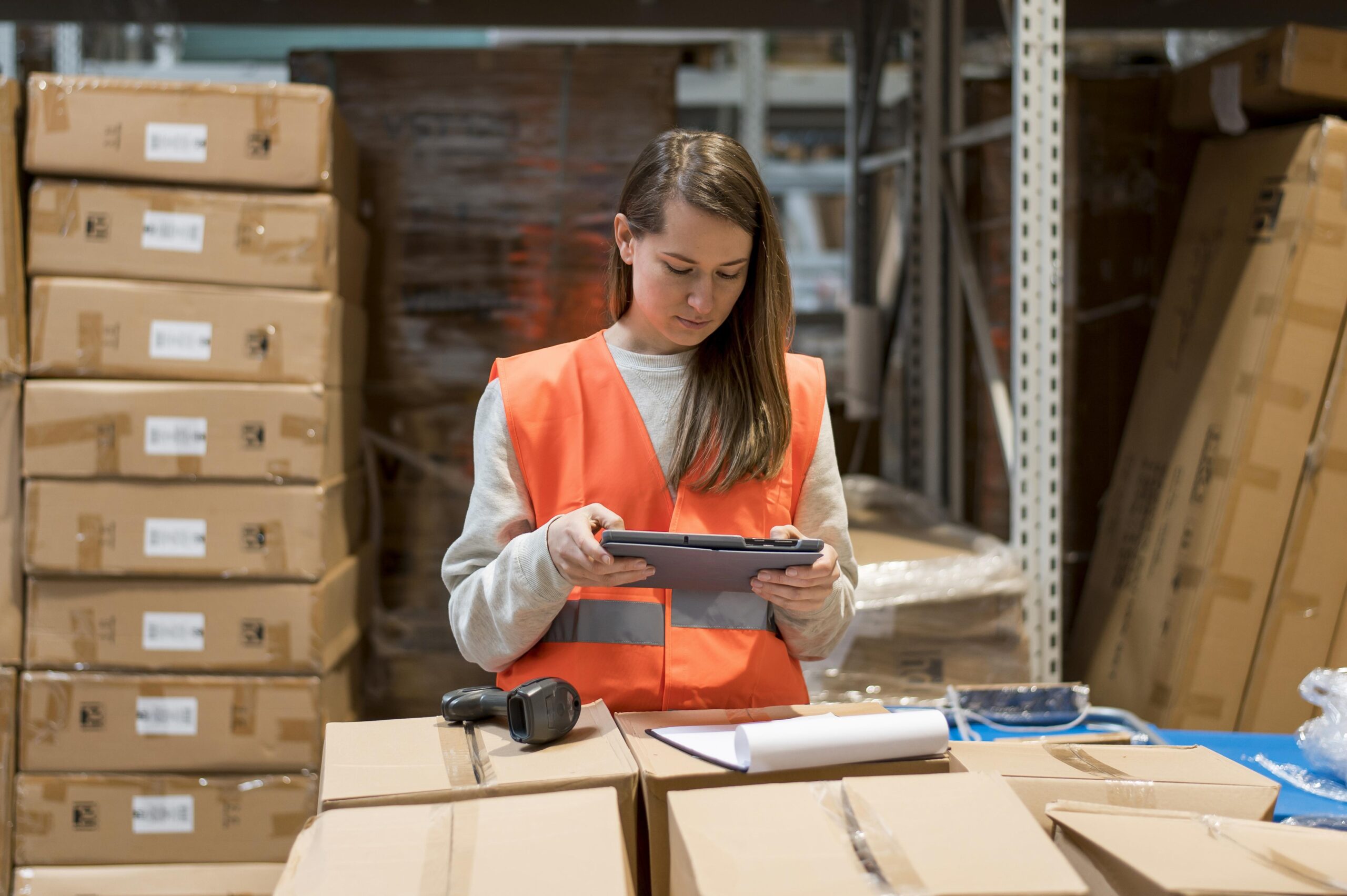
In the textile industry, effective inventory tracking is the backbone of smooth operations. With fluctuating consumer demands, a diverse range of SKUs, and tight production deadlines, staying on top of inventory is a complex yet vital task. Mismanaged inventory can lead to issues such as overstocking, stockouts, production delays, or increased costs, all of which can impact a manufacturer’s bottom line.
For textile manufacturers – market competition is fierce, and customer expectations are high. Therefore, implementing robust inventory management practices is essential. It minimizes waste and optimizes storage space while ensuring timely deliveries and better resource utilization.
In this blog, we’ll explore five best practices for textile inventory tracking. These strategies are designed to help textile manufacturers streamline operations, reduce errors, and enhance overall efficiency in an increasingly demanding market.
5 Best Practices for Textile Inventory Tracking with ERP
Enterprise Resource Planning (ERP) systems have transformed how textile businesses manage inventory. By centralizing data, automating workflows, and delivering real-time insights into fabric stock management, ERP solutions have become indispensable for modern textile manufacturers.
However, to fully capitalize on these benefits, certain best practices must be integrated into the inventory tracking process. Let’s explore five key practices that can help your textile business stay competitive and efficient.
1] Implement Real-Time Tracking Systems:
Real-time inventory tracking is a game-changer for the textile industry, where the pace of operations demands precision and agility. Knowing the exact location and status of raw materials, work-in-progress items, and finished goods at any given moment is critical.
Textile inventory software help textile manufacturers ensure inventory levels are always accurate, preventing costly overstocking or shortages. These systems reduce errors, enhance operational transparency, and facilitate faster decision-making, especially during peak production cycles.
Additionally, real-time tracking fosters better collaboration between departments by ensuring everyone accesses the same up-to-date data. This minimizes miscommunication, streamlines workflows, and improves overall operational efficiency during complex production runs.
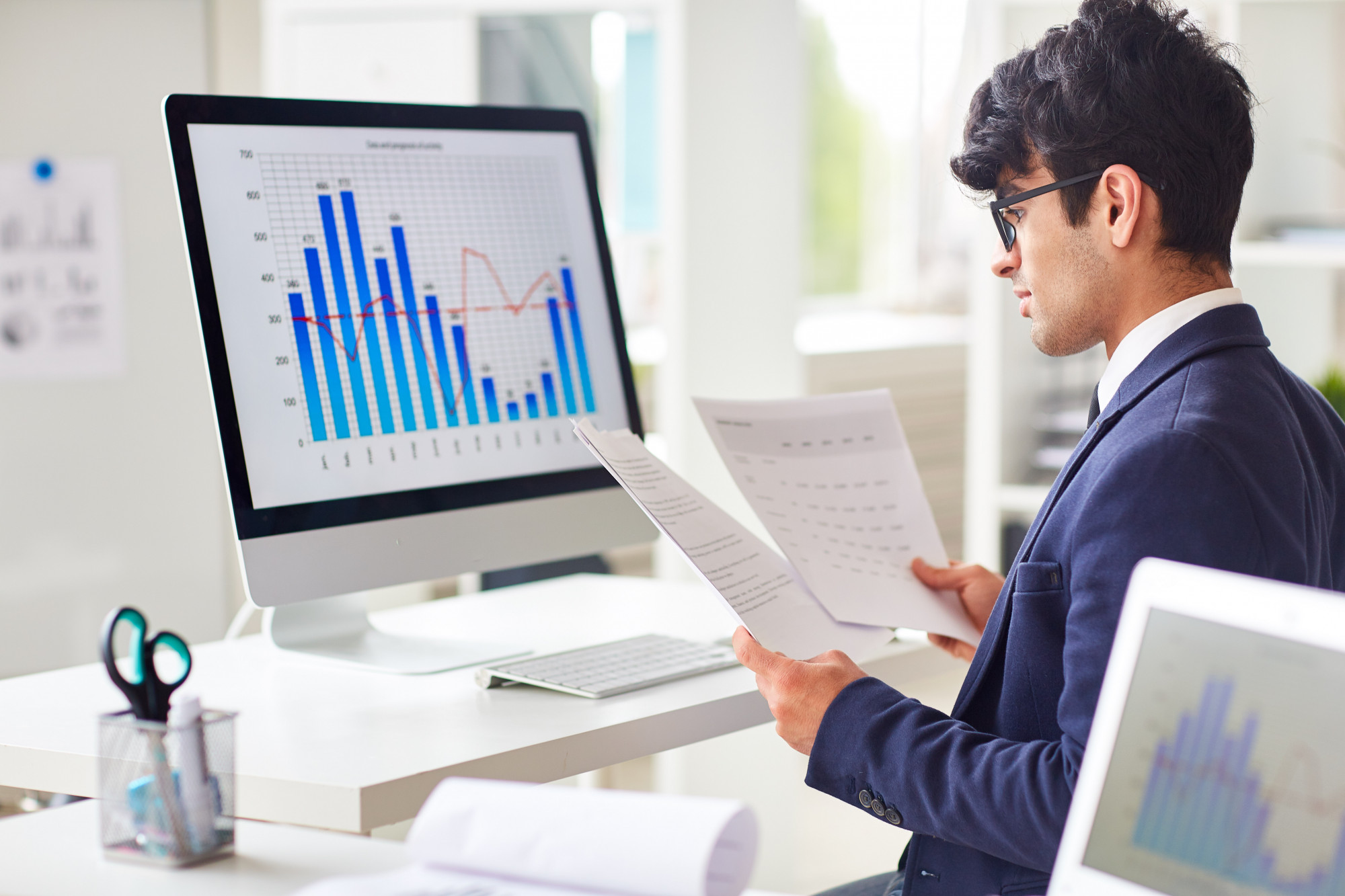
2] Classify and Prioritize Inventory:
Different inventory holds different value inside a textile business. Segmenting inventory into categories such as raw materials, in-process goods, and finished products allows businesses to prioritize resources effectively.
For instance, raw materials needed for high-priority orders can be closely monitored to avoid delays. ERP for textile simplifies this process by automating inventory categorization and prioritization. This ensures that essential items are always available when needed, reducing production delays and improving resource allocation.
Moreover, proper classification streamlines inventory audits and enhances demand forecasting, enabling businesses to respond swiftly to urgent requirements. By classifying and prioritizing inventory, textile manufacturers can maintain better control over stock levels, reduce costs, and improve production timelines.
3] Leverage AI Forecasting Tools:
Inventory mismanagement often results from inaccurate demand forecasting. Using textile ERP system with AI forecasting capabilities enables businesses to predict demand trends based on historical data and market analysis.
For example, an ERP for textile like iTexClouds can analyze seasonal trends, order history, and market demand to generate accurate forecasts. This helps prevent overproduction and understocking, reducing waste while ensuring timely delivery. Forecasting also ensures that you stay prepared for sudden demand surges or shifts.
AI-powered tools also identify slow-moving inventory and recommend strategies to optimize stock levels. With these insights, textile businesses can refine procurement plans, reduce holding costs, and maintain a balanced inventory flow, ultimately boosting operational efficiency.
