ERP Training and Development: Preparing Your Team for Success
It is widely said, – “Even the finest tool remains worthless in untrained hands.“
15-20% of ERP implementations fail due to lack of ERP training. No matter how good an ERP software is, if the users are unaware or untrained to use it then its implementation is likely to fail.
The textile industry comprises of many businesses that lack skilled employees to handle the advanced ERP software of their company. This may be due to lack of transitioning from traditional practices or a reluctance to transition from the legacy systems. In this blog we are going to understand the importance of ERP training and ERP team development, what value it brings and describe how an effective ERP training program should look like. Without further ado let’s get started!
Importance of ERP Training and Team Development
Textile ERP training and team development are necessary part of ERP success strategies. The textile industry is a traditional industry where many businesses have employees who are only educated with the traditional methods and not familiar with skills to use advanced ERP software. This makes it difficult for textile businesses to handle an ERP software efficiently.
To solve this, textile companies can invest in proper ERP training and development programs to educate their current workforce. By investing in quality training and development programs, textile companies can:
- Maximize ROI: Properly trained employees can make the most of the ERP software’s modules. This ensures that the investment in the software translates into tangible advantages.
- Boost Productivity: Training helps employees become efficient in using the software. This leads to faster task completion and reduces chances of errors.

- Easy Employee Transitioning: Training reduces the stress associated with learning new systems and demonstrates the company’s commitment to employee growth and success.
- Ensure Compliance and Standardization: Well-trained staff can adhere to standardized processes and compliance requirements, minimizing risks and enhancing consistency across the organization.
An Effective ERP Training Program
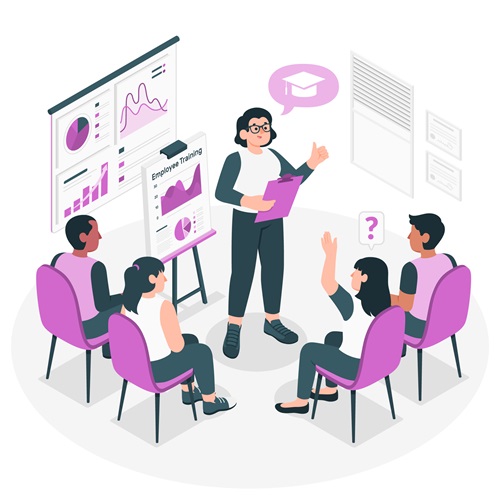
1. Needs Assessment
Before designing a training program, conduct a thorough needs assessment to identify the specific skills and knowledge gaps among your employees. This assessment should involve:
- Analyzing current workflows and processes: To identify areas that will be impacted by the ERP implementation.
- Surveying employees: To understand their current level of familiarity with ERP systems and any specific concerns they may have.
- Consulting with department heads and key stakeholders: To determine the critical functions and features of the ERP system that require focused training.
2. Customized Training Plans
Once the needs assessment is complete, develop customized training plans tailored to different user groups within your organization. These plans should address the unique requirements of each department and roles such as:
- Executives and Managers: Focus on high-level features such as data analytics, reporting, and strategic decision-making tools.
- Operational Staff: Emphasize day-to-day functionalities like inventory management, order processing, and production planning.
- Technical Team: Provide in-depth training on system configuration, troubleshooting, and maintenance.
3. Combined Learning Approach
Adopt a blended learning approach that combines various training methods to cater to different learning styles and preferences. This approach can include:
- Instructor-Led Training (ILT): Classroom sessions or virtual workshops led by experienced trainers to provide hands-on experience and real-time interaction.
- E-Learning Resources: Online courses and tutorials that allow employees to learn at their own pace and revisit topics as needed.
- On-the-Job Training: Practical, real-world training where employees can apply their knowledge under the guidance of a mentor or supervisor.
- Interactive Simulations: Simulated environments that mimic the ERP system’s interface, allowing employees to practice without the risk of impacting live data.
4. Performance Monitoring and Feedback
Track the progress and performance of your training program by collecting feedback from participants and monitoring key performance indicators (KPIs). This can include:
- Pre- and Post-Training Assessments: Evaluate employees’ knowledge and skills before and after training to measure improvement.
- Surveys and Feedback Forms: Gather input from trainees to identify areas for improvement and ensure the training meets their needs.
- Performance Metrics: Monitor KPIs such as system usage rates, error rates, and productivity levels to assess the impact of the training on overall performance.
5. Continuous Learning and Support
Training should not be a one-time event. To ensure long-term success, establish a culture of continuous learning and support by implementing:
- Refresher Training: Regularly scheduled training sessions to reinforce key concepts and introduce new features or updates.
- Knowledge Sharing: Encourage employees to share their experiences and tips through forums, discussion groups, or internal newsletters.
- Help Desk and Support: Provide ongoing access to technical support and troubleshooting resources to address any issues that arise post-implementation.
Successful ERP implementation in the textile industry depends heavily on effective textile ERP training and team development. Proper training ensures that employees can fully utilize the ERP system, maximizing ROI, boosting productivity, and ensuring compliance. By conducting a needs assessment, creating customized training plans, using a blended learning approach, monitoring performance, and fostering continuous learning, textile companies can overcome the challenges of transitioning from traditional methods to modern ERP systems. Investing in ERP training not only empowers employees but also drives the overall success of the business.