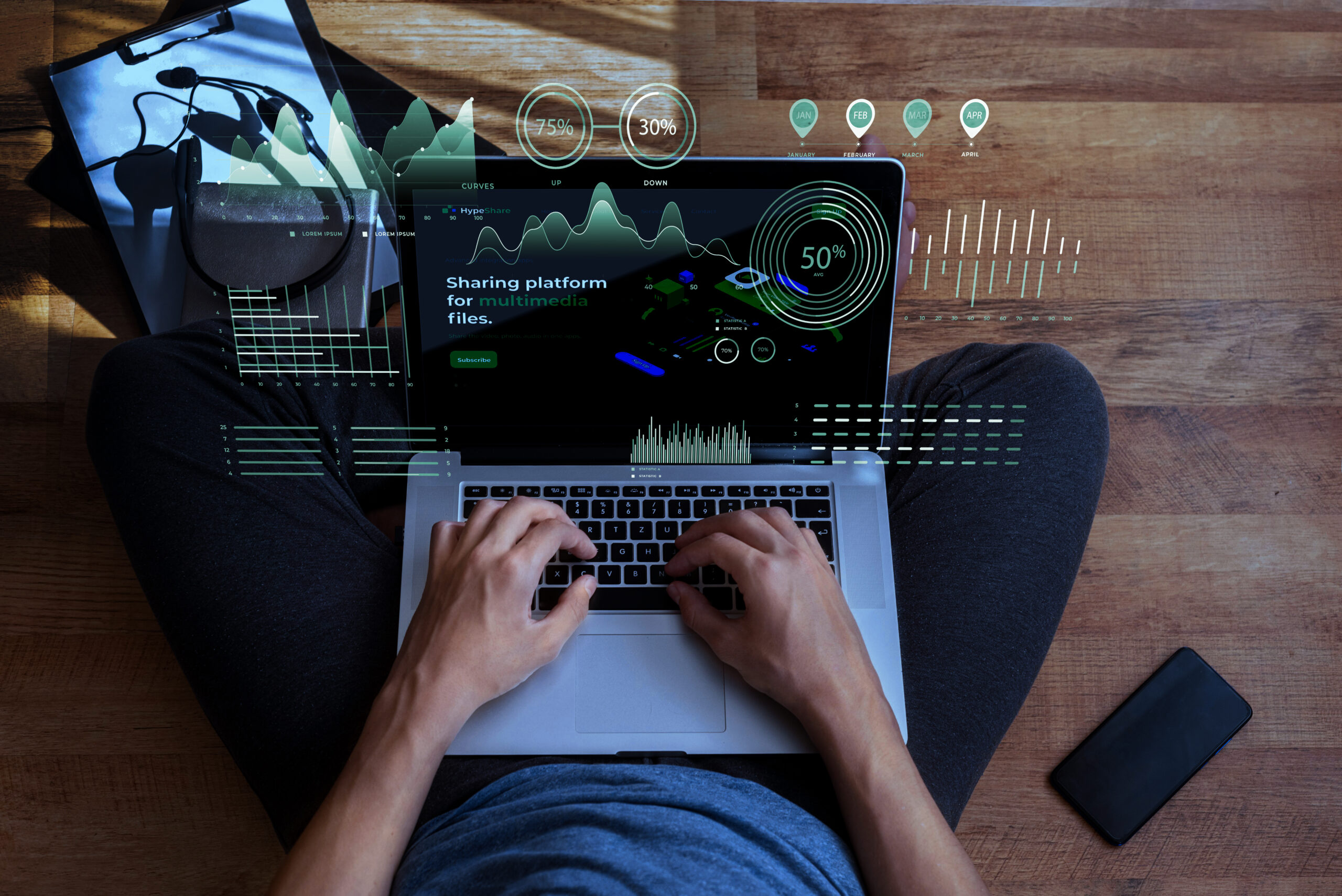
4] Optimize Warehouse Management:
An organized warehouse is the backbone of effective textile inventory tracking. Disorganized warehouses lead to misplaced items, delays in locating stock, and higher operational costs.
Using a textile ERP system which comes equipped with a warehouse management module easily streamlines storage processes. Features such as barcode scanning, automated stock updates, and space optimization insights ensure accurate inventory data and reduce retrieval times.
For textile manufacturers and distributors, especially those managing bulky or fragile materials, these tools improve storage utilization and workflow efficiency. By leveraging ERP-powered warehouse management, businesses can minimize errors, reduce handling time, and enhance overall productivity.
5]Ensure Regular Audits and Reporting:
Even the most advanced systems need regular audits to identify discrepancies. Periodic inventory audits ensure that stock levels recorded in the system match actual quantities.
ERP or a textile inventory software simplifies this process by offering automated reporting tools. By generating real-time inventory reports, textile businesses can quickly identify inconsistencies, track aging stock, and plan corrective actions. Regular audits also maintain compliance with industry regulations, improving your brand’s reputation.
These audits also provide valuable insights into inventory turnover and slow-moving products. With the data from regular audits, businesses can better forecast demand, optimize stock levels, and improve overall supply chain efficiency. This proactive approach reduces the chances of stockouts and overstock situations, allowing textile companies to maintain smoother operations and increase profitability.
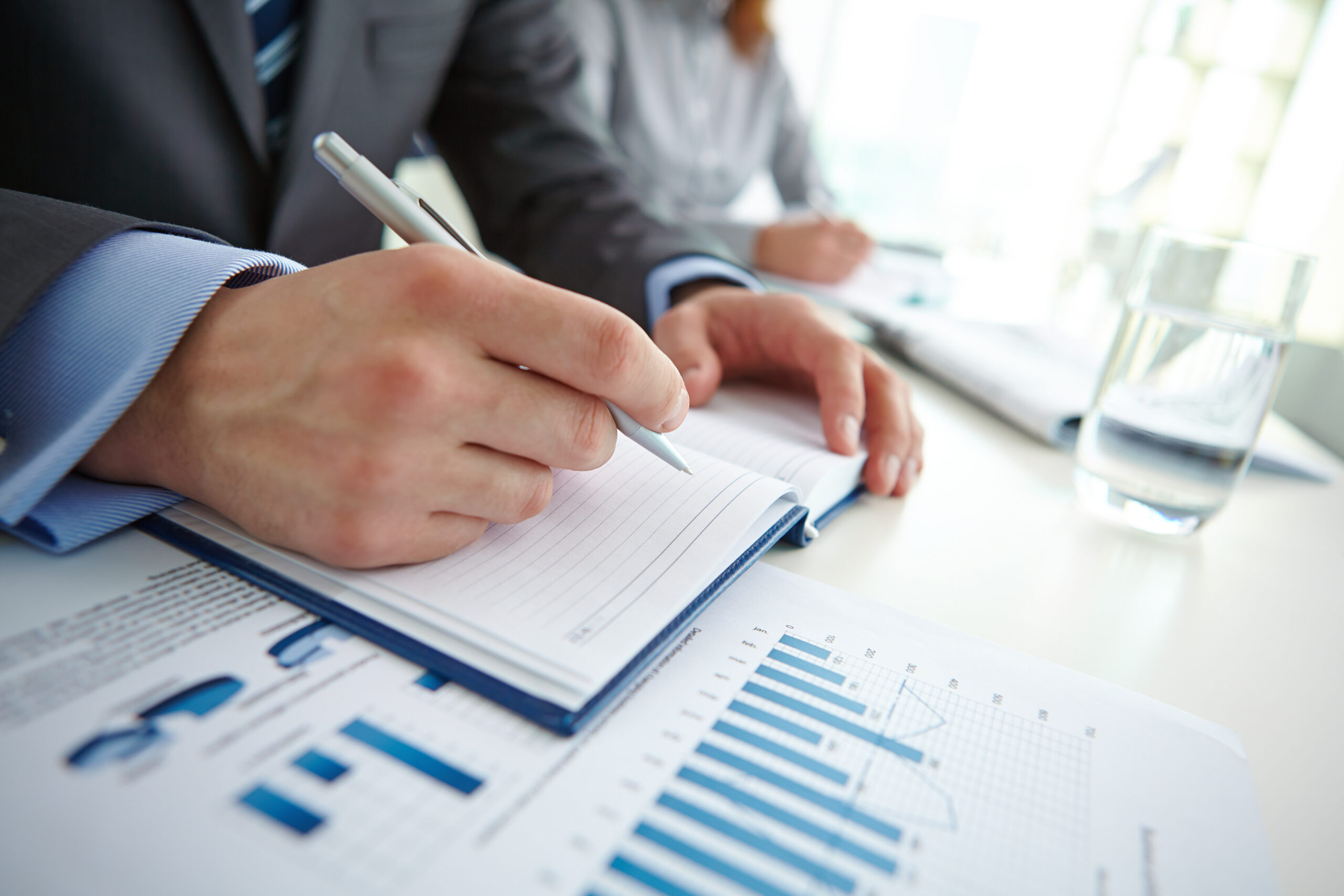
Textile inventory tracking is more than just a routine task—it’s a strategic advantage. By implementing practices like real-time tracking, inventory categorization, demand forecasting, optimized warehouse management, and regular audits, you can significantly improve efficiency.
In 2025, as competition grows, adopting advanced solutions like a textile ERP system will be essential for staying ahead in the textile industry. These practices will not only streamline your operations but also contribute to a sustainable, customer-focused supply chain.

7 Benefits of ERP for Textile Distributors
To understand the benefits of an ERP system, it’s essential to recognize its purpose. ERP for textile distribution is designed to simplify, automate, and optimize every step of the textile distribution process—from inventory management to customer service.By addressing industry-specific challenges, these systems provide the tools distributors need to stay efficient, reduce costs, and meet market demands. Let’s explore seven key benefits that ERP software brings to textile distributors:1] Enhanced Inventory Management: Textile distributors handle diverse inventories, including raw materials, semi-finished goods, and finished products. ERP for textile distribution provides a centralized platform to monitor stock levels, track inventory movements, and prevent overstocking or stockouts.With real-time inventory tracking, distributors can optimize storage, reduce wastage, and maintain a balanced stock supply. This not only minimizes costs but also ensures that the right products are available at the right time, improving operational efficiency and customer satisfaction.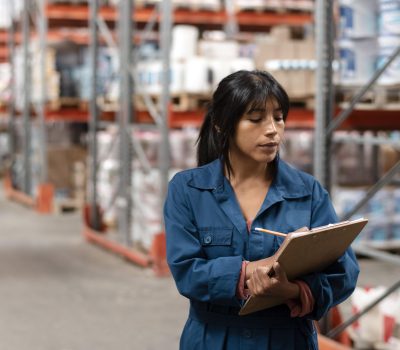
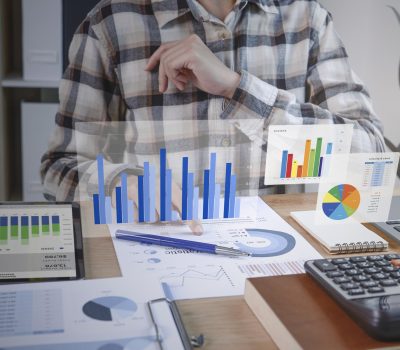
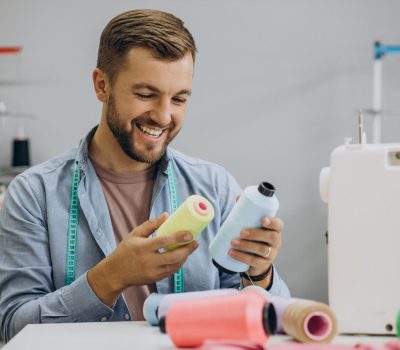
Why ERP is Essential for Textile Distribution?
For textile distributors looking to boost efficiency, reduce costs, and enhance service quality, ERP systems are no longer optional—they’re a necessity. ERP systems address common pain points like fragmented workflows, delayed processes, and lack of visibility, offering solutions tailored to industry-specific needs.- Centralized Data Management: ERP systems integrate data across departments, eliminating silos and ensuring that everyone works with accurate, real-time information. This improves collaboration and reduces errors caused by disconnected systems.
- Automation of Repetitive Tasks: Routine processes like order entry, invoicing, and inventory updates are automated, saving time and allowing employees to focus on more strategic activities.
- Seamless Integration with Vendors: ERP solutions improve communication and collaboration with suppliers, enabling better coordination in sourcing, lead times, and pricing negotiations.
- Real-Time Reporting and Analytics: Distributors gain access to actionable insights with dashboards and reports, helping them identify opportunities, monitor performance, and make data-driven decisions to improve operations.
- Customer-Centric Approach: By providing tools for personalized customer interactions, faster response times, and better service delivery, ERP systems help build stronger, long-lasting relationships with clients.
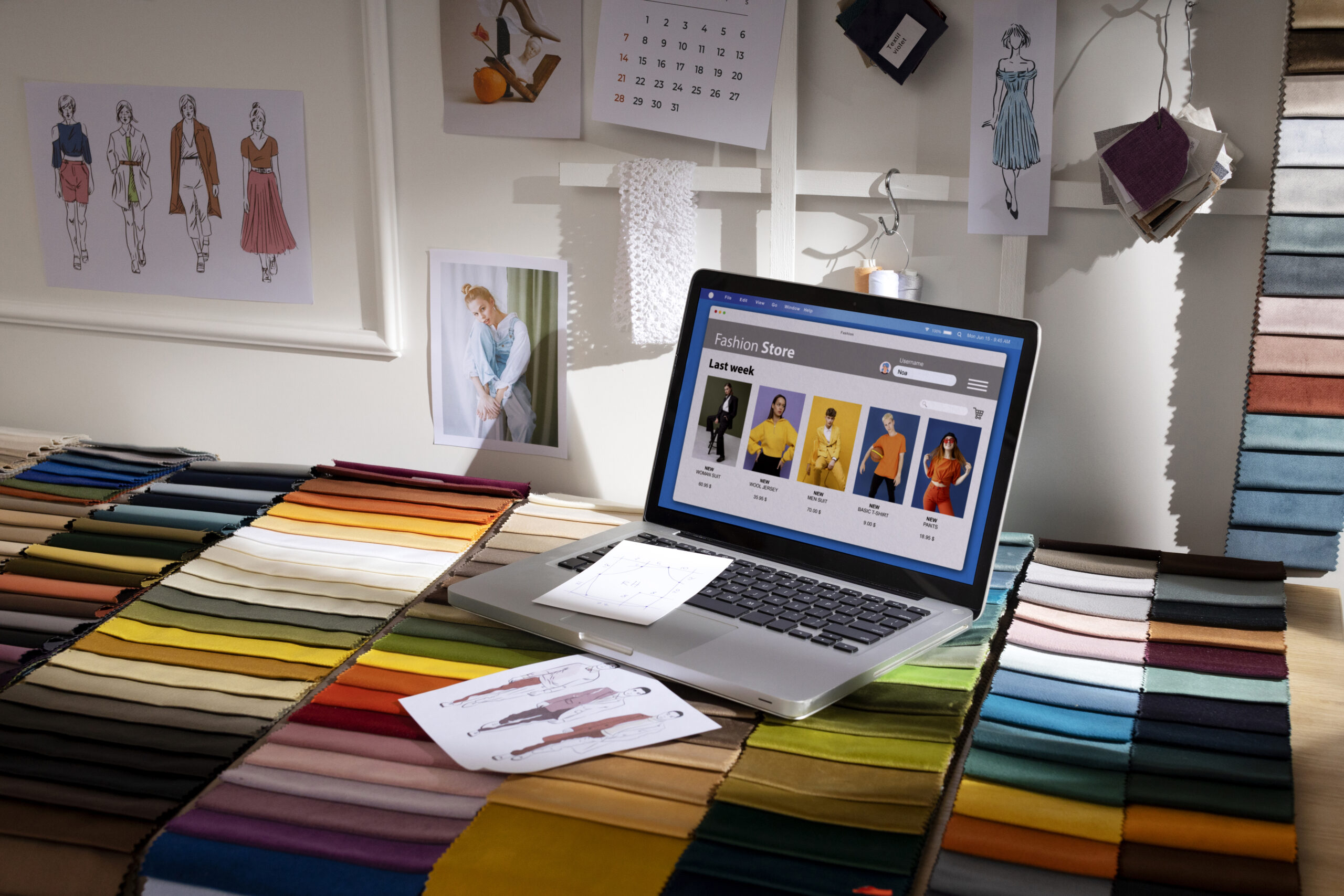
As we approach 2025, the textile industry continues to face heightened competition and rapidly changing consumer trends. To stay ahead, leading textile companies are adopting various software solutions to optimize operations and secure their competitive edge. However, choosing the right tools remains a complex decision with many variables to consider.
Software solutions such as ERP, CRM, CMMS, and design tools empower textile businesses to stay agile and competitive. These systems enhance efficiency, improve customer relationships, and ensure sustainable production processes. Even simple yet versatile tools like Microsoft Excel continue to play a critical role for smaller enterprises.
Below, we explore five must-have software solutions that can help textile businesses thrive in 2025’s dynamic and demanding market.
1] Enterprise Resource Planning (ERP):
ERP software has become indispensable for modern textile businesses, particularly as they navigate increasing complexities in 2025. ERP software for textile industry specializes in handling and integrating all core functions of a textile business like inventory, production, and financial management through dedicated modules.
By automating repetitive tasks such as order processing and inventory updates, textile ERP solutions significantly reduce human error. They also provide actionable insights through advanced analytics and AI-driven forecasting tools, helping businesses anticipate demand, optimize production schedules, and control costs.
Another critical advantage of ERP for textile manufacturers & distributors is its role in supporting compliance with sustainability initiatives. These systems can track raw material usage, monitor waste, and analyze energy consumption, helping businesses align with global environmental standards and achieve their sustainability goals.
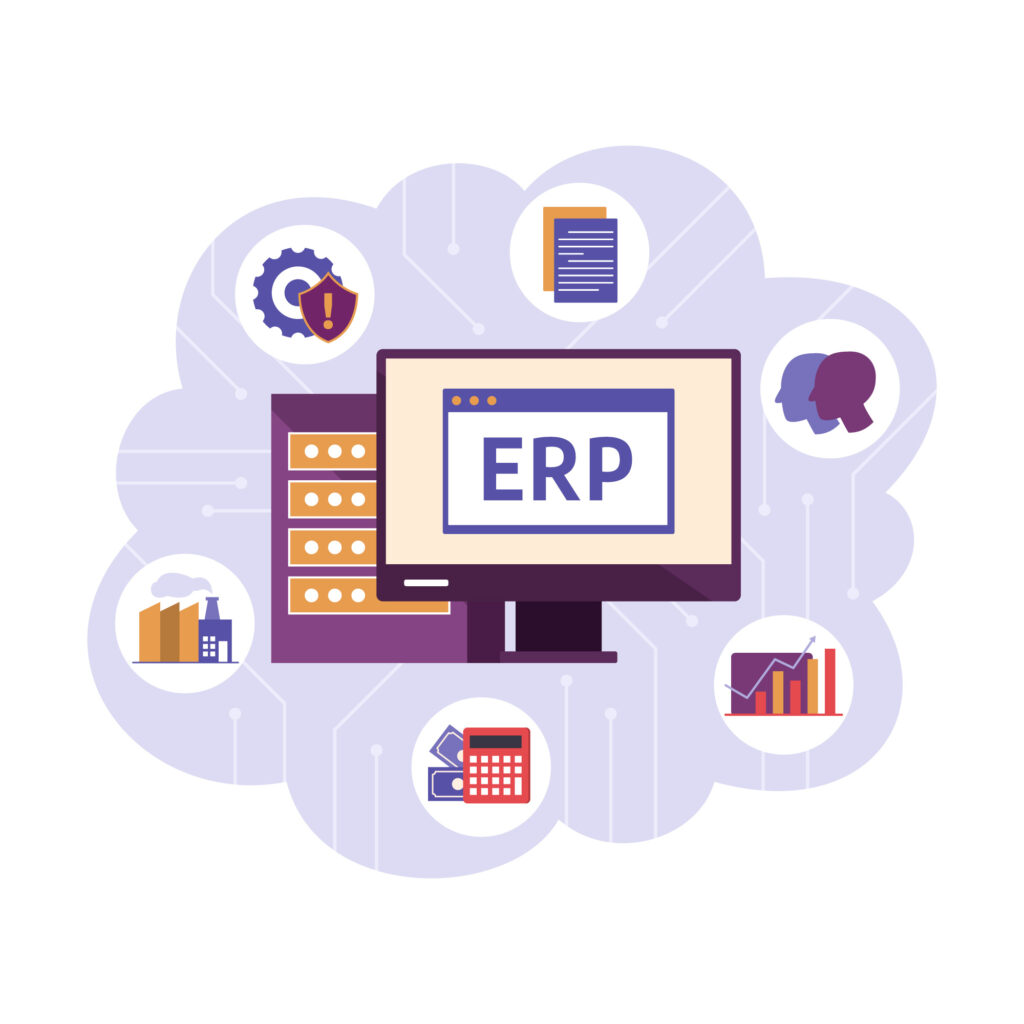

2] Customer Relationship Management (CRM):
A CRM software system enables textile manufacturers and distributors to build and nurture strong customer relationships by centralizing data and automating customer interactions. It tracks essential data like communications, purchasing trends, and sales activities, offering a complete view of customer behavior.
With the textile market becoming increasingly competitive and customer-centric, CRM software is vital for managing the complexities of modern customer relationships. It enables businesses to personalize marketing campaigns, identify cross-selling or upselling opportunities, and streamline sales workflows.
Moreover, CRM tools empower sales teams with real-time data to make informed decisions, predict market trends, and foster long-term customer loyalty. By integrating with ERP systems, textile businesses can ensure a seamless flow of customer data across departments, further enhancing customer experiences and driving revenue growth.
3] Computerized Maintenance Management System (CMMS):
A CMMS software system is crucial for textile businesses to ensure smooth operations by automating maintenance schedules, tracking work orders, and monitoring the performance of critical machinery.
Unplanned downtime can cause significant disruptions in production, especially in the fast-paced textile sector. By using CMMS textile software, manufacturers can proactively manage equipment maintenance, detect potential failures before they occur, and schedule repairs without interrupting production. This leads to reduced downtime, extended asset life, and lower repair costs.
In 2025, the increasing reliance on automation and precision machinery in the textile industry will make CMMS software an essential tool. Additionally, CMMS solutions can track maintenance metrics and safety compliance, ensuring manufacturers meet industry regulations while maximizing resource efficiency and production uptime.
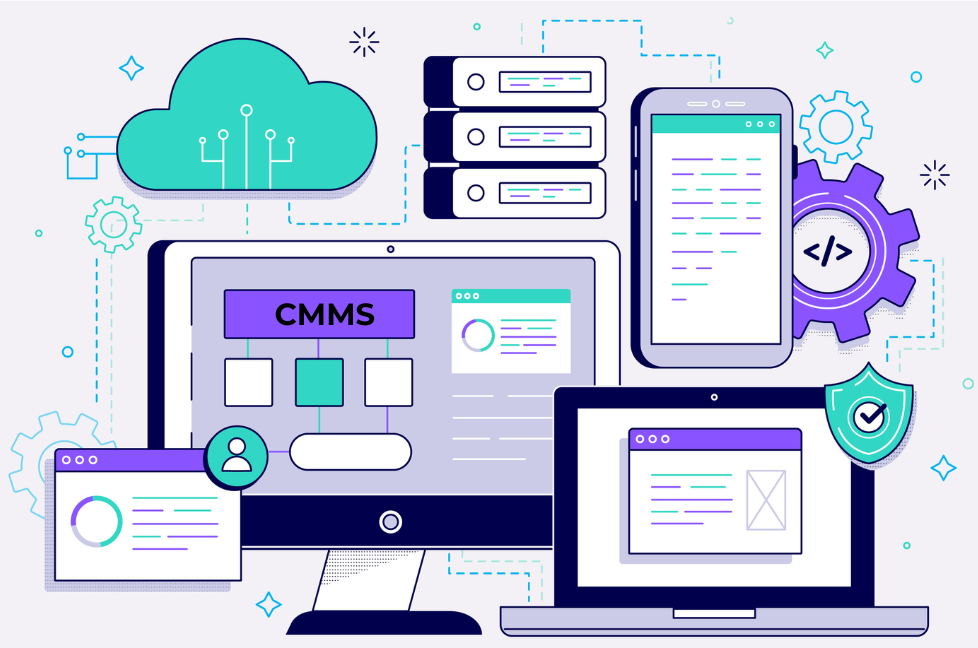
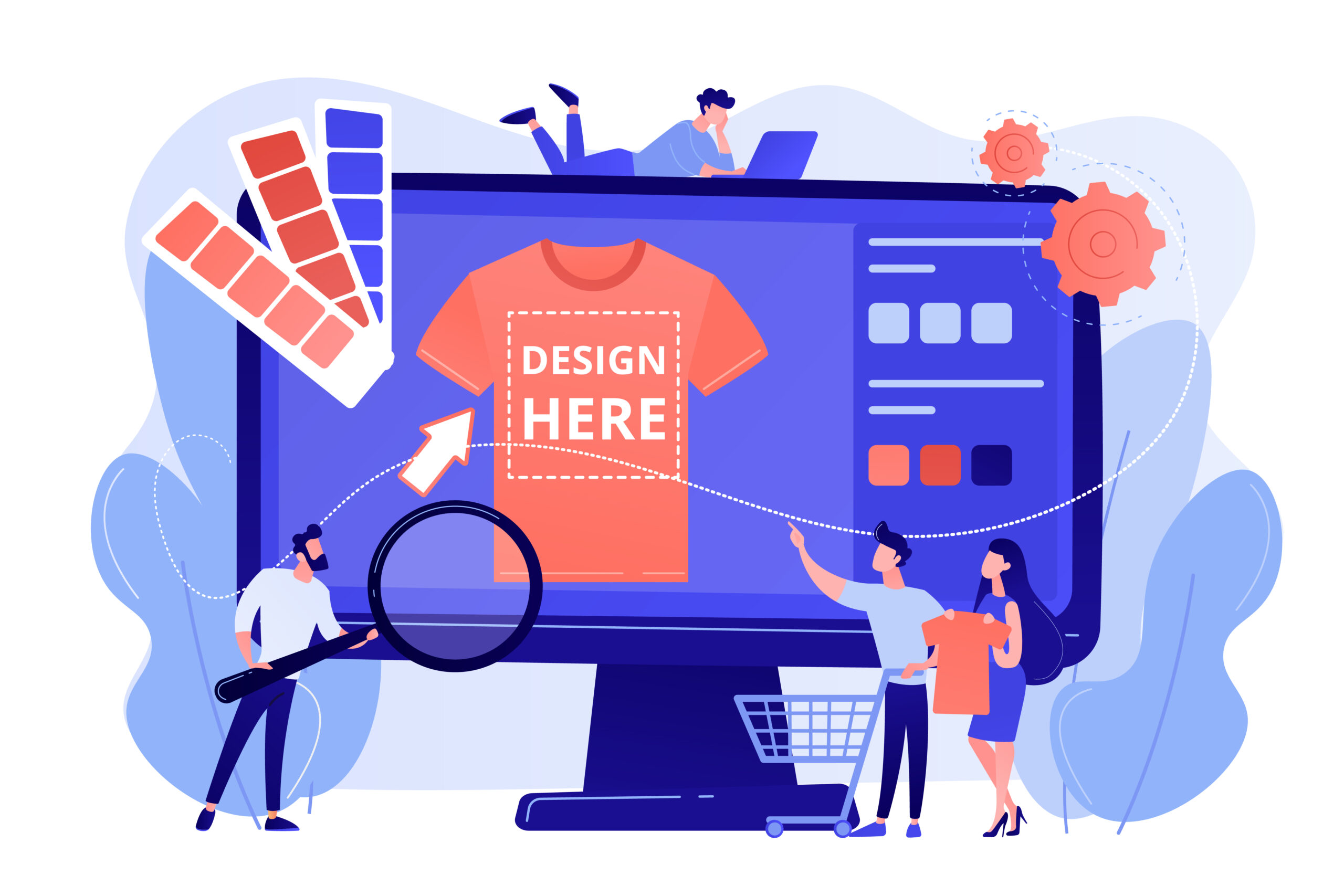
4] Design Software :
Textile design software provides tools to create digital fabric patterns, color schemes, and prototypes, empowering businesses to innovate quickly and meet market demands.
By reducing reliance on physical samples, design software significantly accelerates the design-to-production process, improving speed to market and minimizing waste. With features like AI-assisted pattern generation, fabric rendering, and virtual try-ons, textile designers can experiment with multiple iterations efficiently, ensuring accuracy and creativity.
As fashion trends evolve at lightning speed, 2025 will demand even greater agility in design workflows. Advanced textile design tools will enable businesses to cater to niche markets, create personalized designs, and produce market-ready collections faster than ever. For companies that prioritize innovation, these tools are game-changers in meeting consumer demands while staying cost-effective.
5]Microsoft Excel:
While Excel lacks the automation capabilities of specialized textile software like ERP or CRM, it remains indispensable for small to mid-sized textile businesses due to its adaptability and cost-effectiveness.
Excel offers robust features for managing budgets, monitoring financial performance, and tracking inventory levels with precision. Businesses can use pivot tables, customized formulas, and charts to analyze trends, forecast demand, and make informed decisions.
For businesses that cannot invest in expensive software, Excel’s advanced capabilities like macros and VBA scripting allow automation of repetitive tasks, saving time and reducing errors. From cost analysis to production planning, Excel provides the flexibility and simplicity needed for smaller enterprises to stay competitive.
In 2025, Excel will continue to play a foundational role in bridging gaps for businesses transitioning to more comprehensive software solutions, making it a reliable tool for those on a budget.

Why Choose the Right Textile Software Solution?
Selecting the right textile software solutions is essential for optimizing operations and staying ahead in a competitive industry. Here are the 5 main reasons to invest in the right textile software solution:
- Tackle Supply Chain Complexities: Specialized tools like ERP systems help manage procurement, inventory, and logistics, ensuring smoother operations and fewer disruptions.
- Enhance Customer Relationships: CRM software enables better communication, personalized service, and customer satisfaction through efficient data tracking.
- Streamline Machinery Maintenance: Tools like CMMS reduce equipment downtime, extend machinery lifespan, and minimize repair costs with automated schedules.
- Accelerate Design Processes: Textile design software simplifies creating patterns, prototypes, and color schemes, enabling faster product launches.
- Boost Decision-Making: Integrated solutions provide real-time insights for strategic planning and efficient resource allocation.
In 2025, adopting textile software is essential for staying competitive in a dynamic industry. Tools like ERP, CRM, CMMS, design software, and Excel empower businesses to streamline operations, enhance customer relationships, and adapt to shifting market demands. These solutions enable real-time decision-making, boost efficiency, and reduce operational bottlenecks.
By integrating advanced technologies, textile businesses can optimize resources, meet sustainability goals, and drive growth, positioning themselves for success in an increasingly challenging and fast-paced market environment.
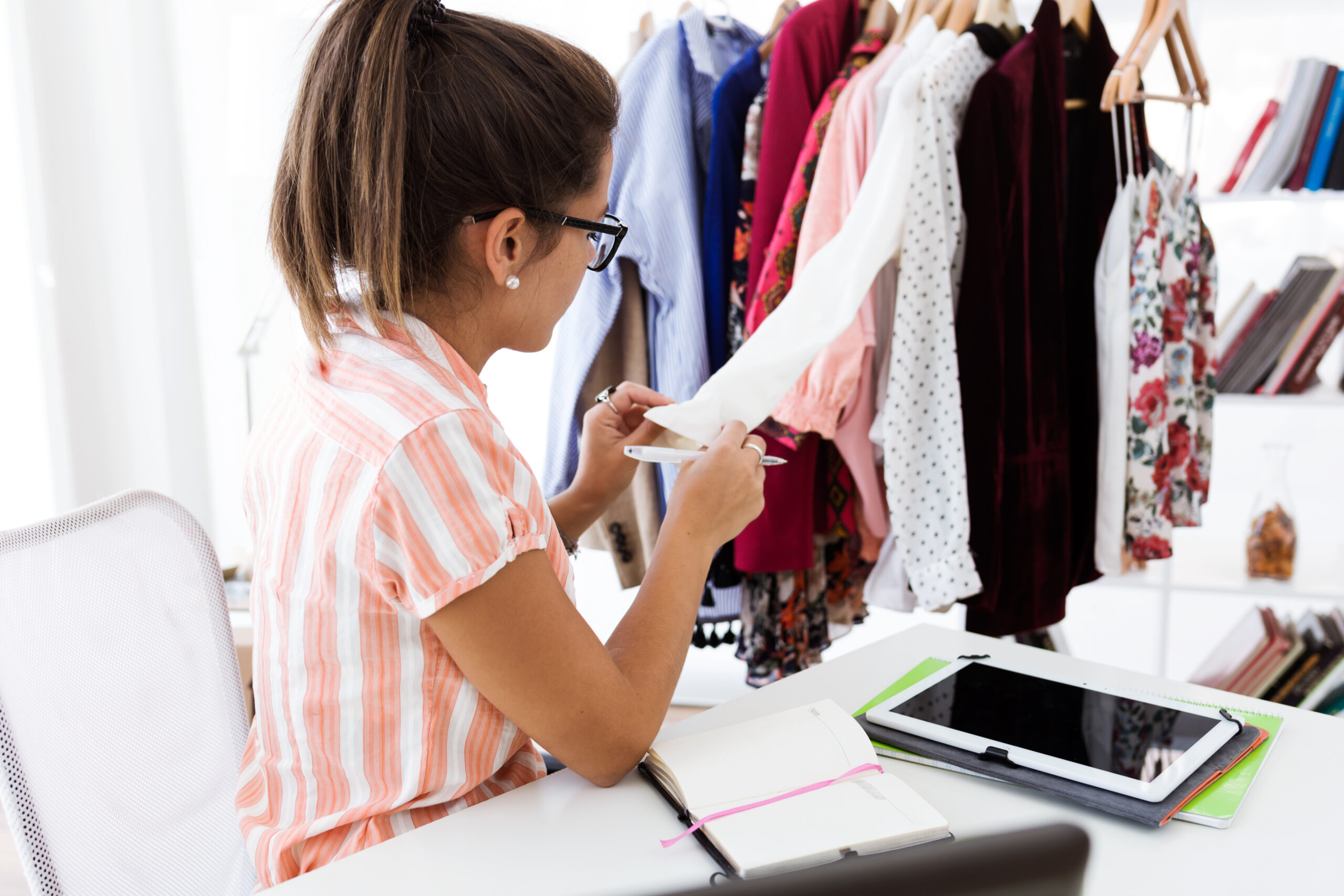
The apparel industry is facing increasing demands for speed, sustainability, and efficiency resulting in a more urgent need for robust management solutions.
In 2025, ERP for apparel management will continue to revolutionize how businesses manage production, inventory, and customer relationships. These systems not only streamline operations but also provide real-time insights and scalability to adapt to market shifts.
In this blog, we’ll highlight 8 key reasons why adopting an apparel industry ERP is essential for staying competitive and driving success in a rapidly evolving industry.
8 Reasons to Use Apparel Management ERP Software in 2025
An apparel production ERP is designed to meet the growing demands of the industry by offering a wide range of benefits. From enhancing efficiency in production to improving decision-making, here are eight key reasons why adopting this technology can transform your garment manufacturing operations:
1] Global Supply Chain Disruptions:
An efficient apparel production line significantly depends on a streamlined supply chain. However, challenges like supplier inconsistencies, geopolitical tensions, pandemics, natural disasters disrupt global supply chains in the textile industry. This makes it difficult for manufacturers to maintain steady production schedules and ensure that materials arrive on time.
Apparel management ERP software help mitigate these issues by offering real-time tracking of raw materials, inventory, and shipments. They allow businesses to quickly identify supply chain bottlenecks, prevent inventory stockouts, predict purchase requirements, etc. As a result, manufacturers can communicate with suppliers more effectively and stay a step ahead of possible supply chain disruptions.
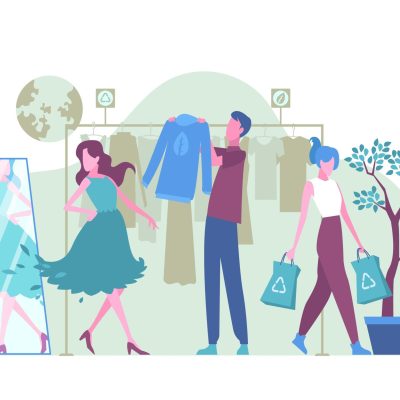
2] Evolving Fashion Trends and Shorter Product Life Cycles:
Fashion trends today are faster than ever, with consumer expectations demanding rapid turnarounds for new styles. This creates pressure on apparel manufacturers to stay agile and respond quickly to market demands.
Apparel management ERP software plays a key role by integrating product development, design, and production schedules into one cohesive system. This allows manufacturers to monitor trend data, align production with market timing, and avoid delays. With better planning and resource allocation, ERP for garment manufacturing help businesses stay competitive by quickly adapting to fashion cycles and reducing time-to-market for new products.
3] Inventory Mismanagement:
Inventory management is often one of the most challenging aspects of the apparel industry. Without accurate, real-time data, businesses risk overstocking certain items while running out of others, leading to costly production delays or missed sales opportunities.
Apparel management ERP software provide a centralized, real-time view of inventory levels, ensuring that businesses can monitor stock across multiple locations and manage reordering more efficiently. By automating this process, ERP helps maintain a balanced inventory that aligns with demand, reducing waste and optimizing working capital.
4] Compliance with ESG Standards : As sustainability becomes a top priority for both consumers and regulators, meeting Environmental, Social, and Governance (ESG) standards has never been more crucial. From sourcing raw materials to labor practices, companies are under increasing pressure to ensure that their operations align with ethical and sustainable practices.
Apparel management ERP software help by tracking key sustainability metrics, including resource usage, waste management, and supplier compliance. They also generate detailed reports to ensure businesses meet industry standards and provide transparency to consumers, helping companies stay ahead in an increasingly eco-conscious market.
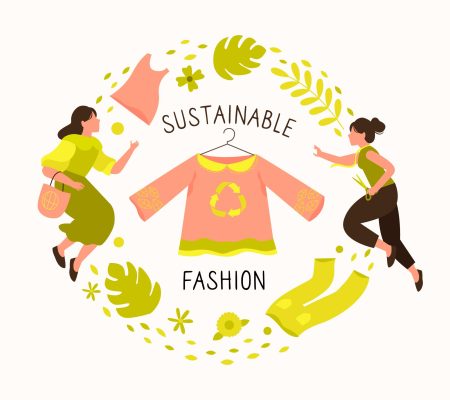
5] Labor Shortages:
The shortage of skilled labor is a significant issue facing the textile industry, particularly in regions like the US. The demand for experienced workers is high, but the supply is low, leading to inefficiencies and delays in production.
ERP for apparel help address this challenge by automating many routine tasks, such as order entry, production scheduling, and inventory management. This reduces the reliance on manual labor and allows existing staff to focus on more critical, value-adding activities.
Moreover, Apparel management ERP software improve workforce management by tracking employee performance and optimizing labor allocation, helping businesses operate more efficiently with fewer resources.
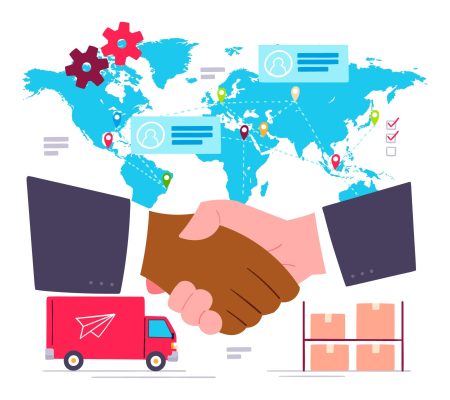
6] Complex Supplier Relationships: Managing a network of suppliers, especially in a globalized market, is a daunting task for apparel manufacturers. Variations in lead times, pricing, and communication can lead to inefficiencies and delays, disrupting the production schedule.
Apparel management ERP software centralize supplier information and streamline procurement processes, providing businesses with a comprehensive view of supplier performance. By automating purchase orders and tracking supplier performance metrics, ERP helps ensure timely deliveries, better negotiation terms, and consistent quality. This reduces the complexities of managing multiple suppliers and fosters stronger, more reliable supplier relationships.
7] Fluctuating Raw Material Costs: The global textile industry is heavily impacted by fluctuations in raw material prices, such as cotton, polyester, and dyes. These price variations can significantly affect profit margins and make financial planning more challenging.
Apparel industry software provide businesses with better visibility into cost trends, helping them forecast material needs and adjust production plans accordingly. They also allow manufacturers to monitor and control procurement processes in real-time, ensuring that material purchases align with market conditions and budget constraints. This agility helps companies mitigate the impact of price fluctuations and better protect their profit margins.
8] Multiple Custom Orders: As consumer demand for personalized products grows, managing custom orders has become increasingly challenging for apparel manufacturers. Each custom order requires detailed specifications, from size and fabric choices to design details, making tracking and production more complex.
ERP for apparel help by consolidating all customer specifications in a single, organized system. This ensures accurate order fulfilment and eliminates manual errors, making it easier to manage large volumes of custom orders. By automating the order entry process and integrating it with production scheduling, ERP ensures that custom orders are delivered on time, maintaining customer satisfaction and reducing production bottlenecks.

Adopting an apparel management ERP software in 2025 is essential for staying competitive in the fast-paced textile industry. From overcoming global supply chain disruptions to managing custom orders, ERP systems offer significant advantages, enabling businesses to streamline operations, reduce costs, and improve efficiency.
As the industry continues to evolve, apparel production ERP systems will be the cornerstone of sustainable growth and success. By addressing key challenges such as inventory mismanagement, labor shortages, and fluctuating material costs, ERP systems ensure that textile manufacturers remain agile and responsive in the face of change.
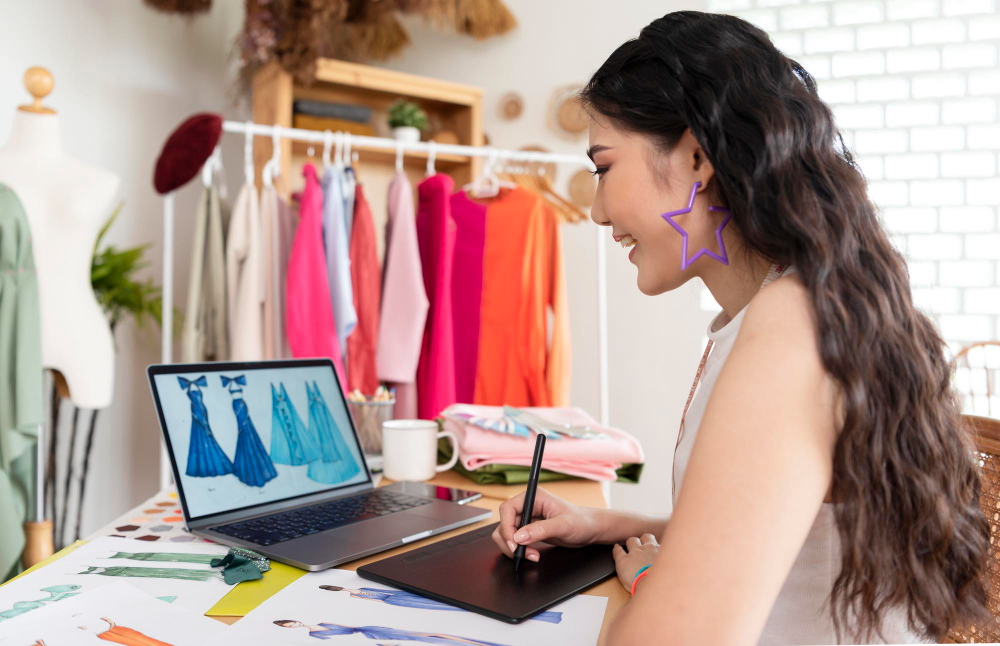
The apparel industry is complex with numerous interconnected processes, including production planning, inventory management, sales tracking, and supply chain coordination. Efficiently managing these operations is crucial and with the right tools, like a tailored apparel management software businesses can streamline workflows, cut costs, and boost overall productivity by as much as 20–30%.
By integrating key functions such as order processing, inventory tracking, and customer management, an apparel software provides real-time data and automation. As a result, apparel companies can respond faster to market demands, improve their decision-making, and maintain a competitive edge.
In this blog, we’ll explore the top 10 ways ERP for apparel how the best apparel software can transform day-to-day operations for business owners allowing them to stay ahead in the competitive market.
10 Ways Apparel Management Software Transforms Operations
Apparel management in the textile Industry involves a lot of operations and procedures. To maintain the quality and efficiency of all these processes on a larger scale, adopting apparel management solutions is must.
An apparel management software’s main function is to increase the visibility, efficiency, quality, and accuracy of all the operations in the whole production chain. So, let’s look at the top 10 ways the best apparel management software transforms all these operations:
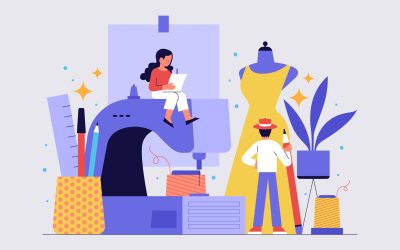
1] AI-Driven Production Planning: The production process in the apparel industry involves intricate planning, from fabric procurement to stitching and final assembly. Apparel management software with AI capabilities automates production scheduling, ensuring seamless workflows.
This reduces delays, eliminates manual errors, and maximizes machine uptime. For instance, AI tools can analyze production capacity, order priority, and timelines to automatically create the most efficient production schedules. Additionally, managers can visualize timelines, assign tasks, and monitor progress for each order in real time.
This not only improves communication among teams but also ensures timely order completion, reducing missed deadlines and improving customer satisfaction.
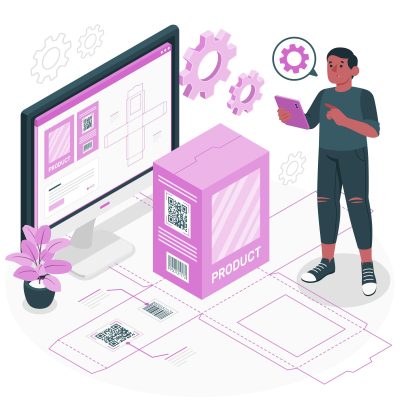
2] Seamless Order Processing: Processing orders manually often leads to errors in key details like fabric specifications, color codes, and quantities. The best apparel management software automates this process, ensuring accuracy and efficiency.
By integrating data entry, order tracking, and customer information, ERP for apparel minimizes human errors and accelerates the order fulfillment cycle. For example, manufacturers can use automation to validate order specifications against available inventory, ensuring immediate action is taken to procure missing materials.
This streamlined process reduces order turnaround times, boosts production efficiency, and results in higher customer satisfaction, ultimately increasing sales and revenue for the business.
3] Better Supplier Management: Supplier relationships play a crucial role in ensuring uninterrupted production. Apparel management software tracks supplier performance, lead times, order histories, and pricing trends, enabling businesses to make data-driven decisions.
For example, the software can provide insights into which suppliers deliver materials on time and which consistently cause delays. This allows manufacturers to optimize procurement strategies, negotiate better terms, and avoid production bottlenecks caused by late deliveries or inconsistent quality.
With better supplier management, businesses can ensure steady production, reduce costs, and maintain consistent product quality.
4] ESG Compliance and Sustainability: Sustainability is no longer optional; it’s a business imperative. Apparel software helps businesses monitor and improve their sustainability efforts by tracking key metrics like energy consumption, waste reduction, and ethical sourcing.
The software ensures compliance with labor laws, environmental standards, and customer expectations for sustainable practices. Additionally, real-time monitoring of energy use during production helps identify areas for improvement, reducing environmental impact.
By integrating ESG compliance into daily operations, apparel businesses can meet regulatory requirements, avoid legal complications, and build a strong reputation for sustainable practices.
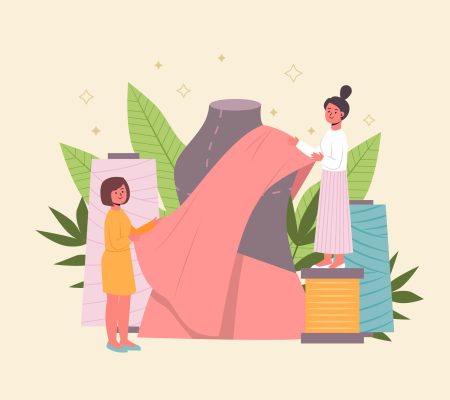
5] Streamlined Financial Management: Managing finances in a vast industry like apparel can be challenging. The best apparel management software simplifies this by automating financial tasks such as expense tracking, budget forecasting, and profit analysis.
Instead of manually compiling financial data from various departments, the software consolidates this information into easy-to-read reports. For instance, businesses can generate real-time cash flow statements or analyze cost-per-unit production without any manual effort.
This allows managers to make quick, informed financial decisions, allocate resources efficiently, and maintain long-term financial stability.
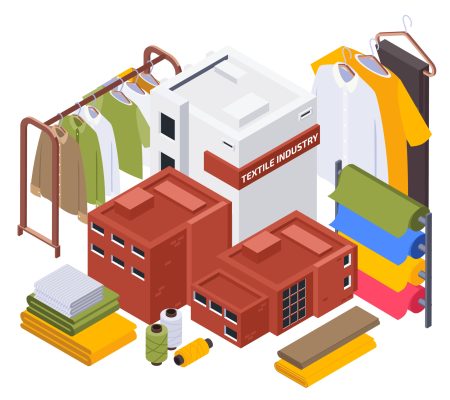
6] Real-Time Data for Decision Making: In an industry driven by rapidly changing trends, timely and accurate data is critical. Apparel management software collects data from every aspect of operations—sales, inventory, production, and customer feedback—and presents it through user-friendly dashboards.
For example, sales trends can be analyzed to predict future demand, while production costs can be monitored to identify areas where efficiency can be improved. This real-time visibility empowers decision-makers to adapt quickly to market changes, capitalize on emerging trends, and mitigate risks effectively.
Access to actionable insights enhances strategic planning and fosters innovation, keeping businesses ahead of the competition.
7] Efficient Inventory Management: Inventory mismanagement can lead to overstocking or stockouts, both of which negatively impact the bottom line. Apparel management solutions provide real-time visibility into stock levels, enabling businesses to forecast demand accurately and plan procurement accordingly.
The software uses predictive analytics to ensure optimal inventory levels, sending alerts when stock runs low or when certain items are overstocked. For instance, manufacturers can set reorder points for high-demand materials, ensuring timely replenishment.
By maintaining leaner inventory aligned with production needs, businesses can reduce carrying costs, avoid wastage, and improve cash flow.
8] Increased Scalability: As apparel businesses grow, managing larger orders, more suppliers, and complex workflows becomes increasingly challenging. A robust ERP for apparel is designed to scale seamlessly with business expansion.
For example, an apparel management software can handle increased transaction volumes, integrate with new sales channels, and support additional product lines without compromising performance. This scalability allows businesses to expand operations while maintaining efficiency, ensuring they can meet growing customer demands and explore new market opportunities.
9] Improved Quality Control: Maintaining high quality standards is essential, especially for businesses dealing with intricate designs and large-scale orders. Apparel management software integrates quality control checks at every stage of production, from raw material inspection to the final product.
For example, the software can flag materials that don’t meet quality standards or identify defects during the production process. This proactive approach ensures consistency, reduces returns, and enhances customer trust in the brand.
By minimizing defects and maintaining high-quality output, businesses can build a reputation for excellence and stand out in the competitive market.
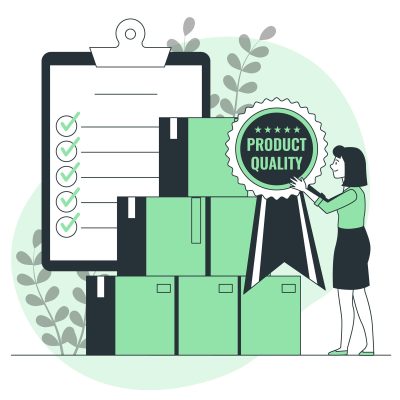
10] Improved Customer Satisfaction and Retention: With more customers expecting transparency and quick deliveries, apparel management software offers real-time updates on order status, shipping timelines, and inventory availability, creating a seamless customer experience.
For instance, customers can receive automated notifications about order progress, from production to delivery. This level of transparency builds trust and loyalty, encouraging repeat business.
By ensuring timely deliveries and clear communication, businesses can improve customer satisfaction, reduce churn, and foster long-term relationships.
The apparel industry demands efficiency, accuracy, and adaptability. Apparel management software addresses these needs by automating critical tasks, providing real-time insights, and integrating key operations into a unified platform.
From AI-driven production planning and streamlined order processing to better supplier management and enhanced quality control, these solutions empower businesses to thrive in a competitive landscape. By embracing ERP for apparel, companies can not only boost operational efficiency but also build stronger customer relationships and achieve sustainable growth.
Adopting the right software isn’t just a smart move; it’s a competitive necessity.
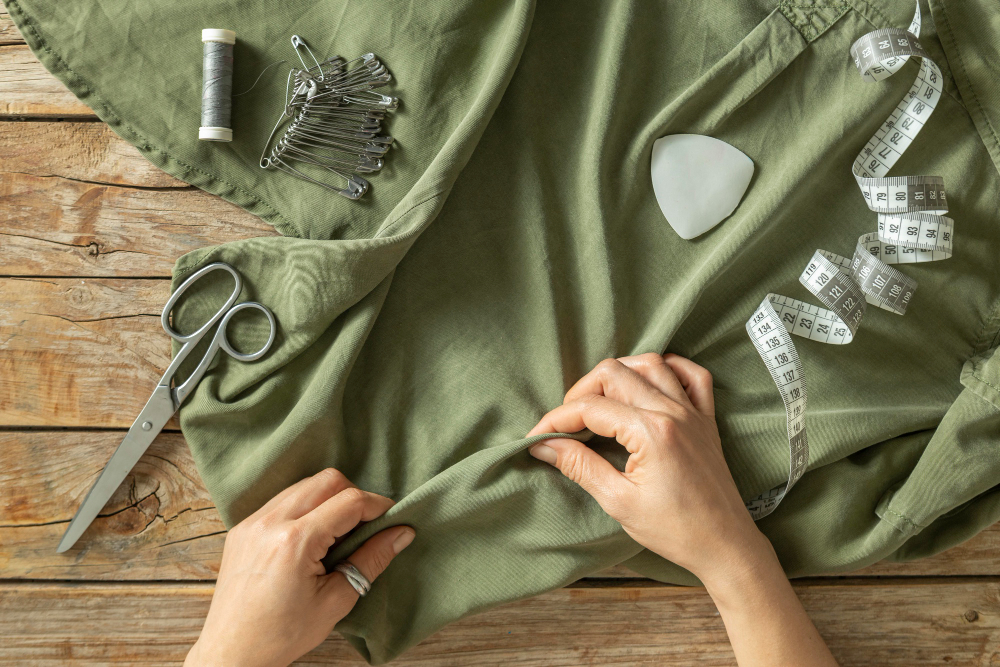
The textile industry has always been a cornerstone of global manufacturing, but it's also one of the most resource-intensive industries. As sustainability becomes a growing concern, textile manufacturers are under pressure to adopt eco-friendly practices. This shift towards sustainability is not just a trend; it’s a necessity.
To achieve these goals, many companies are turning to Enterprise Resource Planning (ERP) systems. ERP systems have the potential to revolutionize the way textile companies operate, making the combination of ERP and sustainable textiles a perfect match.
Why Sustainability Matters in the Textile Industry?
Sustainable textiles mean producing goods in a way that minimizes environmental impact, conserves resources, and reduces waste. The industry faces several challenges, such as excessive water usage, chemical pollution, energy consumption, and waste generation. Consumers and regulatory bodies are now demanding that companies reduce their carbon footprints and implement more sustainable practices.
As a result, textile companies are looking for solutions that can help them meet these expectations while maintaining productivity and profitability. This is where Eco-friendly ERP systems come into play. With the right ERP solution, textile manufacturers can streamline their operations, reduce waste, optimize resource usage, and move towards a more sustainable future.
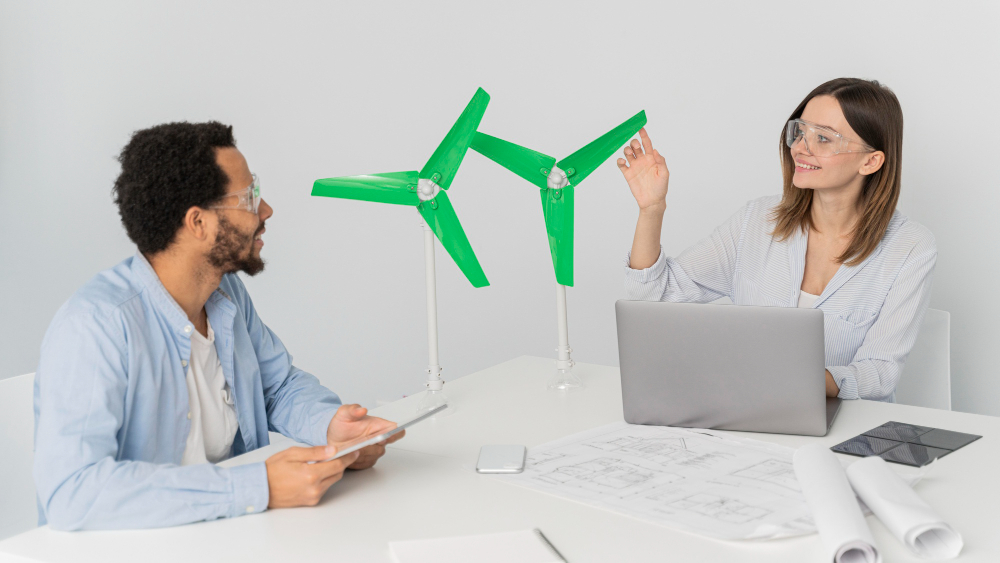
Role of ERP Systems in Producing Sustainable Textiles
An ERP system integrates various business processes into a unified platform, allowing for better control and visibility over all aspects of production. It supports sustainability by providing the tools needed to optimize operations, manage resources efficiently, and reduce waste.
Let’s explore how ERP systems contribute to sustainable textiles production:
1] Efficient Resource Management: ERP systems are designed to manage resources efficiently. In textile production, this means controlling the use of raw materials, energy, and water. By monitoring these resources in real-time, ERP systems help manufacturers identify areas where they can cut back on usage, reduce waste, and minimize their environmental impact. This level of control ensures that resources are utilized optimally, promoting sustainable textiles production practices.
2] Reduced Waste and Inventory Management: Waste reduction is a critical component of sustainability. Textile manufacturers often deal with excess inventory, fabric scraps, and defective products. An ERP system helps manage inventory levels accurately, preventing overproduction and reducing the amount of waste generated.
By providing a clear overview of inventory status and production needs, ERP systems ensure that manufacturers produce only what is necessary, minimizing fabric waste and cutting down on disposal costs. This approach supports sustainable textiles goals.
3] Energy Efficiency and Carbon Footprint Reduction: Energy consumption is a major concern in textile production. ERP systems can track energy usage across different stages of manufacturing, enabling companies to identify high-energy-consuming processes and optimize them for better efficiency. This not only reduces energy costs but also helps lower the carbon footprint of the production process. By adopting energy-efficient practices, textile manufacturers can move closer to their sustainability goals and sustainable textiles production.
4] Traceability and Transparency: One of the most significant benefits of using an ERP system is its ability to provide complete traceability of the production process. Textile companies can track the origin of raw materials, monitor production stages, and ensure compliance with environmental standards.
This transparency is crucial for meeting the demands of consumers who are increasingly concerned about the ethical and environmental impact of the products they buy. ERP systems make it easier for manufacturers to provide proof of sustainable textiles practices to their stakeholders.
5] Compliance with Environmental Regulations: The textile industry is subject to stringent environmental regulations, and non-compliance can result in heavy fines and damage to a company’s reputation. ERP systems help ensure compliance with these regulations by maintaining records of all production activities, waste management processes, and resource usage. This automated tracking reduces the risk of human error and makes it easier for companies to meet regulatory requirements, thus promoting sustainable textiles.
6] Sustainable Supply Chain Management: Sustainability isn’t limited to just production; it also extends to the entire supply chain. ERP systems facilitate better supply chain management by connecting manufacturers with sustainable suppliers, optimizing logistics, and reducing the carbon footprint associated with transportation.
By improving communication and collaboration with suppliers, ERP systems help textile companies make eco-friendly sourcing decisions that align with their sustainability objectives, ultimately contributing to green textile ERP solutions.
Benefits of ERP Sustainability for Textile Manufacturers
Integrating ERP systems with sustainability initiatives offers numerous benefits to textile manufacturers:
1] Cost Savings: Reduced resource consumption and waste lead to significant cost savings in the long run.
2] Improved Brand Image: Companies that adopt sustainable practices are viewed more favorably by consumers, enhancing their brand reputation.
3] Regulatory Compliance: Automated compliance tracking helps manufacturers stay updated with changing regulations and avoid penalties.
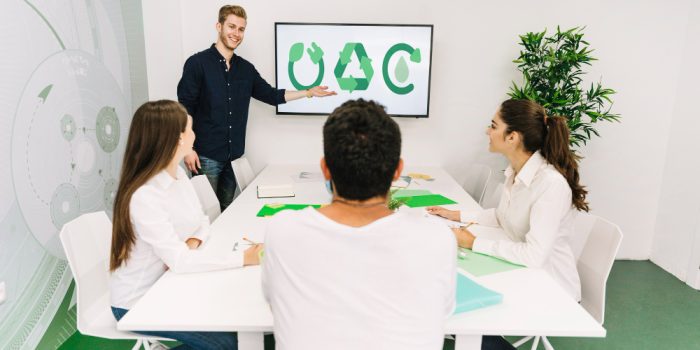
4] Increased Efficiency: ERP-driven production processes are more streamlined and efficient, boosting overall productivity.
5] Data-Driven Decision Making: With comprehensive data analytics, manufacturers can make informed decisions to improve sustainability in their operations.
ERP systems are becoming an indispensable tool for textile manufacturers striving to adopt sustainable practices. By enabling efficient resource management, reducing waste, ensuring compliance, and optimizing supply chains, ERP systems pave the way for a more eco-friendly and responsible textile industry.
The integration of ERP and sustainable textiles production is indeed a perfect match - one that promises a greener future for the industry.
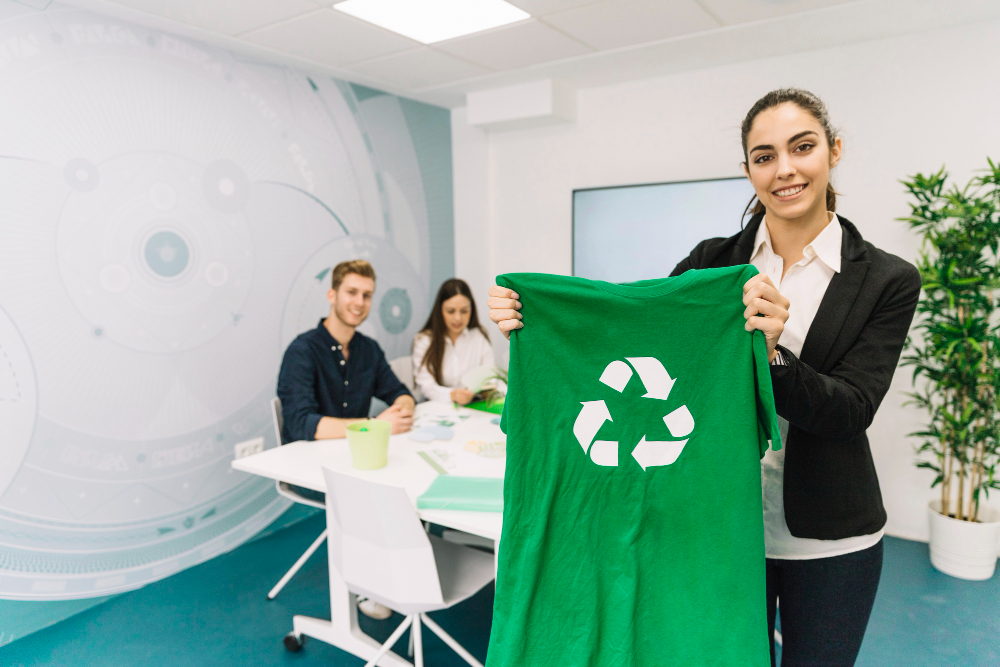
The textile industry produces 92 million tonnes of waste every year globally while being responsible for 10% of global carbon emissions. It is also believed, if not controlled, the textile industry will double its carbon emissions reaching 50% by 2030!
To control the amount of textile waste produced and reduce the industry’s contribution to carbon emissions, sustainability has taken center stage. Manufacturers across the globe are being urged to adapt to environmentally friendly practices in their manufacturing processes.
One of the most significant steps toward ensuring the textile industry becomes more sustainable is the implementation of Extended Producer Responsibility (EPR). As per this regulatory framework, as published by European Commission (EC) in July 2023, textile manufacturers are held accountable for the entire lifecycle of their products.
While EPR is reshaping how textile companies operate, it is challenging for manufacturers to comply to EPR regulations. This is where Enterprise Resource Planning (ERP) systems come into play.
In this article, we will explore how ERP systems can help textile manufacturers integrate sustainability into their core operations, comply with EPR regulations, and pave the way for a greener future.
Understanding EPR in Textile Industry
Landfilling and incineration have been common waste disposal methods used by the textile industry. However, these methods are no longer sustainable as they contribute significantly to environmental degradation.
The introduction of EPR in textile industry solves this problem!
This policy is designed to hold manufacturers responsible for the environmental impact of their products throughout their entire lifecycle. This includes everything from raw material sourcing and production processes to how products are disposed of or recycled once they reach the end of their useful life.
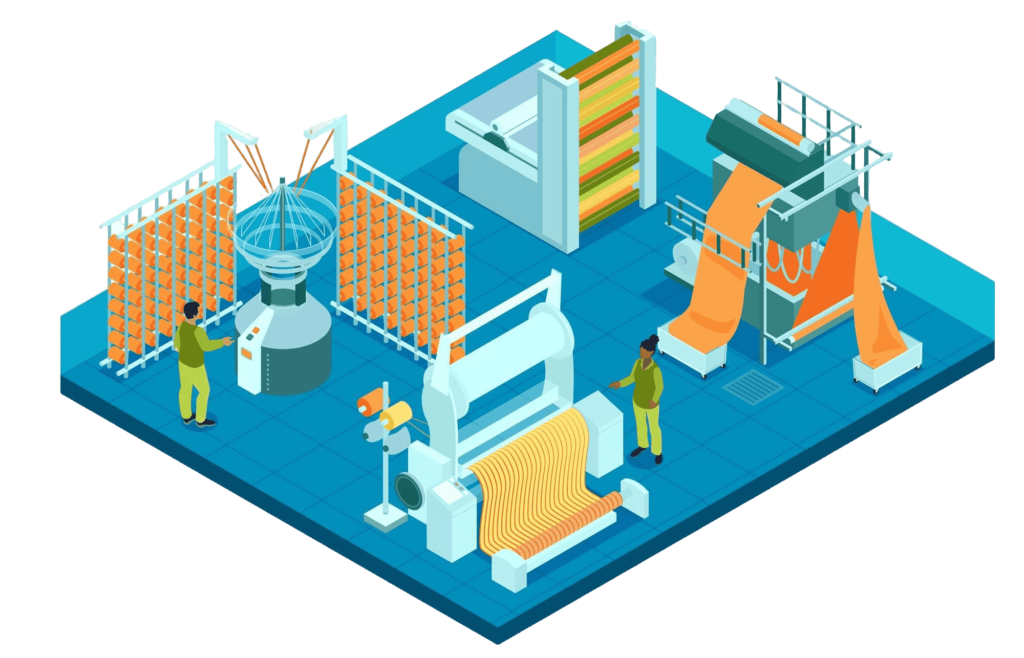
Consequently, manufacturers are now forced to find ways to minimize environmental harm, whether through recycling, repurposing materials, or reducing waste at the source. Textile manufacturers are also encouraged to design products with a longer lifespan, use materials that are easier to recycle, and implement more sustainable production techniques.
The implementation of the EPR policy has also made way for a shift from the linear “take-make-dispose” model to a circular economy. Under this, more sustainable materials are used for manufacturing, products are reused or repurposed, and most importantly – manufacturers are considering sustainability at every step of their operations.
Growing Momentum for Textile EPR in the USA
Textile waste in the USA has surged by 80% in weight since 2000, with only about 15% of discarded clothing recycled or reused. The remaining 85% is incinerated or landfilled. This contributes substantially to greenhouse gas emissions and environmental degradation.
California became the first US state to adopt an EPR program for textiles with the passage of Senate Bill 707. Signed by Governor Gavin Newsom in September 2024, this landmark legislation aims to reduce textile waste and promote recycling across the state.
The success of California’s EPR law could encourage similar national initiatives, creating a pathway toward unified EPR standards. By holding producers responsible for the entire lifecycle of their products, these policies support circular practices like recycling, repair, and resale, ultimately making sustainable options more accessible to businesses and consumers alike.
Challenges for Textile Manufacturers Under EPR
Before implementation of EPR framework, the disposal of textile waste rested with authorities. Thanks to the policy, this responsibility has now shifted to producers.
While EPR holds the potential for fostering innovation in recycling technologies, product design, and manufacturing processes – textile manufacturers face several challenges:
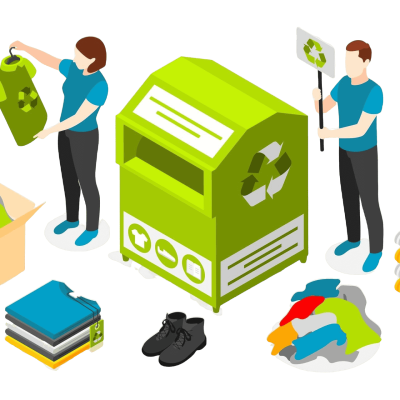
1] To ensure 100% compliance of EPR policies, manufacturers must have full visibility of their products. This requires accurate tracking of materials from sourcing to post-consumer disposal.
2] Companies must deal with the complexities of collecting, sorting, and recycling textiles, which often involves coordinating with third-party recyclers and managing reverse logistics.
3] Textile dyeing industries face challenges due to the discharge of large volumes of effluents containing harmful chemicals and dyes, requiring investment in sustainable dyeing practices and advanced wastewater treatment to comply with EPR regulations.
4] Consumer participation is crucial for EPR success, but awareness and engagement in sustainable behaviors remain limited.
Challenges for Textile Manufacturers Under EPR
An ERP for textile manufacturers is designed to streamline every aspect of the manufacturing process. It integrates data from all departments enabling business owners to get full visibility of their processes and take data-driven decisions.
ERP promotes sustainability across textile manufacturing operations by offering real-time insights and automated controls, making it easier for companies to meet their EPR obligations.
Some of the key ways in which ERP helps include:
1] Supply Chain Transparency: Offering increased transparency across the supply chain is at the core of an ERP system. Manufacturers get end-to-end visibility and easily track raw materials, production processes, and final products. As a result, companies can monitor the environmental impact at each stage and ensure sustainable sourcing practices.
2] Automated Waste Tracking: ERP systems automate the tracking of waste, helping textile companies measure and manage the discharge of harmful chemicals. With the help of this data-driven approach, manufacturers can easily comply with EPR guidelines on waste reduction and wastewater treatment.
3] Product Lifecycle Management (PLM): Manufacturers can seamlessly integrate ERP with a PLM tool to facilitate the monitoring of lifecycle of products – from design to post-consumer disposal. Therefore, they can improve recyclability, durability, and responsible disposal according to EPR goals.
4] Efficient Resource Management: An ERP software for textiles is a great help when it comes to optimizing resources such as water, energy, raw materials, etc., based on usage patterns. Reduction in resource wastage results in lowered environmental footprint for manufacturers helping them meet sustainability targets outlined in EPR policies.
5] Dedicated ESG Module: With the rising importance of sustainability in textiles, several ERP systems now come equipped with a dedicated ESG module. This module helps in tracking sustainability metrics, including carbon emissions, water usage, and waste reduction efforts. Textile manufacturers get a centralized platform using which they can monitor and report environmental impact, ensuring compliance with sustainability goals.
ERP in textiles will continue playing a vital role in driving sustainability. With growing consumer awareness and regulations becoming stricter, textile manufacturers must embrace innovation to meet compliance demands. ERP systems are at the forefront of this transformation, providing the necessary tools to streamline processes and enhance transparency throughout the supply chain.
The future of EPR in textiles relies on the integration of efficient systems like ERP. Adopting these solutions will help manufacturers not only comply with EPR requirements but also support the transition to a circular economy, ultimately leading to a more sustainable industry.
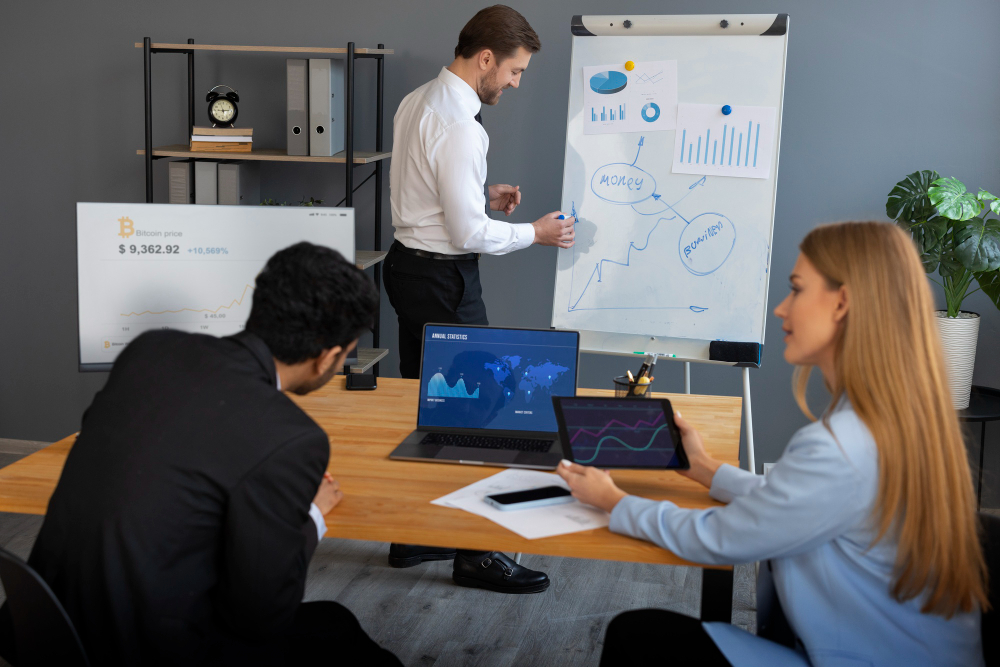
Studies show SMB’s (under $100 million in revenue) were slower in implementing their ERP than mid-sized businesses (between $100 million to $250 million in revenue), possibly due to less resources and expertise. These numbers indicate that ERP user adoption in textile industry is never an easy or a smooth process since the software is complex to handle at first.
This is one of the top ERP implementation challenges and it is an even bigger problem for businesses where the majority of staff and workers are undertrained for handling such software.
In an effort to bridge this gap, we are going to talk about 5 tips/methods you can use to ensure all team members have a complete understanding of the software. Training employees on ERP software also ensures that they are well-acquainted with their roles in its operation.
5 Ways to Ensure ERP User Adoption in Textile Industry
1] Communicate the Benefits Early and Clearly
One of the most important steps to getting your textile team onboard with a new ERP software is making sure they understand its benefits. Communication is key to overcoming ERP implementation challenges. Many employees might feel anxious about the new system, fearing that it will complicate their work or replace their role.
To ease these concerns, communicate the clear advantages the ERP software will bring, not only for the business but for their day-to-day tasks. For example, explain how ERP will simplify workflows, reduce repetitive tasks, and provide real-time insights that make decision-making easier. Highlight benefits like faster data entry, streamlined order tracking, and efficient inventory management.
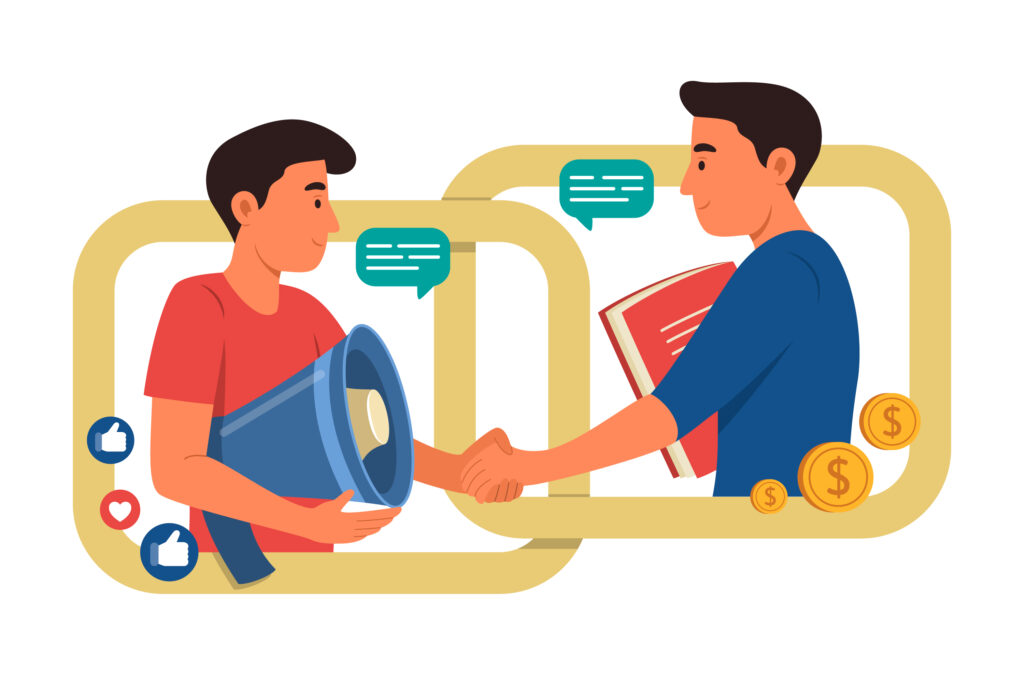
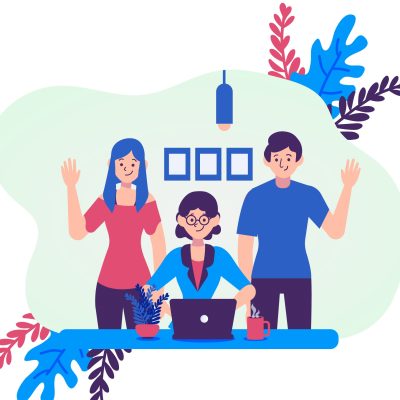
2] Involve the Team in the Selection and Implementation Process:
When your team feels involved in the decision-making process, they are more likely to take ownership of the change. Invite key team members to participate in the selection process of the ERP software. Their insights on daily operations can help identify the right solution that meets the specific needs of your textile business.
During the implementation phase, gather feedback from employees who will be using the system. This involvement not only boosts morale but also ensures higher chances of ERP user adoption in the textile industry. Your employees will believe that the chosen ERP software aligns with the practical needs of the team.
3] Provide Comprehensive Training and Support:
An ERP software will seem complex at first, and staff will need time and guidance to become comfortable with it. Plan a structured program that is customized for training employees on ERP software. You can even have custom-made programs for different roles within the team.
For instance, the production team may need in-depth training on modules related to manufacturing processes, while the finance team may require a focus on accounting and inventory management features. Hands-on, role-based training helps employees understand how the ERP system will impact their specific tasks.
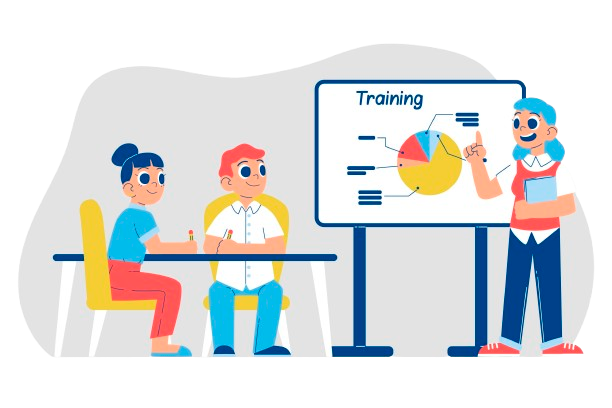
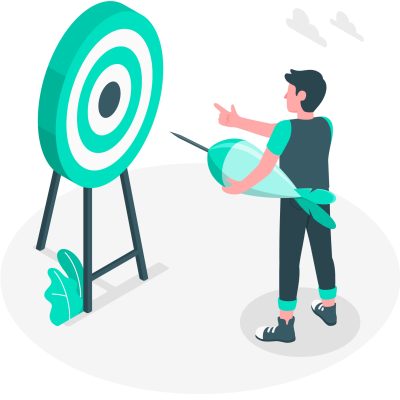
4] Set Realistic Expectations
During initial stages of onboarding your team, mistakes are bound to happen. The textile team will be trying to get a hold on the software, so setting realistic expectations for them will go a long way. Encourage patience and a willingness to learn, reminding the team that mastering the ERP software will take time.
As the textile team progresses through the onboarding stage, celebrate small wins. Whether it’s successfully completing the first production run with the ERP software or smoothly processing the first set of customer orders. Recognizing these achievements will help increasing ERP user adoption in the textile industry.
5] Appoint ERP Experts to Lead the Way
Recruiting an ERP expert to guide the textile team during onboarding process will be the best move to make to overcome ERP implementation challenges. An ERP expert will usually have years of understanding and experience with various ERP software solutions, so he/she will know how to guide the team through the entire process.
Hiring an ERP expert also helps the textile team to understand the product in an in-depth manner and make the right decisions along the way. For instance, team members can gain knowledge through the ERP expert rather than testing it out with the software themselves. This will optimize the whole onboarding process and provide the textile team a sense of direction to what they want to achieve.
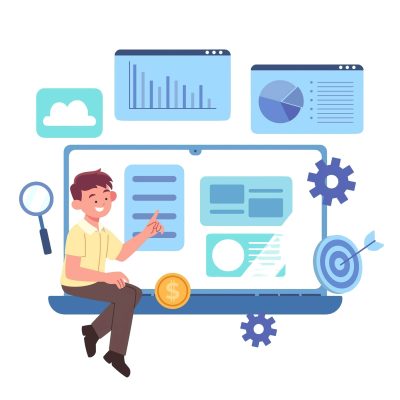
Training employees on ERP software and getting your team onboard with a new system takes effort, patience, and clear communication. By explaining the benefits early, involving the team in decisions, and providing proper training, you can ease the transition.
Setting realistic expectations and appointing an ERP expert will further help ERP user adoption in textile industry. Remember, it's normal for the team to take time to adjust, and recognizing their progress will keep morale high. With the right approach, your textile team will be confident and skilled in using the ERP system, making your business more efficient.
Contact Us
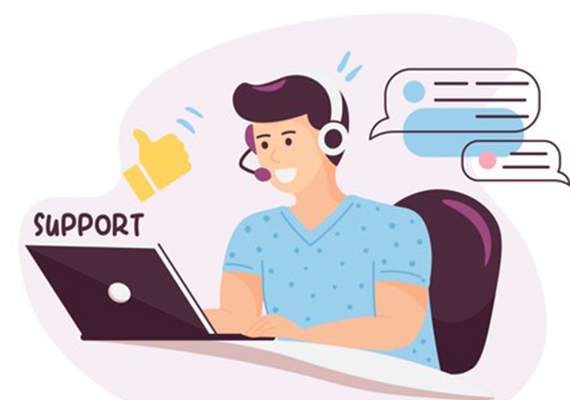